Perfluoroalkoxy alkane
Perfluoroalkoxy alkanes (PFA) are fluoropolymers. They are copolymers of tetrafluoroethylene (C2F4) and perfluoroethers (C2F3ORf, where Rf is a perfluorinated group such as trifluoromethyl (CF3)). The properties of these polymers are similar to those of polytetrafluoroethylene (PTFE). Compared to PTFE, PFA have better anti-stick properties, higher chemical resistance on expense of a lesser scratch resistance.[2] Other than in PTFE, the alkoxy substituents allow the polymer to be melt-processed. [3] On a molecular level, PFA have a smaller chain length and higher chain entanglement than other fluoropolymers. They also contain an oxygen atom at the branches. This results in materials that are more translucent and have improved flow, creep resistance, and thermal stability close to or exceeding PTFE.[4] Thus, PFA are preferred when extended service is required in hostile environments involving chemical, thermal, and mechanical stress. PFA offer high melt strength, stability at high processing temperatures, excellent crack and stress resistance, a low coefficient of friction.[1] Similarly advantaged processing properties are found in fluorinated ethylene propylene (FEP), the copolymer of tetrafluoroethylene and hexafluoropropylene.[5] However FEP is ten times less capable to withstand repeated bending without fracture than PFA.[1]
PFA | |
---|---|
![]() | |
Density[1] | 2150 kg/m3 |
Flexural modulus(E) | 586 MPa |
Tensile strength(t) | 24 MPa |
Elongation at break | 300% |
Folding endurance | No break |
Notch test | |
Melting point | 315 °C |
Maximum operating temperature | 260 °C |
Water absorption (ASTM) | <0.03 % after 24 hours |
Dielectric constant (Dk) at 1MHz | 2.1 |
Dissipation factor at 1MHz | 0.0001 |
Arc resistance | < 180 seconds |
Resistivity at 50% R. H. | > 1016 Ω m |
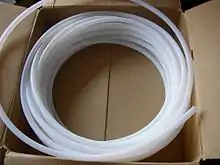
Common trademarks include Teflon-PFA, Hostaflon-PFA, and Chemfluor.[6]
Applications
PFA are commonly used as materials for piping and fittings for aggressive chemicals, as well as corrosion-resistant lining of vessels in the chemical-processing industry. Typical applications include the construction of gas scrubbers, reactors, containment vessels, and piping.[7] In coal-fired power plants, they are used as lining for heat exchangers. By channeling crude gas through a PFA-lined apparatus the gas stream can be cooled below its condensation temperature without damaging the heat exchanger. Its use contributes to increasing the efficiency of the whole plant.[8]
PFA are also used as inert materials for sampling equipment in analytical chemistry and for geochemical or environmental in situ studies on field site when it is particularly important to avoid chemical contamination of metallic ions at trace levels.
Precautions
At high temperatures or in a fire, fluoroelastomers decompose and may release hydrogen fluoride. Any residue must be handled using protective equipment.
References
- "PTFE, FEP, and PFA Specifications". Boedeker Corp. 2007. Retrieved 2007-12-22.
- "PTFE, FEP, PFA". TechnoFinish GmbH & Co. KG. Retrieved 2019-06-22.
- "PFA - Perfluoralkoxy". Reichelt Chemietechnik. Retrieved 2019-06-22.
- "PFA Properties". Fluorotherm Polymers. 2018. Retrieved 2018-11-04.
- Siegemund, Günter; Schwertfeger, Werner; Feiring, Andrew; Smart, Bruce; Behr, Fred; Vogel, Herward; McKusick, Blaine (2002). "Fluorine Compounds, Organic". Ullmann's Encyclopedia of Industrial Chemistry. Weinheim: Wiley-VCH. doi:10.1002/14356007.a11_349..
- "Glossary: PFA - Perfluoralkoxy". Reichelt Chemietechnik. Retrieved 2019-06-22.
- Dietrich Braun, Kunststofftechnik für Einsteiger, Hanser, München, 2003.
- H. Saechtling: Kunststoff Taschenbuch, Hanser Verlag, Wien 1995, ISBN 3-446-17855-4.