Ultrasonic transducer
Ultrasonic transducers and ultrasonic sensors are devices that generate or sense ultrasound energy. They can be divided into three broad categories: transmitters, receivers and transceivers. Transmitters convert electrical signals into ultrasound, receivers convert ultrasound into electrical signals, and transceivers can both transmit and receive ultrasound.
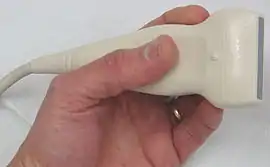
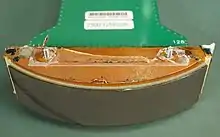
In a similar way to radar and sonar, ultrasonic transducers are used in systems which evaluate targets by interpreting the reflected signals. For example, by measuring the time between sending a signal and receiving an echo the distance of an object can be calculated. Passive ultrasonic sensors are basically microphones that detect ultrasonic noise that is present under certain conditions.
The design of transducer can vary greatly depending on its use: those used for medical diagnostic purposes, for example the range-finding applications listed above, are generally lower power than those used for the purpose of changing the properties of the liquid medium, or targets immersed in the liquid medium, through chemical, biological or physical (e.g. erosive) effects. The latter class include ultrasonic probes and ultrasonic baths, which apply ultrasonic energy to agitate particles, clean, erode, or disrupt biological cells, in a wide range of materials; See Sonication.
Applications and performance
Ultrasound can be used for measuring wind speed and direction (anemometer), tank or channel fluid level, and speed through air or water. For measuring speed or direction, a device uses multiple detectors and calculates the speed from the relative distances to particulates in the air or water. To measure tank or channel liquid level, and also sea level (tide gauge), the sensor measures the distance (ranging) to the surface of the fluid. Further applications include: humidifiers, sonar, medical ultrasonography, burglar alarms, non-destructive testing and wireless charging.
Systems typically use a transducer which generates sound waves in the ultrasonic range, above 18 kHz, by turning electrical energy into sound, then upon receiving the echo turn the sound waves into electrical energy which can be measured and displayed.
This technology, as well, can detect approaching objects and track their positions.[1]
Ultrasound can also be used to make point-to-point distance measurements by transmitting and receiving discrete bursts of ultrasound between transducers. This technique is known as Sonomicrometry where the transit-time of the ultrasound signal is measured electronically (ie digitally) and converted mathematically to the distance between transducers assuming the speed of sound of the medium between the transducers is known. This method can be very precise in terms of temporal and spatial resolution because the time-of-flight measurement can be derived from tracking the same incident (received) waveform either by reference level or zero crossing. This enables the measurement resolution to far exceed the wavelength of the sound frequency generated by the transducers.
Transducers
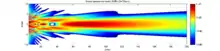
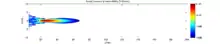
Ultrasonic transducers convert AC into ultrasound, as well as the reverse. Ultrasonics, typically refers to piezoelectric transducers or capacitive transducers. Piezoelectric crystals change size and shape when a voltage is applied; AC voltage makes them oscillate at the same frequency and produce ultrasonic sound. Capacitive transducers use electrostatic fields between a conductive diaphragm and a backing plate.
The beam pattern of a transducer can be determined by the active transducer area and shape, the ultrasound wavelength, and the sound velocity of the propagation medium. The diagrams show the sound fields of an unfocused and a focusing ultrasonic transducer in water, plainly at differing energy levels.
Since piezoelectric materials generate a voltage when force is applied to them, they can also work as ultrasonic detectors. Some systems use separate transmitters and receivers, while others combine both functions into a single piezoelectric transceiver.
Ultrasound transmitters can also use non-piezoelectric principles. such as magnetostriction. Materials with this property change size slightly when exposed to a magnetic field, and make practical transducers.
A capacitor ("condenser") microphone has a thin diaphragm that responds to ultrasound waves. Changes in the electric field between the diaphragm and a closely spaced backing plate convert sound signals to electric currents, which can be amplified.
The diaphragm (or membrane) principle is also used in the relatively new micro-machined ultrasonic transducers (MUTs). These devices are fabricated using silicon micro-machining technology (MEMS technology), which is particularly useful for the fabrication of transducer arrays. The vibration of the diaphragm may be measured or induced electronically using the capacitance between the diaphragm and a closely spaced backing plate (CMUT), or by adding a thin layer of piezo-electric material on diaphragm (PMUT). Alternatively, recent research showed that the vibration of the diaphragm may be measured by a tiny optical ring resonator integrated inside the diaphragm (OMUS).[2][3]
Ultrasonic Transducers are also used in acoustic levitation.[4]
Use in medicine
Medical ultrasonic transducers (probes) come in a variety of different shapes and sizes for use in making cross-sectional images of various parts of the body. The transducer may used in contact with the skin, as in fetal ultrasound imaging, or inserted into a body opening such as the rectum or vagina. Clinicians who perform ultrasound-guided procedures often use a probe positioning system to hold the ultrasonic transducer.
Use in industry
Ultrasonic sensors can detect movement of targets and measure the distance to them in many automated factories and process plants. Sensors can have an on or off digital output for detecting the movement of objects, or an analog output proportional to distance. They can sense the edge of material as part of a web guiding system.
Ultrasonic sensors are widely used in cars as parking sensors to aid the driver in reversing into parking spaces. They are being tested for a number of other automotive uses including ultrasonic people detection and assisting in autonomous UAV navigation.
Because ultrasonic sensors use sound rather than light for detection, they work in applications where photoelectric sensors may not. Ultrasonics are a great solution for clear object detection and for liquid level measurement, applications that photoelectrics struggle with because of target translucence. As well, target color or reflectivity do not affect ultrasonic sensors, which can operate reliably in high-glare environments.
Passive ultrasonic sensors may be used to detect high-pressure gas or liquid leaks, or other hazardous conditions that generate ultrasonic sound. In these devices, audio from the transducer (microphone) is converted down to human hearing range.
High-power ultrasonic emitters are used in commercially available ultrasonic cleaning devices. An ultrasonic transducer is affixed to a stainless steel pan which is filled with a solvent (frequently water or isopropanol). An electrical square wave feeds the transducer, creating sound in the solvent strong enough to cause cavitation.
Ultrasonic technology has been used for multiple cleaning purposes. One of which that is gaining a decent amount of traction in the past decade is ultrasonic gun cleaning.
Ultrasonic testing is also widely used in metallurgy and engineering to evaluate corrosion, welds, and material defects using different types of scans.
References
- Carotenuto, Riccardo; Merenda, Massimo; Iero, Demetrio; Della Corte, Francesco G. (July 2019). "An Indoor Ultrasonic System for Autonomous 3-D Positioning". IEEE Transactions on Instrumentation and Measurement. 68 (7): 2507–2518. doi:10.1109/TIM.2018.2866358.
- Westerveld, Wouter J (2014). Silicon photonic micro-ring resonators to sense strain and ultrasound (Ph.D.). Delft University of Technology. doi:10.4233/uuid:22ccedfa-545a-4a34-bd03-64a40ede90ac. ISBN 9789462590793.
- S.M. Leinders, W.J. Westerveld, J. Pozo, P.L.M.J. van Neer, B. Snyder, P. O’Brien, H.P. Urbach, N. de Jong, and M.D. Verweij (2015). "A sensitive optical micro-machined ultrasound sensor (OMUS) based on a silicon photonic ring resonator on an acoustical membrane". Scientific Reports. 5: 14328. Bibcode:2015NatSR...514328L. doi:10.1038/srep14328. PMC 4585719. PMID 26392386.CS1 maint: uses authors parameter (link)
- Vieira, Silvio L.; Andrade, Marco A.B. (2020). "Translational and rotational resonance frequencies of a disk in a single-axis acoustic levitator". Journal of Applied Physics. Journal of Applied Physics Vol.127. 127 (22): 224901. Bibcode:2020JAP...127v4901V. doi:10.1063/5.0007149.
Further reading
- Escolà, Alexandre; Planas, Santiago; Rosell, Joan Ramon; Pomar, Jesús; Camp, Ferran; Solanelles, Francesc; Gracia, Felip; Llorens, Jordi; Gil, Emilio (2011-02-28). "Performance of an Ultrasonic Ranging Sensor in Apple Tree Canopies". Sensors. 11 (3): 2459–2477. doi:10.3390/s110302459. ISSN 1424-8220. PMC 3231637. PMID 22163749.