Selective catalytic reduction
Selective catalytic reduction (SCR) is a means of converting nitrogen oxides, also referred to as NO
x with the aid of a catalyst into diatomic nitrogen (N
2), and water (H
2O). A reductant, typically anhydrous ammonia, aqueous ammonia or urea solution, is added to a stream of flue or exhaust gas and is absorbed onto a catalyst. As the reaction drives toward completion, carbon dioxide, CO
2 is produced.
Selective catalytic reduction of NO
x using ammonia as the reducing agent was patented in the United States by the Engelhard Corporation in 1957. Development of SCR technology continued in Japan and the US in the early 1960s with research focusing on less expensive and more durable catalyst agents. The first large-scale SCR was installed by the IHI Corporation in 1978.[1]
Commercial selective catalytic reduction systems are typically found on large utility boilers, industrial boilers, and municipal solid waste boilers and have been shown to reduce NO
x by 70-95%.[1] More recent applications include diesel engines, such as those found on large ships, diesel locomotives, gas turbines, and even automobiles.
SCR systems are now the preferred method for meeting Tier 4 Final and EURO 6 diesel emissions standards for heavy trucks, and also for cars and light commercial vehicles. In many cases, emissions of NOx and PM (Particulate Matter) have been reduced by upwards of 90% when compared with vehicles of the early 1990s.
Chemistry
The NO
x reduction reaction takes place as the gases pass through the catalyst chamber. Before entering the catalyst chamber the ammonia, or other reductant (such as urea), is injected and mixed with the gases. The chemical equation for a stoichiometric reaction using either anhydrous or aqueous ammonia for a selective catalytic reduction process is:
With several secondary reactions:
The reaction for urea instead of either anhydrous or aqueous ammonia is:
The ideal reaction has an optimal temperature range between 630 and 720 K, but can operate from 500 to 720 K with longer residence times. The minimum effective temperature depends on the various fuels, gas constituents, and catalyst geometry. Other possible reductants include cyanuric acid and ammonium sulfate.[2]
Catalysts
SCR catalysts are made from various ceramic materials used as a carrier, such as titanium oxide, and active catalytic components are usually either oxides of base metals (such as vanadium, molybdenum and tungsten), zeolites, or various precious metals. Another catalyst based on activated carbon was also developed which is applicable for the removal of NOx at low temperatures.[3] Each catalyst component has advantages and disadvantages.
Base metal catalysts, such as the vanadium and tungsten, lack high thermal durability, but are less expensive and operate very well at the temperature ranges most commonly seen in industrial and utility boiler applications. Thermal durability is particularly important for automotive SCR applications that incorporate the use of a diesel particulate filter with forced regeneration. They also have a high catalysing potential to oxidize SO
2 into SO
3, which can be extremely damaging due to its acidic properties.[4]
Zeolite catalysts have the potential to operate at substantially higher temperature than base metal catalysts; they can withstand prolonged operation at temperatures of 900 K and transient conditions of up to 1120 K. Zeolites also have a lower potential for potentially damaging SO
2 oxidation.[4]
Iron- and copper-exchanged zeolite urea SCRs have been developed with approximately equal performance to that of vanadium-urea SCRs if the fraction of the NO
2 is 20% to 50% of the total NO
x.[5]
The two most common catalyst geometries used today are honeycomb catalysts and plate catalysts. The honeycomb form usually consists of an extruded ceramic applied homogeneously throughout the carrier or coated on the substrate. Like the various types of catalysts, their configuration also has advantages and disadvantages. Plate-type catalysts have lower pressure drops and are less susceptible to plugging and fouling than the honeycomb types, but are much larger and more expensive. Honeycomb configurations are smaller than plate types, but have higher pressure drops and plug much more easily. A third type is corrugated, comprising only about 10% of the market in power plant applications.[1]
Reductants
Several reductants are currently used in SCR applications including anhydrous ammonia, aqueous ammonia or urea. All those three reductants are widely available in large quantities.
Anhydrous ammonia can be stored as a liquid at approximately 10 bar in steel tanks. It is classified as an inhalation hazard, but it can be safely stored and handled if well-developed codes and standards are followed. Its advantage is that it needs no further conversion to operate within an SCR and is typically favoured by large industrial SCR operators. Aqueous ammonia must be vaporized in order to be used, but it is substantially safer to store and transport than anhydrous ammonia. Urea is the safest to store, but requires conversion to ammonia through thermal decomposition[6] in order to be used as an effective reductant.[1]
Limitations
SCR systems are sensitive to contamination and plugging resulting from normal operation or abnormal events. Many SCRs are given a finite life due to known amounts of contaminants in the untreated gas. The large majority of catalyst on the market is of porous construction. A clay planting pot is a good example of what SCR catalyst feels like. This porosity is what gives the catalyst the high surface area essential for reduction of NOx. However, the pores are easily plugged by fine particulates, ammonium sulfate, ammonium bisulfate (ABS), and silicon compounds. Many of these contaminants can be removed while the unit is on line by ultrasonic horns or soot blowers. The unit can also be cleaned during a turnaround or by raising the exhaust temperature. Of more concern to SCR performance are poisons, which will degrade the catalyst and render it ineffective at NOx reduction, possibly resulting in the oxidation of ammonia which will increase NOx emissions. These poisons are halogens, alkali metals, alkaline earth metals, arsenic, phosphorus, antimony, chromium, lead, mercury, and copper.
Most SCRs require tuning to properly perform. Part of tuning involves ensuring a proper distribution of ammonia in the gas stream and uniform gas velocity through the catalyst. Without tuning, SCRs can exhibit inefficient NOx reduction along with excessive ammonia slip due to not utilizing the catalyst surface area effectively. Another facet of tuning involves determining the proper ammonia flow for all process conditions. Ammonia flow is in general controlled based on NOx measurements taken from the gas stream or preexisting performance curves from an engine manufacturer (in the case of gas turbines and reciprocating engines). Typically, all future operating conditions must be known beforehand to properly design and tune an SCR system.
Ammonia slip is an industry term for ammonia passing through the SCR unreacted. This occurs when the amount of ammonia injected is excessive, temperatures are too low for ammonia to react, or the catalyst has degraded.
Temperature is SCR's largest limitation. Engines all have a period during a start-up where exhaust temperatures are too cool for NOx reduction to occur, especially in cold climates.
Power plants
In power stations, the same basic technology is employed for removal of NO
x from the flue gas of boilers used in power generation and industry. In general, the SCR unit is located between the furnace economizer and the air heater, and the ammonia is injected into the catalyst chamber through an ammonia injection grid. As in other SCR applications, the temperature of operation is critical. Ammonia slip is also an issue with SCR technology used in power plants.
Other issues that must be considered in using SCR for NO
x control in power plants are the formation of ammonium sulfate and ammonium bisulfate due to the sulfur content of the fuel as well as the undesirable catalyst-caused formation of SO
3 from the SO
2 and O
2 in the flue gas.
A further operational difficulty in coal-fired boilers is the binding of the catalyst by fly ash from the fuel combustion. This requires the usage of sootblowers, sonic horns, and careful design of the ductwork and catalyst materials to avoid plugging by the fly ash. SCR catalysts have a typical operational lifetime of about 16,000-40,000 hours in coal-fired power plants, depending on the flue gas composition, and up to 80,000 hours in cleaner gas-fired power plants.
Poisons, sulfur compounds, and fly ash can all be removed by installing scrubbers can be installed before the SCR system to increase the life of the catalyst, though most plants' scrubbers are installed after the system.
SCR and EPA 2010
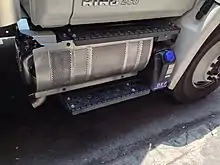
Diesel engines manufactured on or after January 1, 2010 are required to meet lowered NOx standards for the US market.
All of the heavy-duty engine (Class 7-8 trucks) manufacturers except for Navistar International and Caterpillar continuing to manufacture engines after this date have chosen to use SCR. This includes Detroit Diesel (DD13, DD15, and DD16 models), Cummins (ISX, ISL9, and ISB6.7), Paccar, and Volvo/Mack. These engines require the periodic addition of diesel exhaust fluid (DEF, a urea solution) to enable the process. DEF is available in bottles and jugs from most truck stops, and a more recent development is bulk DEF dispensers near diesel fuel pumps. Caterpillar and Navistar had initially chosen to use enhanced exhaust gas recirculation (EEGR) to comply with the Environmental Protection Agency (EPA) standards, but in July 2012 Navistar announced it would be pursuing SCR technology for its engines, except on the MaxxForce 15 which was to be discontinued. Caterpillar ultimately withdrew from the on-highway engine market prior to implementation of these requirements.[9]
BMW,[10][11] Daimler AG, and Volkswagen have used SCR technology in some of their passenger diesel cars.
See also
- Acid rain
- Catalytic converter, which also catalyzes NOx conversion but does not use urea or ammonia
- Diesel exhaust fluid (DEF) or AdBlue
- Exhaust Gas Recirculation versus Selective Catalytic Reduction
- Environmental engineering
- Selective non-catalytic reduction (SNCR)
- NOx adsorber (LNT)
- Vehicle emissions control
References
- Steam: Its Generation and Uses. Babcock & Wilcox.
- "Environmental Effects of Nitrogen Oxides". Electric Power Research Institute, 1989
- "Archived copy". Archived from the original on 2015-12-08. Retrieved 2015-11-27.CS1 maint: archived copy as title (link) CarboTech AC GmbH
- DOE presentation
- Gieshoff, J; M. Pfeifer; A. Schafer-Sindlinger; P. Spurk; G. Garr; T. Leprince (March 2001). "Advanced Urea Scr Catalysts for Automotive Applications" (PDF). Society of Automotive Engineers. Retrieved 2009-05-18.
- Kuternowski, Filip; Staszak, Maciej; Staszak, Katarzyna (July 2020). "Modeling of Urea Decomposition in Selective Catalytic Reduction (SCR) for Systems of Diesel Exhaust Gases Aftertreatment by Finite Volume Method". Catalysts. 10 (7): 749. doi:10.3390/catal10070749.
- "Hino Standardized SCR Unit". Hino Motors. Archived from the original on 5 August 2014. Retrieved 30 July 2014.
- "The DPR Future" (PDF). Hino Motors. Retrieved 30 July 2014.
- "Caterpillar exits on-highway engine business". Today's Trucking. Jun 13, 2008. Retrieved 29 December 2017.
- http://www.bmw.com/com/en/owners/service/care/_downloads/BMW-BluePerformance-AdBlue-Eng.pdf
- http://www.bmw.com/com/en/owners/service/care/checkup_and_maintenance/maintenance/adblue.html