Pliofilm
Pliofilm was a brand name of a plastic wrap made by the Goodyear Tire and Rubber Company at plants in the US state of Ohio. Invented in the early 1930s, it was made by dissolving rubber in a benzene solvent and treating it with gaseous hydrochloric acid. Pliofilm was more stable in a range of humidities than earlier cellulose-based wraps and became popular as a food wrap. Its manufacture exposed workers to carcinogenic benzene and, when an additive was used to improve durability, caused dermatitis.
.jpg.webp)
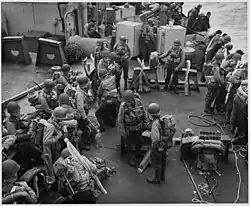
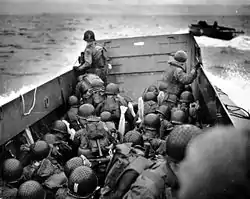
The supply of rubber was restricted during World War II due to the Japanese occupation of much of South-East Asia which hindered production, and so during the war years production was given over entirely to military purposes, with Pliofilm being used to wrap machinery and to waterproof firearms. After the war a plant was opened in Wolverhampton, England, and commercial production continued until the late 1980s.
Manufacture
Pliofilm is a transparent film made of rubber hydrochloride.[1] It is impermeable to water and water vapour and non-flammable.[1][2]
Pliofilm was manufactured by dissolving natural rubber in the solvent benzene.[3] The solution was kept in a tank at around 10 °C (50 °F) and treated with gaseous hydrochloric acid.[3][4] The material was then neutralised with an alkali.[3] The product was cast as a sheet on an endless belt which passed through a dryer that drove off the solvent.[5][6] The finished product was around 30% chlorine.[4] It could be made thinner by stretching whilst being heated and thickesses of 0.00075–0.025 inches (0.019–0.635 mm) were sold.[7][8] Thicker sheets could be produced by laminating the product, combining several sheets with the use of rubber cement.[9]
History and uses
Pliofilm was invented by Harold J. Osterhof at the Goodyear Tire and Rubber Company in the early 1930s and was first marketed in 1934.[10][11][12] The product found early use as a food wrap, its very low oxygen permeability helping to keep foods fresh.[8][13][14] Its clinginess and better stability at a range of humidities was an advantage over the cellulose wrapping films used previously, Pliofilm became about as popular as Cellophane by 1937 and had supplanted cellulose films by 1942.[13][14][15] Pliofilm could also function as a shrink wrap and was marketed as a means to reseal bottles (it was advised to place the Pliofilm over an embroidery hoop and to heat it while twisting the bottle).[8][16]
The material was also used to manufacture aprons and protective sleeves to protect factory workers from hazardous substances.[3] Pliofilm saw widespread use during World War II as a means of protecting tools and engines during shipping.[11] For aviation parts a modified product was produced; a chemical known as RMF was added in quantities of 1-5% to make the product less susceptible to deterioration by ultra-violet light.[3][9] RMF led to dermatitis in workers who had contact with it. The United States Public Health Service investigated the factories involved and recommended that workers wear protective sleeves made from ordinary Pliofilm.[3] The manufacturing process also caused workers to become exposed to benzene. A study of Pliofilm workers at Goodyear's Akron and St. Marys, Ohio plants between 1936 and 1976 was used as the basis for determining the cancer slope factor and occupational exposure standards for benzene.[17]
Pliofilm was used by the US military during World War II. Sleeves were producted as a means of waterproofing firearms during amphibious landings. These came in three sizes to suit pistols, rifles and sub-machine guns and were sealed by tying a knot in the sleeve or by use of an elastic band.[18] It was intended that the sleeve would be torn off after landing, though some troops kept them on inland due to fields having been flooded by the Germans as a defensive measure. The Pliofilm usually trapped enough air to keep the firearm buoyant if dropped in the water. Because it prevented use of the weapon's regular sling some troops fashioned ad-hoc slings from rope that could be used over the top of the Pliofilm.[18][19][20]
Pliofilm manufacture was hindered by the Japanese occupation of rubber-producing countries in South-East Asia.[21] Commercial outputs were stopped and the entire production given over to military uses, leading to a large commercial demand and a backlog of orders after the war's end.[22][23] In the post-war years Pliofilm saw use as a food wrap; to package drugs and textiles; and as a means of laminating paper.[11][24] It was also marketed as Vitafilm.[24] Production was extended abroad to the Goodyear factory in Wolverhampton, England, in the late 1940s.[25] The US Mint switched its packaging for mint set coins from Cellophane to Pliofilm in 1955.[26] Osterhof was awarded the 1971 Charles Goodyear Medal by the American Chemical Society for his invention of Pliofilm.[10] It remained commercially available in 1987.[4]
References
- Chemical & Process Engineering. L. Hill Technical Group. 1945. p. 206.
- "Rubber hydrochloride". Encyclopedic Dictionary of Polymers. Springer: 852–852. 2007. doi:10.1007/978-0-387-30160-0_10001.
- Public Health Reports. U.S. Marine Hospital Service. April 1943. p. 625.
- Štěpek, Jiri (1987). Polymers as Materials for Packaging. E. Horwood Limited. p. 242. ISBN 978-0-85312-677-5.
- Packaging Series. American Management Association. 1955. p. 73.
- Stern, Harold Jacob (1967). Rubber: Natural and Synthetic. Maclaren. p. 58.
- Modern Plastics Worldwide World Encyclopedia, with Buyer's Guide. Plastics Catalogue Corporation. 1953. p. 182.
- Popular Mechanics. Hearst Magazines. October 1949. p. 174.
- Public Health Reports. U.S. Marine Hospital Service. April 1943. p. 626.
- The Michigan Alumnus. Alumni Association of the University of Michigan. September 1970. p. 32.
- The Michigan Technic. University of Michigan, College of Engineering. February 1958. p. 1.
- Chemical & Process Engineering. L. Hill Technical Group. 1952. p. 32.
- Illini Horticulture. Illinois State Horticultural Society. 1937.
- Modern Packaging Encyclopedia. McGraw-Hill. 1971. p. 135.
- Plastics in Industry. Chapman & Hall Limited. 1942. pp. 204–5.
- Decisions of Commissioner of Patents and U.S. Courts in Patent and Trademark and Copyright Cases. U.S. Government Printing Office. 1945. p. 207.
- Williams, Pamela R. D.; Paustenbach, Dennis J. (25 April 2003). "Reconstruction of benzene exposure for the Pliofilm cohort (1936-1976) using Monte Carlo techniques". Journal of Toxicology and Environmental Health. Part A. 66 (8): 677–781. doi:10.1080/15287390306379. ISSN 1528-7394.
- Hambucken, Denis (2013). American Soldier of WWII: D-Day, A Visual Reference. The Countryman Press. p. 39. ISBN 978-1-58157-200-1.
- Marriott, Leo; Forty, Simon (2014). The Normandy Battlefields: D-Day and the Bridgehead. Casemate Publishers. p. 94. ISBN 978-1-61200-338-2.
- Morgan, Martin (2014). The Americans on D-Day: A Photographic History of the Normandy Invasion. Zenith Press. p. 141. ISBN 978-1-62788-154-8.
- Modern Packaging. Morgan-Grampian Publishing Company. 1945. p. 116.
- Food Manufacture. Morgan-Grampian. 1945. p. 191.
- Modern Packaging. Morgan-Grampian Publishing Company. 1945. p. 117.
- Stern, Harold Jacob (1967). Rubber: Natural and Synthetic. Maclaren. p. 59.
- Food Manufacture. 1949. p. 169.
- Herbert, Alan (1995). Coin Clinic - 1,001 Frequently Asked Questions. Krause Publications. p. 163. ISBN 978-0-87341-380-0.