Phosphor bronze
Phosphor bronze is a member of the family of copper alloys. It is composed of copper that is alloyed with 0.5–11% of tin and 0.01–0.35% phosphorus, and may contain other elements to confer specific properties (e.g. lead at 0.5–3.0% to form free-machining phosphor bronze). Alloyed tin increases the corrosion resistance and strength of copper, while phosphorus increases its wear resistance and stiffness.[1]
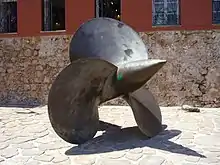
These alloys are notable for their toughness, strength, low coefficient of friction, and fine grain. The phosphorus reduces the viscosity of the molten alloy, which makes it easier and cleaner to cast and reduces grain boundaries between crystallites. It was originally formulated by the Belgian Georges Montefiore-Levi.[2]
Industrial uses
Phosphor bronze is used for springs, bolts, bushings and bearings, electrical switches with moving or sliding parts, dental bridges, the reed component of organ pipes and various other products or assemblies where resistance to fatigue, wear, and corrosion are required[3] (e.g., ship's propellers in a marine environment).[4]
Phosphor bronze comes in a wide array of standard alloys, including nonferrous spring alloys, free-machining phosphor bronze and bearing bronze. The combination of good physical properties, fair electrical conductivity, and moderate cost make phosphor bronze, available in standard round, square, flat, and special format wire desirable for many springs, electrical contacts, and a wide variety of wire forms where the desired properties do not require the use of more expensive beryllium copper.[4]
Phosphor bronze (94.8% copper, 5% tin, 0.2% phosphorus) is also used in cryogenics. In this application, its combination of fair electrical conductivity and low thermal conductivity allows the making of electrical connections to devices at ultra low temperatures without adding excessive heat.[5]
Spent nuclear fuel overpack
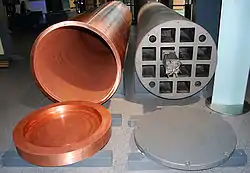
Oxygen-free copper can be alloyed with phosphorus (CuOFP alloy) to better withstand oxidizing conditions. This alloy has application as thick corrosion-resistant overpack for spent nuclear fuel disposal in deep crystalline rocks.[6]
UNIVAC computer
Magnetic tape was first used to record computer data in 1951 on the Eckert-Mauchly UNIVAC I. The UNISERVO drive recording medium was a thin metal strip of 0.5-inch (12.7 mm) wide nickel-plated phosphor bronze. Recording density was 128 characters per inch (198 micrometre/character) on eight tracks at a linear speed of 100 in/s (2.54 m/s), yielding a data rate of 12,800 characters per second. Of the eight tracks, six were data, one was a parity track, and one was a clock, or timing track. Making allowance for the empty space between tape blocks, the actual transfer rate was around 7,200 characters per second. A small reel of mylar tape provided separation from the metal tape and the read/write head.
Musical instruments
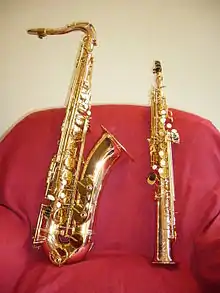
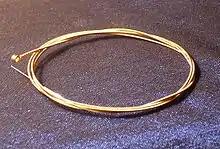
Phosphor bronze is preferred over brass for cymbals because of its greater resilience, leading to broader tonal spectrum and greater sustain.
Phosphor bronze is one of several high copper content alloys used as a substitute for the more common "yellow" or "cartridge" types of brass to construct the bodies and bells of metal wind instruments. Examples of instruments constructed using high copper alloys occur among members of the brass instrument family (trumpets, flugelhorns, and trombones) and one member of the reed instrument family, saxophones. In addition to the distinctive appearance provided by the reddish-orange hue of high copper alloys, they are purported by some instrument designers, sellers, and players to provide a broader harmonic response spectrum for a given instrument design. The Yanagisawa 902/992 model saxophones (pictured) have bodies of phosphor bronze, in contrast to the brass 901/991 models.
Some instrument strings for acoustic guitars, mandolins and violins are wrapped with phosphor bronze. Some harmonica reeds are made of phosphor bronze, such as those by Suzuki Musical Instrument Corporation and Bushman Harmonicas.[7]
The reed component of reed-type organ pipes is usually made of phosphor bronze owing to its high wear and low deformability under conditions of constant vibration when producing sound.[8]
Some snare drums are constructed with phosphor bronze.
Variants
Further increasing the phosphorus content leads to formation of a very hard compound Cu3P (copper phosphide), resulting in a brittle form of phosphor bronze, which has a narrow range of applications.
Around 2001, the Olin Corporation developed another alloy for use in electrical and electronic connectors which they referred to as "phosphor bronze".[9] Its composition was as follows:
- Zinc – 9.9%
- Tin – 2.2%
- Iron – 1.9%
- Phosphorus – 0.03%
- Copper – 85.97%
When assessed in strictly metallurgical terms it is not a phosphor bronze, but a form of iron-modified tin brass.
References
- Phosphor Bronze; Copper Development Association
- "Jews in Belgium". Archived from the original on 6 February 2008.
- Cavallo, Christian. "All About Phosphor Bronze". Thomas Network. Retrieved 12 March 2020.
- "Phosphor Bronze and Beryllium Copper". Little Falls Alloys. Retrieved 12 March 2020.
- "LakeShore". Archived from the original on 2011-05-03. Retrieved 2011-12-23.
- McEwan, Tim; Savage, David (1996). The Scientific and Regulatory Basis for Geological Disposal of Nuclear Waste. New York: J. Wiley & Sons. pp. See "Overpack" in index. Retrieved 1 February 2016.
- https://bushmanmusic.com/
- http://hardmanwurlitzer.com/pipes/
- "Innovations: Phosphor Bronze: Teaching an Old Dog New Tricks". Copper.org. Retrieved 2010-03-20.