Annular cutter
An annular cutter (also called as core drill, core cutter, broach cutter, trepanning drill, hole saw, or cup-type cutter) is form of core drill used to create holes in metal. An annular cutter cuts only a groove at the periphery of the hole and leaves a solid core or slug at the center.[1]
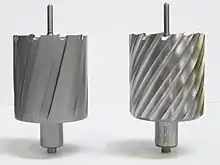
An annular cutter is a more expensive and more efficient alternative to spiral drill bits and standard hole saws. An annular cutter is similar to a hole saw but differs in geometry and material. The two most common types are high-speed steel (HSS) and tungsten carbide tipped (TCT).
Like a hole saw, but unlike a spiral drill bit, an annular cutter cuts only the periphery of a hole, leaving a circular "slug" at the center.
Annular cutters are available from 12 mm (1/2’’) diameter to 200 mm (7 7/8’’) and larger. Depths of 30 mm, 55 mm, 75 and 110 mm are commonly available.
Annular cutters are best used with a drill press or magnetic drilling machine, both for their stability against high torque forces created by such a drill bit and lower RPMs compared to other types of drills.
History
The annular cutter was patented in 1973.[2] The high-speed steel type was patented 1983,[3] and tungsten carbide tipped in 1985.[4]
Benefits
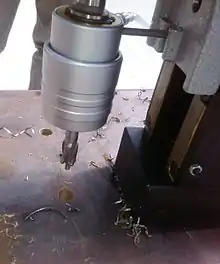
Time saving
As an annular cutter cuts only on the periphery of the hole to be made, it has to remove much less material as compared to conventional drill bits which cut and remove the complete material of the hole. Annular cutters are considered to be 3 to 4 times faster than conventional drill bits. Also while using a twist drill bit or metal hole saw one has to do pre-drilling and step-drilling operations for bigger diameter holes, whereas an annular cutter requires no pre-drilling and step-drilling. It is a one-shot drilling operation.
The annular cutters have fewer teeth and less wear, therefore with an annular cutter holes can be made at higher or faster cutting speed and a faster feed rate of the drilling machine.[5]
Energy savings
Because annular cutters do not have to drill/cut through the complete work piece, they require less thrust and thus less energy to drill through material.[6]
More finishing
The hole made using an annular cutter is more finished, precise and accurate.[6]
Easy
Due to the unique geometry of the annular cutters, making holes at awkward angles is also very easy.[6]
Efficient cooling
The cooling of annular cutters is internal. The internal lubrication is provided through a hole with the help of a pilot pin. Internal lubrication makes the annular cutter faster and more efficient for deep hole drilling.[6]
Best for light duty machines
As the annular cutters require very low RPM (from min 50 RPM), these cutters can be easily used with light duty drilling machines or portable magnetic base drilling machines.[6]
Sizes
Annular cutters biggest advantage is the variety of sizes. Annular cutters start from 12 mm diameter up to 150 mm diameter and more if required. Various cutting depth (length) of annular cutters can be sourced depending upon the requirement.[6]
Types
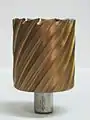
The types of core drills are categorized by the material used to manufacture them:[7] Primarily a metal core drill is made from High Speed Steel and Tungsten Carbide Tips. So commercially the types of core drills are HSS core drills and TCT core drills.[8]
High-speed steel (HSS)
HSS core drills are made from high-speed steel material. These are most popular core drills or annular cutters in market. HSS core drills are cheaper for smaller diameter i.e. 40 mm. The biggest advantage of HSS core drill is its ability to re-sharpen. Unlike TCT core drills, HSS core drills re-sharpened and used with good efficiency until the desirable length is remaining. HSS core drills have longer service life, high heat resistance: the characteristics of HSS core drills is that drilling with these core drills can be done without the use of excessive force.
Standard
The HSS Standard core drills are made from M2 steel. These core drills are one of the most popular core drills in western countries due to its cost and resharpening advantage. The Standard HSS core drills are used to drill Mild and Structural steel, Aluminium, Stainless steel of lower BHN., etc.
Cobalt
The HSS Cobalt are core drills made from M42 Steel. These core drills have 8% Cobalt in HSS. These core drills are harder than the Standard HSS core drills which gives better performance to drill harder material. A high percentage of Cobalt in HSS makes it faster, stronger and durable.[9] Cobalt HSS core drills are used to drill materials like Structural Steel, Stainless Steel, Cast iron, etc.
Hard coating
The HSS core drills with Hard Coating are core drills with a coating on it, generally TiN Coating. This make the core drills more resistant to heat, longer tool life and even removal of chips. These core drills are gaining lot of popularity over the Standard HSS core drills these days. These core drills are used Structural steel, Stainless steel, etc.[7]
Tungsten carbide tipped (TCT)
Tungsten carbide tipped (TCT) core drills have tungsten carbide on their tips, a very hard material suitable for cutting through tougher materials. TCT core drills are more expensive than HSS core drills but are faster and more efficient making larger holes. TCT core drills are cheaper for bigger diameter i.e. above 41 mm. Tip breakage is more likely than with HSS core bits, and TCT bits may not be resharpened.
Standard
A Standard TCT core drill has tungsten carbide tips. These types of core drills are now available in vast range of diameter, for up to 150 mm. These are popularly used core drills on magnetic core drilling machines. These core drills are popularly used to drill materials like railway tracks, structural steel, stainless steel, cast iron, etc.
Hard coating
The TCT core drills with Hard Coating are core drills with a coating on it, generally TiN Coating. This make the core drills more resistant to heat, longer tool life and even removal of chips just like the advantage of HSS core drill. The biggest advantage of hard coated core drills is that these cutters are very good for cutting larger diameters on hard material. These core drills are popularly used to drill materials like corroded or weathered material, structural and stainless steel.
Shanks
Weldon
"Weldon shank" annular cutters have 2 flats and this is the traditional method adopted by many of the popular magnetic drill manufacturers. "Weldon shank" annular cutters fix in the chuck by tightening grub screws in the two flat areas.
Universal
"Universal shank" annular cutters has one flat and three quick connect grooves. This is also a popular method for using annular cutters into mag drills quickly, without any strain of tightening grub screws. mostly "universal shank cutters" can be used in "weldon -shank machines, where as weldon-shank annular cutters can't use in "one-touch" machines without the help of an extra adapter. while using "universal shank cutters" into "weldon shank" machines, the tightening area (flat area) is only one, which is also not 100% sufficient to tighten the both screws.
Drilling tubes and pipes
Annular cutters can also be best used to make holes in pipes and tubes. Annular cutters help make holes in pipe and tubes without dimpling and deburring. Unlike the conventional method of bringing the workpiece to machine, with the help of portable magnetic core drilling machines, you can now bring the machine to the workpiece. This makes the drilling process on tubes very easy.
To make a hole in tube or pipe easily an annular cutter should be used with a magnetic base drilling machine and a tube/pipe clamping device. The tube clamping device is a metallic device which is clamped on the tube with an adjustable chain. After clamping the device the magnetic drilling machine is placed on the device, which gets clamped to the device by switching on its magnet.
With the help of magnetic drilling machines' proper RPM the annular cutter makes a perfect hole in the tube.
Generally a HSS annular cutter is used to make holes in tubes and pipes, as the TCT annular cutters has more chances of cutting teeth breakage due to curved surfaces of tubes and pipes.
As annular cutters are hollow there is no dead zone resistance. The cutting takes place only on the periphery of the hole to be made. Annular cutters distribute load equally on the periphery of the hole with its multiple cutting edges, thus the required thrust and energy is also much less comparatively.[10]
Comparison between HSS and TCT core drills
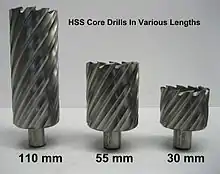
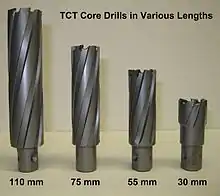
Cost
HSS core drills are cheaper than the TCT core drills for smaller diameters up to 40 mm, while TCT core drills are cheaper than HSS for diameters above 41 mm.
Re-sharpening
Once the HSS cutter loses its sharpness, it can be re-ground on a grinding machine and can be used again. While, re-grinding the TCT core drill is possible but very difficult and time consuming.
Defect
The chances of defect in TCT core drills is more because the tungsten carbide tips are glued on the core drill and when the core drill falls down or crashes on the material, the chances tip breakage is more. HSS cutter on the other hand are completely made out of one material.
Speed
TCT cutter biggest advantage is speed and ease in which it may cut harder materials. Especially for larger diameter TCT core drills are very successful. While HSS core drills are good when drilling not very hard material and for small diameter hole sizes.
Hardness
The teeth on TCT core drills are harder than HSS, allowing them to cut more difficult materials.
Advantages of annular cutters over conventional twist drill bits
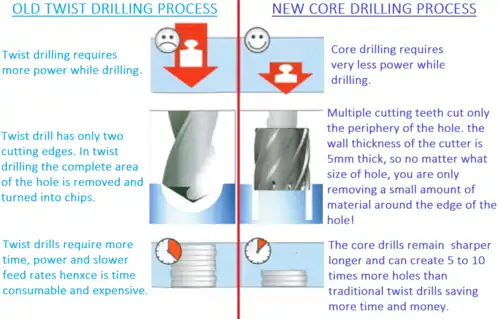
Annular cutters have several advantages over conventional twist drill bits:[11]
Less power / Less effort
The conventional twist drill has only two cutting edges, while an annular cutter or core drill has multiple cutting edges which helps to drill with much less horsepower and efforts.[12]
Less material to cut
The conventional twist drill being solid and having only cutting point has to cut or remove the complete material of the hole to be made. While with annular cutters or core drills having multiple edges and being hollow cuts only on the periphery of the hole to be made.[5]
Less time needed
As core drill has to cut less material as compared to twist drill, the time required is also too less. A core drill is considered to be 3 to 4 times faster than twist drills.
Lower cost
A single core drill makes 5 to 10 times more holes then a twist drill, plus core drills can be again reground to make another 1500 holes, thus saving a lot of tool cost.
No pre-drilling or step-drilling
Unlike twist drills, core drills even for larger diameters do not require any pre-drilling or step-drilling.
Example: To make a 50 mm diameter hole with twist drill, one has to start making a pre-drilling of 10 mm, than 15 mm than 20 mm, ...up to 50 mm slowly increasing the size of holes. While with core drill one can drill directly 50 mm in one-shot.[12][5]
Disadvantages of core drills
The biggest disadvantage of core drill or annular cutter is that it can not drill blind holes. A core drill due to its hollow geometry can only make through holes. Another disadvantage is in drilling a pile of many plates. There are some core drills with a different geometry which can be used for drilling piles of plates, but still it is not 100% successful. The cost of a core drill is high compared to twist drill, but the cost per hole made with core drill is less as compared to twist drills, this is because a single core drill makes 5 to 10 times more holes than a twist drill.[12][11]
Cooling lubricants
Using lubricant or coolant with any type of annular cutter is a must. A correct lubrication and coolant delivery more life for annular cutters. The very important thing to know is that TCT annular cutters require Coolant, not lubricant and HSS annular cutters required Cutting oil, not coolant.
While drilling overhead with liquid lubricants will lead to damage the motor of the machine due to the lubricant entering the motor. Thus high performance cutting paste to drill overhead or in the horizontal situation. This cutting paste is suitable for both HSS and TCT core drills as well as for thread cutting tools/Taps.
Ejector pin
The ejector pin (also called a pilot pin) has three major functions:[14]
- Centering - The ejector pin is exactly positioned to the center punch mark. Switch the magnet on and the machine and annular cutter are in the drilling position.
- Oiling - Cutting oil for automatic internal lubrication is supplied via the ejector pin.
- Ejecting - The spring-loaded ejector pin pushes the core out of the drill hole made by annular cutter.
Cutting speed
The magnetic drilling machines are provided with speed gears and some machines are also equipped with variable speed control. As per the diameter of the annular cutter and the type of annular cutter the speed of the magnetic drilling machine has to be set.[15]
The formula for calculating the speed is:
d = diameter of the annular cutter in mm.
v = cutting speed of the annular cutters.
HSS vs TCT annular cutters
Trade-offs between HSS and TCT annular cutters include:[16]
- Cost - HSS annular cutters are cheaper than the TCT for smaller diameters up to 40 mm, while TCT are cheaper for diameters above 41 mm.
- Re-sharpening - A HSS annular cutter can be resharpened, while re-grinding a TCT is possible but more difficult due to the geometry needed for carbide. Unless carbide is ground properly it can break easily.
- Breakage - HSS cutters are made of one piece of steel, while TCT cutters have brazed on teeth, which can break or shatter more easily.
- Speed - TCT cutters are faster, especially for larger diameter holes
- Hardness - TCT cutters can drill through harder materials due to the carbide tips.
References
- Metal Cutting Theory and Practice. David A. Stephenson, John S. AgapiouCRC Press, 02.12.2005. Page number 216.
- Hougan, Dough. Inventing, As a Way of Life.
- United States Patent. Patent number 4516890. Filed 12.09.1983. USA.
- United Kingdom Patent. Patent number 2167983-A. Filed 31.10.1985. UK.
- "Benefits of Using an Annular Cutter". 2010-12-15. Archived from the original on 2014-05-27. Retrieved 2014-05-27.
- "How to select annular cutter?". Magnetic Drilling Machines .com. 2015-12-11. Retrieved 2017-03-21.
- "Selecting Annular Cutters". UAE Magnetic Drilling Machine. UAE Magnetic Drilling Machine. Archived from the original on 2018-11-07.
- "Advantages of HSS Cobalt Annular Cutters". UAE Magnetic Drilling Machine. UAE Magnetic Drilling Machine.
- "Tube drilling with magnetic base drilling machines". Magnetic Drilling Machines .com. 2015-11-03. Retrieved 2017-03-21.
- says, MUKESH SHAH (2015-10-27). "Twist Drilling vs. Annular Cutting". Magnetic Drilling Machines .com. Retrieved 2017-03-21.
- "What are core drills or annular cutters?". www.metaller-machines.com. Metaller Machines. Archived from the original on 2014-05-27. Retrieved 2014-05-26.
- Carroll, Tom. "Twist Drilling vs. Annular Cutting – A Primer". csunitec.com. CS Unitec. Retrieved 2014-05-26.
- "What is the advantage of an ejector pin of the annular cutter?". magneticdrillingmachines.com.
- "How to calculate the speed for an annular cutter?". Magnetic Drilling Machines .com. 2016-07-14. Retrieved 2017-03-21.
- NITTO KOHKI. "TCT vs. HSS". www.nitto-kohki.eu.