Ultrasonic antifouling
Ultrasonic antifouling is a technology that uses high frequency sound (ultrasound) to prevent or reduce biofouling on underwater structures, surfaces, and medium. Ultrasound is just high frequency sound (which humans can not hear). Ultrasound has the same physical properties as human-audible sound. The method has two primary forms: sub-cavitation intensity and cavitation intensity. Sub-cavitation methods create high frequency vibrations, whilst cavitation methods cause more destructive microscopic pressure changes. Both methods are shown to inhibit or prevent biofouling by algae and other single-celled organisms.
History
This term comprises at least two topics: ultrasonic (ultrasound) and antifouling (biofouling):
- Ultrasound has been known about since 1794 when an Italian physiologist and biologist named Lazzarro Spallanzani discovered that bats navigate in the dark through the reflection of high frequency sounds. [1] Ultrasonic antifouling is believed to have been discovered by the US Navy in the 1950s . During sonar tests on submarines, it is said that the areas surrounding the sonar transducers were cleaner of fouling than the rest of the hull .
- Antifouling (the removal of biofouling) has been a desire of sailors for what feels like forever. "Coating technology has been applied to ships and vessels since very ancient times, either to protect the wood from shipworms or to prevent fouling. The first materials to be used were natural products like waxes, tar or asphalt. Later on, copper and lead sheathings were introduced by the Phoenicians and Carthaginians."[2] There is the oft quoted example of how the British Royal Navy recognised the benefit of copper sheathing on their wooden hulls to prevent worms and other organisms deteriorating their boats [3] The Cutty Sark is one example of such copper sheathing, available to view in Greenwich, England.
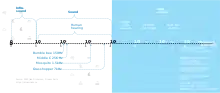
Theory
Ultrasound
Ultrasound (ultrasonic) is just sound at a high frequency such that human's can not normally hear it.[4] There is nothing different about ultrasound compared to sound than its frequency. As we know, sound has a frequency (low to high) and an intensity (quiet to loud).
Ultrasound is familiar in many household and industries [5] as a technique to: clean fine jewellery, weld rubber, treat absesses, and perhaps most famous of all, sonography permitting the observation of a fetus in the womb. All these techniques rely on a physical interaction of sound with the mediums through which the sound travels. In maritime application, ultrasound is the key ingredient in sonar; sonar relies on ultrasound.
It is the intensity of sound that causes the impact on media. Ultrasound can be so gentle as to blow out a candle[6] or so intense as to fuse together materials,[7] and more. There is therefore, clearly, a difference between the sound in sonography and ultrasonic welding. Indeed, bats use ultrasound and these clearly are not of a high power.
Biofouling starts with biofilms
Biofouling starts small; it's a small issue which could simply be wiped away with a soft cloth, but quickly worsens as the habitat created by one organism permits, attracts, or otherwise leads to another "The fouling process starts from the moment the surface is immersed in water and takes place in three main stages: formation of a conditioning film, microfouling and macrofouling"[2] "The combination of the conditioning film and the slime of living and dead bacteria cells generates the first stage of microfouling, so-called the primary film."[2]
.jpg.webp)
_-_Control_box_%2526_Transducer.jpg.webp)
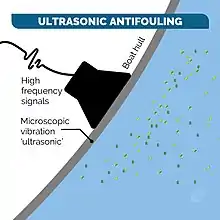
Ultrasonic Antifouling
In the references here, there are at least two views about sound used in ultrasonic antifouling:
- Cavitation intensity power antifouling: The ultrasound is of such a high intensity that the water boils with cavitation. The biofilm and organisms are annihilated. This type has been shown to remove established marine biofouling. With these high intensities of ultrasound there can be concerns as to the effect on the hull, not just the water and biofilm touching the hull. Acoustic cavitation[8] can be predicted theoretically through the calculation of acoustic pressure and where this pressure is low enough, the liquid can reach its vaporisation pressure. This results in localised vaporisation of the liquid, forming small bubbles; these collapse quickly and with tremendous energy and turbulence, generating heat on the order of 5000K and pressures of the order of several atmospheres.[9] Such systems are more appropriate where power consumption, and the surfaces-to-be-protected can tolerate highly destructive cavitation.
- Sub-cavitation intensity power antifouling: The ultrasound causes vibration in the surfaces (e.g. hull, propeller shafts, rudders, sea chests, water coolers) to which the transducer is attached. At lower intensity levels, the rapid vibrations, creates small movements of the surrounding water, making it extremely difficult for marine life to firmly attach to a surface, and even to exist and function. This type works best to maintain a clean hull; such as inhibiting the settlement of barnacle cyprids.[10] The disturbance of this first stage "biofilm" with even a subtle intensity of ultrasound reduces or removes the entire sequence of upper stages which are the cause of so much trouble for the boat owner. For sailing yachts, where power is a limited resource, especially when not connected to shore power, such low power systems are more appropriate.
The effectiveness of different frequencies and intensities (or power) of ultrasonic waves on various marine life, such as barnacles,[10] mussels and algae.
Commercial ultrasonic systems have been used to control algal blooms in ponds, harbours and reservoirs.[11] In controlling the algae, the first stage in the fouling sequence is halted, acting as a prevention, rather than a cure as with traditional anti-fouling paint.
The Appeal of Ultrasonic Antifouling
The main reason ultrasonic antifouling has so much interest is:
- It offers continuous stable protection instead of gradually wearing out as do antfouling coatings and paints
- It is fitted on the inside of a boat hull and therefore requires no external access, dry docking or lifting of the boat
- It is modular and scalable to all sizes of boats. Each transducer has a defined radius of influence e.g. 10m radius (300m^2) and can be positioned to ensure complete coverage, or even extra coverage of different surfaces.
- The power consumption is appropriate to the vessel size: small vessels which rely on stored battery power only require a few transducers, whilst commercial vessels which require many more transducers or higher power transducers have onboard generators. Small vessels may even use wind and solar energy to power such systems.
- It has a low single cost compared to the annual repeated costs of antifouling paints.
- Above all, it is sustainable: fit once, can be of low power consumption, and no polluting chemicals (biocides) are used in operating.
Components of an Ultrasonic Antifouling System
There are two main components of an ultrasonic antifouling system:

- Transducer, or in human audible terms, a speaker. A speaker, like a transducer, is just a device that takes an electrical control signal and vibrates the medium in which it is located. Thus, a speaker normally vibrates the air in order to propagate sound such as music or voices. The term transducer is used in more engineering based discussion, and in this case since the medium is water (sea water) then the vibration from the transducer propagates through the water. The transducer is in such firm and direct contact with the hull or other surfaces that it causes them to propagate the (ultra)sound. Hull materials such as concrete and wood do not provide good antifouling since they contain many voids which dissipate and absorb the sound. "The transducers are directly fixed to the inside of the boat hull"[12] with a firm bond to the inside surface of the boat hull or attached to other items such as propeller shafts, sea chests, pipework etc., such that the ultrasound radiates from the surface of the item to be protected from fouling. An installed transducer is shown in the images on this page,
- Control box, or in music terms the sound source and amplifier, provides the signals and power to each transducer. A control box might control multiple transducers with either the same signal or a variation, depending on the control box, "Each system includes a Control Box with status LEDs and 1 to 4 Transducer units".[12] The control box is positioned in any convenient location such that power is easily connected and future access is possible.
Between the two is often standard single-core 'satellite' cable.
Modern usage
Modern commercial systems are available in a wide range of powers and installation variants, however all use similar ceramic piezoelectric transducer as the ultrasound source. There are dedicated systems for:
- Pool cleaning (to reduce chemicals necessary to prevent algae blooms)
- Ship hull protection (to prevent fouling, increasing speed and reducing fuel costs)
- Heat exchanger protection (to extend operational cycles between cleaning)
- Seachest / water intakes (to prevent blockages by marine growth) [13]
- Fuel tank protection (to stop algae growth and prevent diesel contamination)
- Protection of offshore structures (such as wind farms, oil & gas installations etc.)
- HVAC Cooling Towers to reduce or eliminate chemical dosing treatment
- Propeller Shafts and Propellers [14]
However, most of these systems are controlled by fairly simple variable-frequency drive units, which run random frequencies in the ultrasonic spectrum of 20–45 kHz over an operational cycle. Intelligent systems will target specific frequencies, as well as manage power consumption, protect batteries & power supplies and come with various other features and options such as remote monitoring, alarm systems and daylight sensors. Several companies have patents on their intelligent systems
Some systems will actually automatically calibrate after installation and target the ideal frequency range for the substrate to maximize effectiveness.[15][16]
Limitations
Effectiveness
Ultrasonic anti-fouling may be considered a complete replacement for traditional anti-fouling paints; as well as a preventive measure to deter marine growth from a surface. There is so much latitude in the installation of an ultrasonic antifouling system from:
- the frequencies used,
- the intensity of the ultrasound,
- the location of each transducer,
- the water temperature and salinity, as well as
- the type of organisms in the water,
that some trial and error might be required before complete antifouling is achieved.
In review of the effectiveness of installation on a 34 foot sailing yacht "...
Established Methods
There is a large vested interest from boat yards and boat maintenance companies to sell and provide the current antifouling paints and coatings which are required each annum rather than the single-install ultrasonic antifouling systems. Ultrasonic antifouling systems are now cost competitive, thanks to production efficiencies and established designed, that they out perform the cost of antifouling coatings, and indeed are a DIY option for the average sailor who is accustomised to performing their own repairs and installs.
Hull Materials
Ultrasonic systems cannot work on wooden-hulled vessels, or vessels made from ferro-cement. Vessels with foam or wooden cored composite hulls will require modification to the hull in the specific locations that the transducers are to be installed. Ultrasonic systems will work with reduced effectiveness on vibration isolated fittings, such as sterndrives. This is because the hull must pass the ultrasound waves from the transducer located inside the hull through to the water, and these materials act to dampen the amplitude of ultrasonic waves.
Applications
Sites and structures using ultrasonic antifouling include:
- 34 foot sailing yacht hull [17]
- HVAC Cooling Tower full scale trial results[18]
- Tholen Harbour, the Netherlands[19]
- Longham lakes, UK[20]
- 3x MOD Mk IV LCVP landing craft trial[21]
- Kippari magazine test boat[22]
- Moody 36 ‘Dalriada’[23]
- Alloy Yachts ‘Mondango 3’[24]
- Dredgers[25]
- Coast Guard & Patrol Boats [26]
- Propeller Shafts & Propellers [27]
References
- "The History of Ultrasound". Ultrasound Schools Guide. Retrieved 20 January 2021.
- "Non-toxic, non-biocide-release antifouling coatings based on molecular structure design for marine applications". The Royal Society of Chemistry. 2015. Retrieved 20 January 2021.
- "A Copper Bottomed Guarantee". Dream Sails. 20 January 2021. Retrieved 21 January 2021.
- "Sound & Ultra-sound (Ultrasonics)". Dream Sails ~ Ultrasonic Antifouling ~ Everything You Need to Know. 20 January 2021. Retrieved 20 January 2021.
- "Ultrasonic Applications". Ultrasonic Antifouling ~ Everything You Need To Know. 20 January 2021. Retrieved 20 January 2021.
- "Ultrasonic Candle Blow Out". YouTube. 20 January 2021. Retrieved 20 January 2021.
- "SharperTek Ultrasonic Plastic Welder for Strap and Velcro Welding". YouTube. 20 January 2021. Retrieved 20 January 2021.
- "Acoustic Cavitation Explained - H2oBioSonic"
- Environmental Health Perspectives, Vol 64, pp. 233-252, 1985. "Free radical generation by ultrasound in aqueous and nonaqueous solutions. P. Riesz, D. Berdahl, and CL Christman
- Guo, S. F.; Lee, H. P.; Chaw, K. C.; Miklas, J.; Teo, S. L. M.; Dickinson, G. H.; Birch, W. R.; Khoo, B. C. (2011). "Effect of ultrasound on cyprids and juvenile barnacles". Biofouling. 27 (2): 185. doi:10.1080/08927014.2010.551535. PMID 21271409.
- "LG Sonic Tholen harbour"
- "Ultrasonic Marine Anti-fouling System". Ultrasonic Marine. Retrieved 20 January 2021.
- "Box Coolers, Seachests & Pipework"
- "Propeller shafts & propellers"
- "CleanAHull.com"
- "HullSonic.com.au – Ultrasonic Antifouling"
- "This is How You Sonic - Cruising World Magazine" (PDF). Ultrasonic Marine. 2016. Retrieved 21 January 2021.
- "H2oBioSonic HVAC Trial Results, Joshua David"
- "LG Sonic Tholen Harbour"
- "LG Sonic reservoir test"
- "Ultrasonic Antifouling LTD testimonials page"
- "CMS Marine magazine review"
- "CMS Magazine review"
- "Ultrasonic Antifouling Testimonials - CleanAHull.com"
- "Ultrasonic Antifouling Case Studies - Sonihull.com"
- "LSC Keeps Dutch Patrol Boats Clear - Sonihull.com"
- "Protecting Propeller Shafts & Propellers - Sonihull.com"