Axial flux motor
An axial flux motor (also known as an axial gap motor, or pancake motor) is a geometry of motor construction where the gap between the rotor and stator, and therefore the direction of magnetic flux between the two, is aligned parallel with the axis of rotation, rather than radially as with the concentric cylindrical geometry of the more common radial gap motor.[1]

Although this geometry has been used since the first electromagnetic motors were developed, its usage was rare until the widespread availability of strong permanent magnets and the development of brushless DC motors, which could better exploit some of the advantages of the axial geometry. The axial geometry can be applied to almost any operating principle (e.g. brushed DC, induction, stepper, reluctance) that can be used in a radial motor, and can allow some topologies that would not be practical in a radial geometry, but even for the same operating principle there are considerations in the application and design that would cause one geometry to be more suitable than the other. Axial motors are typically shorter and wider than an equivalent radial motor.
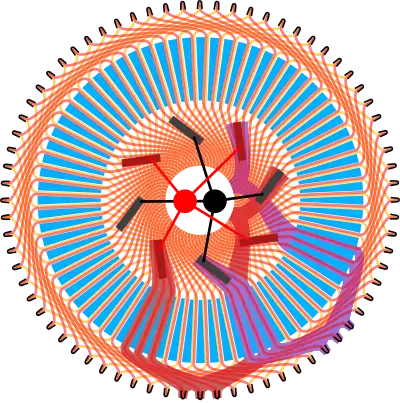
Axial motors have been used for some time for low-power low-cost brushless DC motors, since the motor can easily be built directly upon a PCB, or even using PCB traces as the stator windings, but recently there have been more efforts to design high-power brushless motors in an axial geometry.[2] A successful brushed DC axial motor is the Lynch motor, where the rotor is almost entirely composed of flat copper strips with small iron cores inserted allowing very power-dense operation.
Benefits
- A motor can be built upon any flat structure, such as a PCB, with only the addition of coils and a bearing.
- The coil winding process may be significantly simpler, as well as the process of joining the coil and core.
- Since the coils are flat, rectangular copper strips can more easily be used allowing high-current windings to be simplified.
- It is often possible to make the rotor significantly lighter.
- The rotor-stator gap can be adjusted without machining new parts.
- Potentially shorter magnetic path length.
- Most structural components are flat and can be produced without custom casting or stamping tooling.
- Grain-oriented electrical steel can be easily used in the rotor, having higher permeability and lower core losses.
Detriments
- The rotor is typically much wider causing:
- Increased rotational inertia.
- Increased centrifugal forces which can limit the maximum speed.
- The overall dimensions are generally significantly wider for the same power density.
- Uneven flux distribution due to wedge-shaped segments.
- Coils that are not between two magnets cannot easily make use of laminated cores.
- Since the segments narrow towards the centre there is less room to arrange windings and connections there.
References
- Parviainen, Asko (April 2005). "Design of axial-flux permanent-magnet low-speed machines and performance comparison between radial-flux and axial-flux machines" (PDF). MIT.
- Moreels, Daan; Leijnen, Peter (30 Sep 2019). "This Inside-Out Motor for EVs Is Power Dense and (Finally) Practical". IEEE. Retrieved 2 August 2020.