Five-bar linkage
A five-bar linkage is a two degree-of-freedom mechanism that is constructed from five links that are connected together in a closed chain. All links are connected to each other by five joints in series forming a loop. One of the links is the ground or base.[1] This configuration is also called a pantograph,[2][3] however, it is not to be confused with the parallelogram copying linkage pantograph.
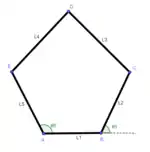
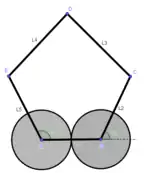
The linkage can be a single degree-of-freedom mechanism if two gears are attached to two links and are meshed together, forming a geared five-bar mechanism.[1]
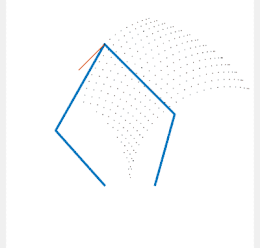
Robotic Configuration
When controlled motors actuate the linkage, the whole system (a mechanism and its actuators) becomes a robot.[4] This is usually done by placing two Servomotors (to control the two degrees of freedom) at the joints A and B, controlling the angle of the links L2 and L5. L1 is the grounded link. In this configuration, the controlled endpoint or end-effector is the point D, where the objective is to control its x and y coordinates in the plane in which the linkage resides. This robotic configuration is a parallel manipulator. It is a parallel configuration robot as it is composed of two controlled Serial manipulators connected to the endpoint.
Unlike a Serial manipulator, this configuration has the advantage of having both motors grounded at the base link. As the motor can be quite massive, this significantly decreases the total moment of inertia of the linkage and improves backdrivability for haptic feedback applications. On the other hand, workspace reached by the endpoint is usually significantly smaller than that of a serial manipulator.
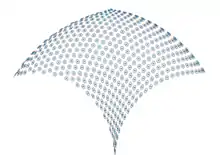
Kinematics and Dynamics
Both the forward and inverse kinematics of this robotic configuration can be found in closed-form equations through geometric relationships. Different methods of finding both have been done by Campion and Hayward.[2] Dynamic modeling of this robotic configuration has been done by Khalil and Abu Seif,[5] forming an equations of motion relating the torques applied at motor with the angles at the joints. The model assumes all links are rigid with center of gravity at their centers, and zero-stiffness at all joints.
Applications
This robotic linkage is used in many different fields ranging from prosthetics to haptic feedback. This design has been explored in several haptic feedback devices for general force feedback.[3][2] It has also been used in the automatic drawing toy WeDraw.[6] A novel Ackermann-type steering mechanism design by Zhao et. al. utilized a five-bar linkage instead of the regular four-bar linkage.[7] A prosthetic ankle-foot by Dong et. al. used a geared five-bar spring mechanism to simulate the stiffness and damping behavior of a real foot.[1]
References
- Dong, Dianbiao, et al. "Design and optimization of a powered ankle-foot prosthesis using a geared five-bar spring mechanism". International Journal of Advanced Robotic Systems 14.3 (2017): 1729881417704545. p. 3.
- Campion, Gianni. "The Pantograph Mk-II: a haptic instrument." The Synthesis of Three Dimensional Haptic Textures: Geometry, Control, and Psychophysics. Springer, London, 2005. 45-58.
- Yeh, Xiyang. "2-DOF Pantograph Haptic Device for General Educational Purposes". Collaborative Haptics and Robotics in Medicine Lab at Stanford University. Retrieved 1 June 2020.
- He, Dong; Zhihong Sun; and W. J. Zhang. "A note on inverse kinematics of hybrid actuation robots for path design problems". ASME 2011 International Mechanical Engineering Congress and Exposition. American Society of Mechanical Engineers Digital Collection, 2011.
- Khalil, Islam. "Modeling of a Pantograph Haptic Device" (PDF). Medical Micro & Nano Robotics Laboratory (MNRLab), Department of Mechatronics Engineering, German University in Cairo. Retrieved 1 June 2020.
- p-themes. "The Best Robot for kids". Wedrawrobot. Retrieved 1 June 2020.
- Zhao, Jing-Shan & Liu, Zhi-Jing & Dai, Jian. (2013). "Design of an Ackermann Type Steering Mechanism". Journal of Mechanical Engineering Science. 227. 10.1177/0954406213475980.