Aircraft maintenance
Aircraft maintenance is the performance of tasks required to ensure the continuing airworthiness of an aircraft or aircraft part, including overhaul, inspection, replacement, defect rectification, and the embodiment of modifications, compliance with airworthiness directives and repair.[1][2]
Regulation
The maintenance of aircraft is highly regulated, in order to ensure safe and correct functioning during flight. In civil aviation national regulations are coordinated under international standards, established by the International Civil Aviation Organization (ICAO). The ICAO standards have to be implemented by local airworthiness authorities to regulate the maintenance tasks, personnel and inspection system. Maintenance staff must be licensed for the tasks they carry out.
Aircraft maintenance organization
.jpg.webp)
Scheduled maintenance checks
Aircraft maintenance in civil aviation generally organized using a maintenance checks or blocks which are packages of maintenance tasks that have to be done on an aircraft after a certain amount of time or usage. Packages are constructed by dividing the maintenance tasks into convenient, bite-size chunks to minimize the time the aircraft is out of service, to keep the maintenance workload level, and to maximize the use of maintenance facilities. [3]
Power-by-the-Hour
A Power by the Hour program provides budget predictability, avoids installing a loaner during repairs when an aircraft part fails and enrolled aircraft may have a better value and liquidity. This concept of unscheduled maintenance was initially introduced for aircraft engines to mitigate engine failures.[4] The term was coined by Bristol Siddeley in 1962 to support Vipers of the British Aerospace 125 business jets for a fixed sum per flying hour.[5] A complete engine and accessory replacement service was provided, allowing the operator to accurately forecast this cost, and relieving him from purchasing stocks of engines and accessories.
In the 1980s, Rolls-Royce plc reinstated the program to provide the operator with a fixed engine maintenance cost over an extended period of time. Operators are assured of an accurate cost projection and avoid the breakdowns costs; the term is trademarked by Rolls-Royce but is the common name in the industry.[6] It is an option for operators of several Rolls-Royce aircraft engines. Other aircraft engine manufacturers such as General Electric and Pratt & Whitney offer similar programs.
Jet Support Services provides hourly cost maintenance programs independently of the manufacturers.[7] GEMCO also offers a similar program for piston engines in general aviation aircraft. Bombardier Aerospace offers its Smart Services program, covering parts and maintenance by the hour.
Maintenance release
At the completion of any maintenance task a person authorized by the national airworthiness authority signs a maintenance release stating that maintenance has been performed in accordance with the applicable airworthiness requirements. In the case of a certified aircraft this may be an Aircraft Maintenance Engineer or Aircraft Maintenance Technician, while for amateur-built aircraft this may be the owner or builder of the aircraft.[8] A maintenance release can be called a certificate of release to service (CRS).[9]
Maintenance personnel
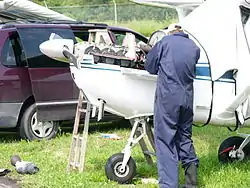
The ICAO defines the licensed role of aircraft maintenance (technician/engineer/mechanic), noting that "The terms in brackets are given as acceptable additions to the title of the license. Each Contracting State is expected to use in its own regulations the one it prefers."[10] Thus, aircraft maintenance technicians, engineers and mechanics all perform essentially the same role. However different countries use these terms in different ways to define their individual levels of qualification and responsibilities.
In Americas licenses for aircraft maintenance personnel include:
- Aircraft Maintenance Engineer (AME), also called Licensed Aircraft Maintenance Engineer (LAME or L-AME).
- Aircraft Maintenance Technician (AMT), or colloquially Airframe and Powerplant (A&P).
- Aircraft Maintenance Mechanic (AMM).
As there will be 41,030 new airliners by 2036, Boeing expects 648,000 new commercial airline maintenance technicians from 2017 till then: 256,000 in Asia Pacific (39%), 118,000 in North America (19%) and 111,000 in Europe (17%).[11]
In Europe aircraft maintenance personnel must comply with Part 66, Certifying Staff, issued by the European Aviation Safety Agency (EASA). This regulation establishes four levels of authorization:
- Level 1: General Familiarisation, Unlicensed
- Level 2: Ramp and Transit, Category A
- can only certify own work performed for tasks which he/she has received documented training
- Level 3: Line Certifying Staff and Base Maintenance Supporting Staff, Category B1 (electromechanic) and/or B2(Avionics)
- can certify all work performed on an aircraft/engine for which he/she is type rated excluding base maintenance (generally up to and including A-Check)
- Level 4: Base Maintenance Certifying Staff, Category C
- can certify all work performed on an aircraft/engine for which he/she is type rated, but only if it is base maintenance (additional level-3 staff necessary)
- this authorization does not automatically include any level 2 or level 3 license.
Market
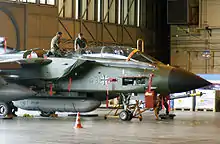
Aircraft
The Maintenance, Repair, Overhaul (MRO) Market was US$135.1 Billion in 2015, three quarters of the $180.3 B aircraft production market. Of this, 60% is for civil aviation : air transport 48%, business and general aviation 9%, rotorcraft 3% ; and military aviation is 40% : fixed wing 27% and rotary 13%. Of the $64.3 Billion air transport MRO market, 40% is for engines, 22% for components, 17% for line, 14% for airframe and 7% for modifications. Its is projected to grow at 4.1% per annum till 2025 to $96B.[12]
Airliner MRO should reach $74.3 Billion in 2017 : 51% ($37.9B) single-aisles, 21% ($15.6B) long range twin-aisles, 8% ($5.9B) medium range twin-aisles, 7% ($5.2B) large aircraft, 6% ($4.5B) regional jets as turboprop regional airliners and 1% ($0.7B) short range twin-aisles.[13] Over the 2017–2026 decade, the worldwide market should reach over $900 billion, led by 23% in North America, 22% in Western Europe, and 19% in Asia Pacific.[14]
In 2017, of the $70 billion spent by airlines on maintenance, repair and overhaul (MRO), 31% were for engines, 27% for components, 24% for line maintenance, 10% for modifications and 8% for the airframe; 70% were for mature airliners (Airbus A320 and A330, Boeing 777 and 737NG), 23% were for “sunset” aircraft (MD-80, Boeing 737 Classic, B747 or B757) and 7% was spent on modern models (Boeing 787, Embraer E-Jet, Airbus A350XWB and A380).[15]
In 2018, the commercial aviation industry expended $88 billion for MRO, while military aircraft required $79.6 billion, including field maintenance.[16] Airliner MRO is forecast to reach $115 billion by 2028, a 4% compound annual growth rate from $77.4 billion in 2018.[17] Major airframe manufacturers Airbus, Boeing and Embraer entered the market, increasing concerns about intellectual property sharing. Shared data-supported predictive maintenance can reduce operational disruptions. Among other factors, prognostics helped Delta Air Lines reduce maintenance cancellations by 98% from 5,600 in 2010 to 78 in 2017.[18]
Insourced maintenance can be inefficient for small airlines with a fleet below 50–60 aircraft. They have to either outsource it or sell its MRO services to other carriers for better resource utilization. For example, the maintenance on South African Comair's 26 Boeing 737s is outsourced to South African Airways' Technical Department. Another example is Spain's Air Nostrum operates 45 CRJs and ATR72s and its 300-person maintenance department provides line, base maintenance and limited component repair for other airlines 20% of the time.[19]
Airframe heavy maintenance is worth $6 billion in 2019: $2.9 billion for C checks and $3.1 billion for D checks, Aviation Week forecasts a growth to $7.5 billion in 2028 – $3.1 billion C and $4.2 billion D – for $70 billion over 10 years, 10% of the overall market compared to 40% for the engines.[20]
Engines

The commercial aviation engine MRO market is anticipated by Aviation Week to be $25.9 billion in 2018, a 2.5 billion increase from 2017, led by 21% for the Boeing 737NG' CFM56-7B and the A320's CFM56-5B and IAE V2500 (also on the MD-90) tied for second, followed by the mature widebody engines: the GE90 then the Trent 700.[21]
Over the 2017–2026 decade, the largest markets for turbofans will be the B737NG's CFM56-7 with 23%, the V2500-A5 with 21%, the GE90-115B with 13%, the A320's CFM56-5B with 13%, the PW1000G with 7%, the Trent 700 with 6%, the CF6-80C2 with 5%, the CFM LEAP with 5% and the CF34-8 with 4%.[14] Between 2018 and 2022, the largest MRO demand will be for CFM engines with 36%, followed by GE with 24%, Rolls with 13%, IAE with 12% and Pratt with 7%.[22]
As an aircraft gets older, a greater percentage of its value is represented by its engines. Over the course of the engine life it is possible to put value back in by repair and overhaul, to sell it for its remaining useful time, or to disassemble it and sell the used parts, to extract its remaining value. Its maintenance value includes the value of life-limited parts (LLPs) and the time before overhaul. The core value is the value of its data plate and non-life-limited-parts.[23] Engine makers deeply discount their sales, up to 90%, to win the multi-year stream of spares and services, resembling the razor and blades model.[24]
Engines installed on a new aircraft are discounted by at least 40% while spare engine values closely follow list prices. Accounting for 80% of a shop visit cost, LLP prices escalate to recoup the original discount, until engine availability increase with aircraft teardowns. Between 2001 and 2018 for the Airbus A320 or the Boeing 737-800, their CFM56 value increased from 27–29% to 48–52% of the aircraft value. The 777-200ER's PW4000 and the A330-300's Trent 700 engines rose from a share of 18–25% in 2001 to 29–40% in 2013. For the A320neo and 737 MAX, between 52% and 57% of their value lies in their engines: this could rise to 80–90% after ten years, while new A350 or B787 engines are worth 36–40% of the aircraft. After some time the maintenance reserves exceed the aircraft lease.[25]
In 2018, a full set of LLP for a B737-800's CFM56-7B list price is $3.6 million, like for the A320ceo's CFM56-5B for 20–30,000 cycles up from $2.0 million in 2009, while an IAE V2500 is priced at $3.9 million for 20,000 cycles but have a lower overhaul cost. The LLP parts for and A320neo's PW1127G costs $4 million and its competitor $4.3 million for 20–30,000 cycles. For an A330ceo, a GE CF6-80 LLP set is priced at $11 million for 15–20,000 cycles and $9 million for a PW4000, and $6 million for a Trent 700 but with a $9–10 million overhaul against $4–5 million for the others. The LLP set for a B767-300ER's CF6 or PW4000 costs $7 million, and for a B787-8's Trent 1000 $7 million compared to $8.5 million for a GEnx. An B777-300ER's GE90 LLP set is priced at $9 million while the A380's Trent 900 costs $7 million, both for 15,000 cycles. [26]
Between 2019 and 2038, 5,200 spare airliner engines will be required with at least half leased.[27]
An engine overhaul for a B737-800 costs $3.1 million every 20,000 hours, or $3.4 million every 15,000 hours for earlier variants, while for a B757 powerplant it costs $4.5 million every 24,000 hours. For an A330 turbofan, it costs $7 million every 24,000 hours, $8 million for an A350 or B787 engine, $9 million every 20,000 hours for a B777-200ER powerplant and $10 million every 25,000 hours for a B777-300ER engine. It costs $4 million every 18,000 hours for each B747-400 turbofan and $7.5 million every 25,000 hours for an A380 engine.[28]
Future of aircraft maintenance
Aircraft health monitoring
Airbus has indicated that data diagnostics could put an end to aircraft unscheduled grounding for fault repairs around 2025, supported by big data and operational experience. Predictive maintenance, diagnostics and health monitoring could eliminate unscheduled groundings, by making maintenance schedule intervals more frequent to avoid AOGs and the associated operational interruptions, ultimately eliminating them. Data or monitoring can tell that some parts do not need a scheduled check, but a full transition to this model will need much greater experience. With more history, examples and regulatory confidence, the maintenance program and associated manuals could become a dynamic documents for each specific aircraft with maintenance schedule based on operational history of the aircraft.[29]
Electric aircraft
In October 2018, consultant Roland Berger counted 134 electric propulsion projects: 70% electric engines with batteries recharged on ground and 30% hybrid-electric with a fuel generator, in parallel or in series; 45% are urban air taxis, 43% general aviation and 12% airliners. All-electric is sometimes selected for sub-19 seats commuters, and more often for smaller 2-4-seat aircraft like urban air taxis or trainers. Electric motors will probably require less maintenance than a fuel engine, while batteries and cables may need to be exchanged more often than fuel systems.[30]
The all-electric Pipistrel Alpha Electro two-seat trainer is already certified as a LSA in Europe, Australia and possibly the US. Redmond, Washington-based MagniX is integrating a 350 hp (260 kW) electric motor on its iron bird testbed before a first flight of a Cessna Caravan in 2019, with a 750 hp (560 kW) Magni500 replacing its PT6 single turboprop. MagniX expects to certify the Magni500 and the 375 hp (280 kW) Magni250 by 2020, and the Caravan conversion by 2022 with a range of 100–200 mi (160–320 km) as it is typically operated over less than 100 mi (160 km). A Britten-Norman Islander retrofitted with electric propulsion should be demonstrated by 2021 by Cranfield Aerospace before commercial service in 2023. Roland Berger expects a 50-seat hybrid-electric airliner in 2032 with a 340 km (210 mi) range.[30]
Maintenance automation
Automated aircraft inspection systems have the potential to make aircraft maintenance safer and more reliable.[31] Various solutions are currently developed: a collaborative mobile robot named Air-Cobot,[32][33] and Unmanned aerial vehicles from Donecle or Easyjet.[34][35]
See also
References
- Transport Canada (May 2012). "Canadian Aviation Regulations 2008-1, Part I - General Provisions, Subpart 1 - Interpretation". Archived from the original on 27 December 2012. Retrieved 9 December 2012.
- Transport Canada (March 2002). "Canadian Aviation Regulations 2008-1, Part V - Airworthiness, Standard 593 - Airworthiness Directives". Archived from the original on 18 May 2013. Retrieved 9 December 2012.
- Hessburg, Jack. "What's This 'A' Check, 'C' Check Stuff?". www.aviationpros.com. Retrieved 2020-12-23.
- William Garvey (Nov 3, 2017). "How Hourly Maintenance Provides Shelter From Explosive Surprises". Aviation Week & Space Technology.
- "Rolls-Royce celebrates 50th anniversary of Power-by-the-Hour" (Press release). Rolls-Royce. 30 October 2012.
- "'Power by the Hour': Can Paying Only for Performance Redefine How Products Are Sold and Serviced?". Knowledge at Wharton. Feb 21, 2007.
- "Jet Support Services, Inc". Bloomberg Businessweek.
- "Canadian Aviation Regulations (CARs)Part V - Standard 571 - Maintenance". Transport Canada. 2010-12-01. 571.10 Maintenance Release.
- Airworthiness Manual, Doc 9760 (3 ed.). Montreal (Canada): International Civil Aviation Organization. 2014. p. 375. ISBN 978-92-9249-454-4. Archived from the original on 2018-09-01. Retrieved 2018-09-01.
- ICAO; Doc 7300, Convention on International Civil Aviation (also referred to as the Chicago Convention), 9th Edn. (2006), Annex 1, Chapter 4. Licenses and ratings for personnel other than flight crew members.
- "Pilot and Technician Outlook". Boeing. 2017.
- Kevin Michaels (April 28, 2016). "MRO Industry Outlook" (PDF). ICF International.
- "2017 MRO Market Share by Category". Aviation Week Network. Jul 12, 2017.
- "Top 10 Engine MRO Demand: 2017–26". Aviation Week Network. Aug 16, 2017.
- Kevin Michaels (Jan 16, 2018). "Opinion: OEMs Focus On Mature Aircraft For Aftermarket Growth". Aviation Week & Space Technology.
- Lee Ann Shay (Jan 2, 2018). "Commercial Spending Will Lead MRO Field In 2018". Aviation Week & Space Technology. Comparing civil, helicopter, business aviation and military MRO forecasts for 2018.
- Aaron Chong (26 Jan 2018). "Global MRO spend to reach $115 billion by 2028 - Wyman". Flightglobal.
- Jon Hemmerdinger (25 Apr 2018). "Airframers set out on differing aftermarket paths". Flightglobal.
- Henry Canaday (Mar 12, 2018). "Outsourcing Versus In-Sourcing For Small Fleets". Aviation Week Network - MRO.
- Alex Derber (Dec 18, 2018). "2019 Outlook For Airframe Heavy Maintenance". Aviation Week & Space Technology.
- James Pozzi (Nov 24, 2017). "Life In The Old Dogs Yet". Aviation Week Network.
- "Engine MRO Demand - Top 5 Engine OEM: 2018–22". MRO Network. Aviation Week Network. May 30, 2018.
- Alex Derber (Oct 16, 2017). "Keeping An Eye On Engine Values". Aviation Week network.
- Ernest S. Arvai (January 19, 2018). "The Meaningless Game of List Prices". AirInsight.
- David Griffin (21 June 2018). "Analysis: The influence of engines on aircraft values". FlightGlobal.
- Aircraft Value News (December 10, 2018). "Engine Life Limited Parts Remain Major Cost Item for Operators".
- Alex Derber (Oct 22, 2018). "Engine Leasing In Rude Health". Aviation Week Intelligence Network.
- Aircraft Value News (March 18, 2019). "Engine Overhaul Costs Mitigated by Longer On Wing Time".
- Max Kingsley-Jones (12 Dec 2017). "Airbus sees big data delivering 'zero-AOG' goal within 10 years". Flightglobal.
- Paul Seidenman; David J.Spanovich (Jan 10, 2019). "Why Electric Propulsion Could Be Disruptive For MRO Electric propulsion for commercial aircraft, once viable, could force massive changes on MRO providers". Aviation Week Network.
- "Robots in the hangar". November 23, 2015. Retrieved May 20, 2016.
- Jovancevic, Igor; Larnier, Stanislas; Orteu, Jean-José; Sentenac, Thierry (November 2015). "Automated exterior inspection of an aircraft with a pan-tilt-zoom camera mounted on a mobile robot" (PDF). Journal of Electronic Imaging. 24 (6): 061110. Bibcode:2015JEI....24f1110J. doi:10.1117/1.JEI.24.6.061110.
- I. Jovancevic, I. Viana, T. Sentenac, J.J. Orteu and S. Larnier, Matching CAD model and images features for robot navigation and inspection of an aircraft, International Conference on Pattern Recognition Applications and Methods, pp. 359–366, February 2016.
- "Donecle - lightning fast aircraft inspections". Retrieved May 20, 2016.
- "EasyJet's Using Drones to Check Planes for Lightning Damage". Retrieved May 20, 2016.
External links
- "Association for Women in Aviation Maintenance".
- Lindsay Bjerregaard, Lee Ann Shay (Oct 11, 2017). "A Day In American's Line Operations At Chicago O'Hare". Aviation Week network.
- James Pozzi (Oct 17, 2017). "Inside Iberia's Engine Shop". Aviation Week network.
- James Pozzi (Nov 4, 2017). "A Look Around Lufthansa Technik Sofia's Expanded Facility". Aviation Week network.
- Lindsay Bjerregaard (Nov 13, 2017). "On The Ground At JetBlue's JFK Hangar". Aviation Week network.
- GE Aviation. Maintenance Minute.
Maintenance Minute videos are produced by GE Aviation's training team to help the aircraft maintainer with everyday engine maintenance tasks.