Farrand & Votey Organ Company
Farrand & Votey Organ Company was a nineteenth-century manufacturer of pianos, reed and pipe organs, and player pianos located in Detroit, Michigan. It evolved from William R. Farrand and Edwin S. Votey, hence the name of Farrand & Votey. The company is the development of the old Detroit Reed Organ Company that was originally bought out in 1881. The Farrand & Votey Organ Company produced 7,200 instruments a year by 1889. The company made huge organs on special order contracts. In 1891 the company built a monumental 2,700 pipe organ for the Detroit's First Presbyterian Church. In 1893 it built a huge organ for the Chicago World's Fair, where it was played in recitals by world-renowned organists. In 1897 it built the nation's largest pipe organ. The company dissolved in 1897 and split up into two separate companies of the owners, each making their own style of organs.
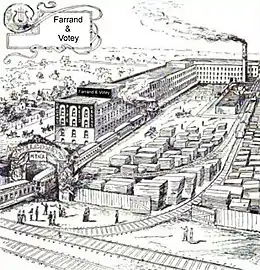
History
The origin of the Farrand & Votey Organ Company dates back to 1881 when the employee owned Detroit Reed Organ Company was dissolved.[1] Clark J. Whitney and Votey bought out the failed company and in 1883 organized as the Whitney Organ Company.[2] Whitney became the general manager, and Votey was its mechanical engineer in charge of designing organs. William R. Farrand joined this new company a few months after it was formed and became its financial manager as the secretary-treasurer. The company hired dozens of employees and manufactured reed organs. Whitney retired in 1887 selling his interest in the company to Votey and Farrand. The company was then renamed the Farrand & Votey Organ Company from Whitney Organ Company.[2]
In 1887, the company's officers were W.F. Raynolds, president, E. H Flinn, vice president, Farrand was treasurer and Votey was the company's secretary. They had a three-story factory built on Twelfth Street and the Grand Trunk Railway in downtown Detroit. The main factory building was shaped in the form of a large letter "L". It fronted on Twelfth Street and was 150 feet (46 m) long on the north side with a width of 40 feet (12 m) throughout the building. There was a separate building 40 feet (12 m) by 100 feet (30 m) which was used for engine and boiler rooms. There were grounds for materials and dry kilns. The facility had direct access to the railroad to receive deliveries of incoming materials as well as for shipping outgoing instruments.[3]
One hundred skilled workmen were employed by the company in 1887. At first, Farrand & Votey built only reed organs, but in 1888 it started making pipe organs and hired more men. The factory had the capacity to produce 600 pianos, organs, and mechanical piano players per month or 7,200 units per year.[4] The firm employed over 400 workers by 1905.[5] These instruments were sold throughout the United States and worldwide.[6][7] The Farrand & Votey Organ Company bought the business and patents of the Roosevelt Organ Works in 1889. It began making organs for the Aeolian Company around 1890. The first Aeolian Organ was installed in New York City's Aeolian Hall in 1893.[7] The partnership bought out the firm of Granville Pipe Organ Company in 1889.[7]
Merchandise
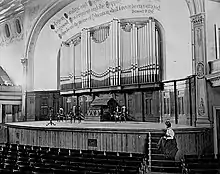
The firm sometimes constructed impressively large organs. They made one each for the Carnegie Library in Pittsburgh, the Pabst Theater in Milwaukee, and the First Church of Christ, Scientist in Boston.[7] A monumental 25-foot-long (7.6 m) 26-foot-high (7.9 m) pipe organ was produced for the First Presbyterian Church of Detroit in 1891 that had 2,700 pipes.[8] An enormous pipe organ, considered to be the largest in the nation at the time, was contracted for San Francisco's St. Ignatius Church in 1897 that had 5,000 pipes that were electrically operated for ease of operation.[9]
The company made an elaborate pipe organ for the 1893 Chicago World's Fair.[10] This massive organ was displayed in the Festival Hall at the fair, with a formal dedication on August 1, 1893. There were over 1,200 people in attendance.[11] World-renowned musicians, including the French organist and composer Alexander Guilmant, played recitals with the colossal organ.[7] The huge organ was played most often by Clarence Eddy, who was the organist at the First Congregational Church in Chicago.[11] There was an award given to the Farrand & Votey Organ Company by the World's Fair jury on musical instruments.[11] After the Chicago's World Fair the organ was taken apart and transported to the University of Michigan to be reassembled in 1894 and installed at University Hall becoming the Frieze Memorial Organ.[12][13]
Reed organ construction
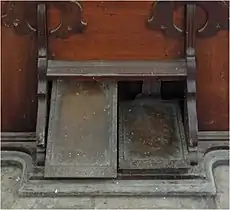
The old original Farrand & Votey reed organs were a mechanical instrument where the organist had to push the foot pedals alternately to make the organ work. There were two pedals just above floor level below the keyboard as they sat at the organ. They were a foot long by a half a foot wide each and located a few inches apart. The organist's feet rested on these two pedals and operated the organ with them. The pumping technique was to push one pedal down at a time and alternate between them on the pushing. When one pedal was depressed, the other one was not. When one pedal had been pushed down flat and level the other was up at about a 45 degree angle. The lowered pedal was then released by the organist's foot while the alternate pedal was depressed all the way down. The organist then had a pumping action with the two feet pushing down the pedals alternating between the two.[14]
When the foot pedals were pumped with the alternating action then the organ's two bellows passed compressed air over a set of reeds. The vibrating reeds then produced the sound. The pitch or the particular tone the reed made was dependent on the design shape of that particular reed.[15] This type of organ was commonly called a "pump organ" because the organist used a lot of energy working the foot pedals in a pumping action. No matter what an organist called the organ it technically was still a reed organ. The organist could control and vary the sound volume of the organ by how hard they operated these foot pedals. There several brass reeds used to create the sound of the organ.[16]
Pipe organ construction
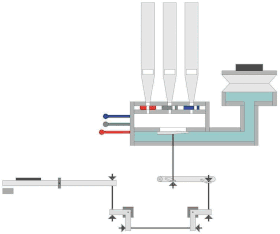
The sound of pipe organs come from the sounding device of pipes. The organ pipe is generally made out of wood or metal. The main body of a wooden pipe can be a softwood or a hardwood. The lower section of the pipe (comprising the foot, cap, block and mouth) is made from hardwood to provide a better connection for the pipe's mouth. The cross-section of a wooden pipe is most commonly square or rectangular, where the cross-section of a metal pipe is circular. The metals for pipe construction can include lead, copper, aluminium, gold electroplate, silver, brass, and iron. The most common metal organ pipe is made out of lead and a mix of tin with trace amounts other metals.[17]
The formula mix of the metal for the pipe determines the general tone and volume characteristics. The formula also determines the beauty characteristics as to how it looks to the audience. A sound is produced through the pipe by pressurized air forced through it. Each pipe produces a single pitch tone, dependent generally on its length. Each pipe is tuned to a specific note. A set of pipes grouped together with common characteristics are called ranks. Many of these are necessary to accommodate a musical scale which are controlled by organ stops. The greater the length of the pipe, the lower its resulting pitch will be. The loudness of the sound produced depends on the volume of air delivered to the pipe and how the pipe was constructed.[17]
The wind system consists of the parts that produce, store, and deliver pressurized air to the pipes. The system requires an adequate amount of wind that will be at just a little over atmospheric pressure. This pressurized air wind comes from bellows that are either hand operated or driven by a motor. Before the 19th-century the bellows had to be operated by assistants to the organist. The bellows became mechanized starting in the 1860s. The pressurized air supply is stored in windchests until a controlled action by the organist allows it to flow into particular set of pipes.[18]
Demise of Company
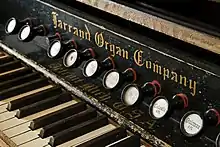
The Farrand & Votey Organ Company broke up amicably in 1897 and the pipe organ business became the Votey Organ Company.[19] The reed organ business went to Farrand.[2][20] The new firm was officially incorporated in 1901 and became the Farrand Organ Company.[21] It then added the Cecilian piano player to its line of products.[21] The unit came in three models in 1906 which were The Farrand-Cecilian Piano costing $675, The Cecilian Piano costing $500, and The Cecilian Piano Player costing $275.[22] The company was dissolved by 1914.[23]
Aeolian Company took over Votey Organ Company in 1899 and the Detroit factory manufacturing of pipe organs was relocated to Garwood, New Jersey. Then in 1901 the Votey pipe organ business was purchased by George Sherburn Hutchings and reorganized into Hutchings-Votey Organ Company of Boston.[24] The factory where they built the organs burned down in 1904.[25][26] The company moved its operations in 1906 to Cambridge, Massachusetts.[27] In 1908 it declared bankruptcy and went out of business.[28] Votey went back to Aeolian Company in New Jersey.[29] The old Hutchings-Votey Organ Company reorganized as the Hutchings Organ Company of Waltham, Massachusetts. It manufactured organs until the death of Hutchings in 1913.[28]
Current surviving organ installations
.jpg.webp)
at St. Martin of Tours Catholic Church
A pipe organ was built in 1895 for the Calvary United Methodist Church in Pittsburg that had electro-pneumatic action.[30] That organ was restored ninety years later in 1985.[31] It was still being used for concerts as of 2018.[32] The original construction of this organ followed the tradition in American organ building in the later part of the nineteenth century of reusing existing materials (i.e. pipes) already at the location (i.e. church, theater) from a previous organ installation. This organ was originally water powered.[33]
St. Martin of Tours Catholic Church has a Farrand & Votey organ that was originally built in 1894.[34][35] The organ in Louisville, Kentucky has been given the nickname "crown jewel."[36] The nineteenth-century organ with Latin inscribed polychromed pipes is the largest in the area. It received various improvements over decades from the time of the original installation. Sometime in the 1940s the original console was replaced. It was completely restored in 1991 by Miller Pipe Organ Company.[37]
A 3,000 pipe organ that had 49 ranks was purchased by Campbellsville University in 2007 from Christ Church of Nashville, Tennessee. The original 1894 Farrand & Votey organ constructed at Christ Church of Nashville was 15 ranks with additional ranks prepared for in the console and chambers. It has been rebuilt with two additional ranks added when installed at the Ransdell Chapel of the campus. It now has 51 ranks total.[38]
Brown University has a Hutchings–Votey organ with 56 ranks and over 3000 pipes. It was constructed in 1903 and has been renovated several times since then. According to Brown, it is the largest remaining Hutchings–Votey organ.[39]
Footnotes
![]() |
Wikimedia Commons has media related to Farrand & Votey Organ Company. |
- "Notices / Copartmership". Detroit Free Press. Detroit, Michigan. October 8, 1881. p. 5 – via Newspapers.com.
- "Farrand & Votey Organ Company". Pump Organ Restorations. Archived from the original on February 12, 2020. Retrieved January 20, 2020.
- Leonard 1887, p. 85.
- "Growth of Farrand & Votey Organ Company's business". The Morning Call. Allentown, Pennsylvania. January 20, 1889. p. 8 – via Newspapers.com.
- "Detroit Captains of Industry / William R. Farrand". Detroit Free Press. Detroit, Michigan. May 14, 1905. p. 42 – via Newspapers.com.
- "Farrand & Votey Organ Co". Detroit Free Press. Detroit, Michigan. September 10, 1895. p. 16 – via Newspapers.com.
- Ochse 1975, p. 295.
- "Opinions of the Press / Pipe Organ for the First Presbyterian Church". Detroit Free Press. Detroit, Michigan. June 28, 1891. p. 42 – via Newspapers.com.
- "A Magnificent Organ / St. Ignatius Church will have the Largest Instrument in the United States". San Francisco, California. February 29, 1896. p. 8 – via Newspapers.com.
- "Pianola Inventor Dies in Summit". The Brattleboro Reformer, page 1. Brattleboro, Vermont. January 26, 1931. Archived from the original on January 13, 2020. Retrieved January 20, 2020 – via Newspapers.com
.
- Abbott 1895, p. 271.
- Abbott 1895, p. 274.
- "Farrand & Votey Organ Co. Opus 700 (1893)". The Organ Historical Society. Retrieved April 5, 2020.
- "Proper Way to Operate the Foot Pedals". Pump Organ Restorations. Retrieved April 4, 2020.
- "Tuning the Reeds". Pump Organ Restorations. Retrieved April 4, 2020.
- "Is It Pump Organ, or Reed Organ?". Pump Organ Restorations. Retrieved April 4, 2020.
- Apel 1986, p. 579.
- Thistlethwaite 1998, pp. 18-20.
- "Important Changes / Farrand & Voteywill will make no more pipe organs". Detroit Free Press. Detroit, Michigan. October 9, 1897. p. 6 – via Newspapers.com.
- "The OHS Pipe Organ Database". The Organ Historical Society. Retrieved January 20, 2020.
- "Farrand Organ Company". Detroit Free Press. Detroit, Michigan. July 23, 1903. p. 21 – via Newspapers.com.
- "You Can Play". The Los Angeles Times. Los Angeles, California. March 6, 1906. p. 17 – via Newspapers.com.
- "Judge Murphy". Detroit Free Press. Detroit, Michigan. December 12, 1914. p. 14 – via Newspapers.com.
- Ochse 1975, p. 296.
- Smith 1998, p. 464.
- "Narrow Escapes; Several Injured /Artists Flee From Flames / Hutchings-Votey Organ Factory Burned". The Boston Globe. Boston, Massachusetts. November 12, 1904. p. 1 – via Newspapers.com.
- Advance 1906, p. 188.
- Bush 2006, p. 265.
- "The OHS Pipe Organ Database". The Organ Historical Society. Retrieved April 4, 2020.
- "A Fine instrument". Pittsburgh Press. Pittsburgh, Pennsylvania. June 4, 1895. p. 9 – via Newspapers.com.
- "'Early Autumn Recital' to feature IUP organ alumni". Indiana Gazette. Indiana, Pennsylvania. November 1, 1985. p. 32 – via Newspapers.com.
- "Pipe Organ Concert at Calvary UMC (Northside)". WQED Multimedia. Retrieved April 3, 2020.
- "THE HISTORIC PIPE ORGANS / The Farrand & Votey Organ (1895)". Pump Organ Restorations. Retrieved April 6, 2020.
- "Music Review / Organ Historical Society". The Courier-Journal. Louisville, Kentucky. July 23, 1993. p. 29 – via Newspapers.com.
- "Society showcases pipe organs' mettle through the pedal". The Courier-Journal. Louisville, Kentucky. July 11, 1993. p. 95 – via Newspapers.com.
- "Organ expert chooses handful of area's finest / St. Martin of Tours". The Courier-Journal. Louisville, Kentucky. April 9, 2006. p. 42 – via Newspapers.com.
- Kleber 2015, p. 705.
- "Farrand & Votey Organ Installed in Ransdell Chapel". Scranton Gillette Communication. Retrieved April 5, 2020.
- "About the Sayles Hall Hutchings–Votey (1903) Organ". Retrieved 2020-11-04.
Sources
- Abbott, Frank D. (1895). Musical Instruments - World's Columbian Exposition. Presto Company. p. 271.
- Apel, Willi (1986). The new Harvard dictionary of music. Belknap Press of Harvard University Press. ISBN 9780674615250.
- Advance (1906). The Advance, Volume 51. Advance Company.
- Bush, Douglas Earl (2006). The Organ: An Encyclopedia. Psychology Press. ISBN 9780415941747.
- Kleber, John E. (2015). Encyclopedia of Louisville. University Press of Kentucky. ISBN 978-0813149745.
- Leonard, John William (1887). The Industries of Detroit. J.M. Elstner & Company.
- Ochse, Orpha (1975). History of Organ in U. S. Indiana University Press. ISBN 025320495X.
- Smith, Rollin (1998). Aeolian Pipe Organ Music. Organ Historical Society. ISBN 9780913499160.
- Thistlethwaite, Nicholas (1998). The Cambridge Companion to the Organ. Cambridge University Press. ISBN 0521575842.