Domestic roof construction
Domestic roof construction is the framing and roof covering which is found on most detached houses in cold and temperate climates.[1] Such roofs are built with mostly timber, take a number of different shapes, and are covered with a variety of materials.
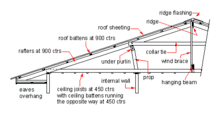
Overview
_00139_(23702821578).jpg.webp)
Modern timber roofs are mostly framed with pairs of common rafters or prefabricated wooden trusses fastened together with truss connector plates. Timber framed and historic buildings may be framed with principal rafters or timber roof trusses. Roofs are also designated as warm or cold roof depending on how they are designed and built with regard to thermal building insulation and ventilation. The steepness or roof pitch of a sloped roof is determined primarily by the roof covering material and aesthetic design. Flat roofs actually slope up to approximately ten degrees to shed water. Flat roofs on houses are primarily found in arid regions.[2]
In high wind areas, such as where a cyclone or hurricane may make landfall, the main engineering consideration is to hold the roof down during severe storms. Every component of the roof, as of course the rest of the structure, has to withstand the uplift forces of high wind speeds. This is accomplished by using metal ties fastened to each rafter or truss. This is not normally a problem in areas not prone to high wind or extreme weather conditions.
In the UK, a concrete tiled roof would normally have rafters at 600 mm (24 in) centers, roof battens at 300 mm (12 in) centers and ceiling joists at 400 mm (16 in) centers. The United States still uses imperial units of measurement and framing members are typically spaced sixteen or twenty-four inches apart.
The roof framing may be interrupted for openings such as a chimney or skylight. Chimneys are typically built with a water diverter known as a cricket or saddle above the chimney. Flashing is used to seal the gap between the chimney and roofing material.
Construction of a rafter roof
A simple rafter roof consists of rafters that the rafter foot rest on horizontal wall plates on top of each wall.[3] The top ends of the rafters often meet at a ridge beam, but may butt directly to another rafter to form a pair of rafters called a couple. Depending on the roof covering material, either horizontal laths, battens, or purlins are fixed to the rafters; or boards, plywood, or oriented strand board form the roof deck (also called the sheeting or sheathing) to support the roof covering. Heavier under purlins or purlin plates are used to support longer rafter spans. Tie beams, which may also serve as ceiling joists, are typically connected between the lower ends of opposite rafters to prevent them from spreading and forcing the walls apart. Collar beams or collar ties may be fixed higher up between opposite rafters for extra strength. The rafters, tie beams and plates serve to transmit the weight of the roof to the walls of the building
Construction of a truss roof
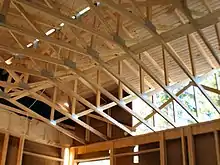
Pre-manufactured roof trusses come in a wide variety of styles. They are designed by the manufacturer for each specific building.
Timber trusses also are built in a variety of styles using wood or metal joints. Heavy timber rafters typically spaced 240 cm (8 ft) to 370 cm (12 ft) apart are called principal rafters. Principal rafters may be mixed with common rafters or carry common purlins.
Design loads
Roof framing must be designed to hold up a structural load including what is called dead load, its own weight and the weight of the roof covering, and additional loading called the environmental load such as snow and wind. Flat roofs may also need to be designed for live loads if people can walk on them. In the United States, building codes specify the loads in pounds per square foot which vary by region. The load and span (distance between supports) defines the size and spacing of the rafters and trusses.[4]
Roof covering
The roofing material is primarily designed to shed water. The covering is also a major element of the architecture, so roofing materials come in a wide variety of colors and textures. The primary roof covering on houses in North America are asphalt shingles, but some have other types of roof shingles or metal roofs. Tile and thatch roofs are more common in Europe than North America. Some roofing materials help reduce air conditioning costs in hot climates by being designed to reflect light.
Asphalt shingles is the most used roofing material in North America, making up as much as 75% of all steep slope roofs. This type of material is also gaining popularity in Europe due to lower installation costs. Asphalt shingles dominate the North American residential roofing market, because they typically less expensive[5] of other materials
In the southern US and Mexico, clay tile roofs are also very popular, due to their longevity, and ability to withstand hurricane winds with minimal or no damage.
In Europe, slate and tile roofs are very popular. Many slate roofs in Europe are over 100 years old, and typically require minimal maintenance / repairs.
Ventilation and insulation
Roof space ventilation is needed to combat condensation within the roof space, leading to interstitial condensation within the roof fabric; this can lead to serious structural damage, wet or dry rot, as well as ruining the insulation in the roof spec.
Condensation within the roof space is much more of a problem today due to: much less fortuitous ventilation due to tighter building envelopes with high performance windows and door and no chimneys leading. This tighter envelope means the air temperature in buildings has risen, the warmer the air in the building is, the more water vapour the air can carry.
As the occupied part of the building has become warmer, the roof space has become colder, with high performance insulation and roofing membranes leading to a cold roof space.
When the warm, moist air from below rises into the cold roof space; condensation begins as the air temperature drops to the ‘dew point’ or as the warm air comes into contact with any of the cold surfaces in the roof.
Most building materials are permeable to water vapour; brick, concrete, plaster, wood and insulation all can fall victim to interstitial condensation, this is why UK Building Regulations require roofs to be ventilated, either by the use of soffit vents, ridge vents, or replacement ventilation slates or tiles.[6]
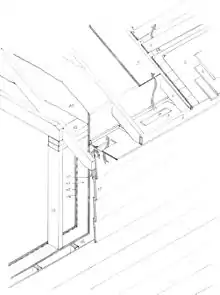
Ventilation of the roof deck speeds the evaporation of water from leakage or condensation and removes heat which helps prevent ice dams and helps asphalt shingles last longer. Building codes in the U.S. specify ventilation rates as a minimum of 1 sq ft (0.093 m2) of opening per 150 sq ft (14 m2) (1:150) with a ratio of 1:300 in some conditions.[7] Warm air rises, so ceiling insulation is designed to have a higher r-value and the insulation is often installed between the ceiling joists or rafters. A properly insulated and ventilated roof is called a cold roof. A warm roof is a roof that is not ventilated,[8] where the insulation is placed in line with the roof pitch.[9] A hot roof is a roof designed not to have any ventilation and has enough air-impermeable insulation in contact with the sheathing to prevent condensation[10] such as when spray foam insulation is applied directly to the under-side or top-side of the roof deck or in some cathedral ceilings.[11]
A more recent design is the installation of a roof deck with foil-backed foam along with a second deck that is air-gapped away from the foil-backed foam to allow air to flow vertically to a ventilation outlet at the peak of the roof—it is a double-deck design with an air gap. This design improves efficiency.[12]
Gallery
- A steeply pitched, timber framed roof under construction in Japan
- A heavy ridge beam and rafters. A tie or joist visible in foreground
- A set of trusses placed atop a home under construction
- A strongly reinforced roof structure in a cyclone-prone area
- Applying corrugated iron sheeting to a house under construction. Shows two gables and external cyclonic fastenings
- Example of architectural roof designs
- A hip roof construction in Northern Australia showing multinail truss construction. The blue pieces are roll formed metal roof battens or purlins. This roof is built with purpose-made steel hook bracket which is bolted to the truss with M16 bolt. The bracket is bolted to an M16 bolt cast in situ, embedded 300 mm (12 in) into the reinforced concrete block wall. This system is typically in place every 900 mm (35 in) around perimeter
See also
References
- "Domestic roof construction: what's involved? - The Manufacturer". The Manufacturer. Retrieved 2018-11-08.
- Marshall, D. & Worthing, D. (2000) The Construction of Houses. 3rd Edition. Estates Gazette London.
- "Roof Repairs 1 - The Rafters" (PDF). The Disaster Handbook, University of Florida. One Source Roofing. 1998. Retrieved 26 October 2014.
- "Domestic construction". www.commerce.wa.gov.au. Retrieved 6 May 2015.
- "12 Roofing Materials to Consider for Your House". The Spruce. Retrieved 2019-07-01.
- Tricker, Ray (2011-03-03). Building Regulations in Brief. doi:10.4324/9780080959160. ISBN 9780080959160.
- Petty, Stephen E.. Forensic engineering damage assessments for residential and commercial structures. Boca Raton, Fla.: CRC Press, Taylor & Francis Group, 2013. 447. Print.
- "Roof, non-ventilated" def. 1. Evert, Klaus. Encyclopedic dictionary of landscape and urban planning multilingual reference in English, Spanish, French and German. Berlin: Springer, 2010. 849. Print.
- "Warm roof" def. 1. Gorse, Christopher A., and David Johnston. A dictionary of construction, surveying, and civil engineering. Oxford: Oxford University Press, 2012. 482. Print.
- Dekorne, Clayton (2014, February). Insulating Cathedral Ceilings: Practical solutions to prevent call backs and boost energy performance, Journal of Light Construction 41-47.
- Kruger, Abe, and Carl Seville. Green building: principles and practices in residential construction. Clifton Park, N.Y.: Delmar Cengage Learning, 2013. 192. Print.
- "ORNL roof and attic design proves efficient in summer and winter". Oak Ridge National Laboratory. September 10, 2012.
External links
Media related to Roofs (structural systems) at Wikimedia Commons