Lycoming ALF 502
The Lycoming ALF 502/LF 507 (now Honeywell) is a geared turbofan engine produced by Lycoming Engines, AlliedSignal, and then Honeywell Aerospace.
ALF 502/LF 507 | |
---|---|
![]() | |
ALF 502 removed from a Bombardier Challenger 600-1A11 | |
Type | Geared turbofan |
National origin | United States |
Manufacturer | Lycoming Engines Honeywell Aerospace |
First run | 1980 |
Major applications | Bombardier Challenger 600 British Aerospace 146 Northrop YA-9 |
Developed from | Lycoming T55 |
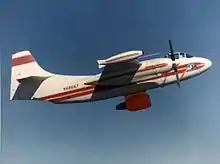
The original YF102 was developed at the Stratford Army Engine Plant in Connecticut, by adding a fan to the Lycoming T55 engine, which was used as the gas generator.[1] Six engines were built for the Northrop YA-9 prototype ground-attack aircraft. These engines were later reused in the C-8A Quiet Short-Haul Research Aircraft (QSRA).
The ALF 502 was certified in 1980 and used on the British Aerospace 146 and Bombardier Challenger 600. The derated FADEC-equipped LF 507 was used on the Avro RJ update of the BAe 146.
Variants
_Canadair_CL-600-1A11_Challenger_600_taxiing_at_Wagga_Wagga_Airport_(3)_(cropped).jpg.webp)
The ALF502 is a high bypass turbofan with geared fan, axial-centrifugal flow high pressure compressor, reverse flow annular combustor, two-stage high pressure turbine, two-stage low pressure turbine:[2]
- ALF502R-3 (single-stage LP compressor)
- ALF502R-4: R-3 with higher thrust
- ALF502R-5: R-4 with improved first-stage and second-stage turbine nozzle assemblies
- ALF502R-3A: R-3 with gas producer turbine improvements, but operated at higher thrust
- ALF502L (two-stage LP compressor)
- ALF502L-2: L with fan blade modification for increased altitude performance
- ALF502L-3: L-2 with turbine improvements and automatic power reserve features
- ALF502L-2A: L-2 with gas producer turbine improvements and automatic power reserve features
- ALF502L-2C: L-2A without automatic power reserve
- ALF502R-6: L-2C with R-5 accessory gearbox
- LF507-1H: R-6 with lower, flat-rated thrust
- LF507-1F: 507-1H with a single-channel FADEC with hydromechanical backup
Proposed variants
In 1972, Lycoming and NASA published a study describing the ALF504, a 12.5 bypass ratio engine producing 8,370 lbf (3,800 kgf; 37.2 kN) of sea-level thrust at a specific fuel consumption of 0.302 lb/(lbf⋅h) (8.6 g/(kN⋅s)) and a fan tip diameter of 48.0 in (1,220 mm).[3]
Lycoming announced its LF500 family of turbofans in September 1988, starting with the LF507-1H and LF507-1F, which were certificated in October 1991 and March 1992, respectively.[1]:198 In June 1992, the company outlined improvements to the LF500 family's core, which included a wide-chord fan to move more air, uprated fan gearbox, three-stage power turbine (an increase from two stages), more lighter-weight composite materials, increased diameter in the first three stages of the axial compressor to increase airflow by 17 percent, an improved impeller (centrifugal compressor) with lean-back vanes, a 16-lobe forced exhaust mixer to reduce noise and specific fuel consumption (SFC), an advanced combustor, and a temperature margin increase of 248 °F (120 °C) in the turbine.[4] Lycoming introduced the 500 Series of common core engines of turboprops and turbofans in February 1994 as a derivative of the LF507 to power regional aircraft in the late 1990s.[1]:198, 199, 200 A turboprop version also was planned for the European Future Large Aircraft military transport (which would eventually become the Airbus A400M). AlliedSignal, which took over Lycoming in October 1994,[5] demonstration tested the common core in December; the core was capable of producing 20,000 lbf (89 kN) of thrust.[6] After losing the competition to power the de Havilland Dash 8-400 regional turboprop, AlliedSignal abandoned the common core effort in July 1995.[7]
- Common Core engines (LF500 family/Lycoming 500 Series/AlliedSignal AS800)
- LF508B2: A 7,900 lbf thrust (35 kN) engine offered for the quad-turbofan powered, 120-seat British Aerospace Regional JetLiner (formerly BAe 146) in 1992[4]
- LF509: A 9,000 lbf thrust (40 kN) turbofan engine for the Avro RJ100[8]
- LF511D: An 11,000 lbf thrust (49 kN) turbofan with a 43 in diameter (1.09 m) wide-chord fan, a three-stage power turbine, and a three-stage low-pressure booster compressor[4]
- LF512 / LF514: Additional turbofan engines of 12,000–14,000 lbf (53–62 kN) thrust, possibly for Avro's proposed 120-seat RJX twin airliner or for a stretched version of the 50-seat Canadair Regional Jet[8]
- LF518: An 18,000 lbf (80 kN) turbofan variant.[9]
- LP512: Turboprop engines targeted for the de Havilland Dash 8-400 and the proposed ATR 82, having an initial power output of 7,500 shp (5,600 kW) but with uprate capability to 11,000 shp (8,200 kW)[1]:200
Applications
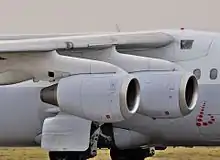
- YF102
- Northrop YA-9
- C-8A Quiet Short-Haul Research Aircraft
- ALF 502
- Bombardier Challenger 600: early CL-600 (1A11) series, 81 built from 1978 to 1982
- British Aerospace 146
- LF 507
- Avro RJ
Specifications
Variant | ALF502R-3 | ALF502R-4/5/3A | ALF502L/L-2/L-3/L-2A/L-2C/R-6 | LF507-1H/1F | ||||||||
---|---|---|---|---|---|---|---|---|---|---|---|---|
Configuration | High bypass, geared fan | |||||||||||
Fan diameter | 40.25 in (1,022 mm)[10] | |||||||||||
Gear ratio | 2.3:1[11] | |||||||||||
Bypass ratio | 5.7:1 | |||||||||||
Compressor | 1 LP, 7-stage axial[10] + centrifugal HP | 2 LP, 7-stage axial[10] + centrifugal HP | ||||||||||
Combustor | Reverse flow annular | |||||||||||
Turbine | Two-stage HP, two-stage LP | |||||||||||
Takeoff thrust | 6,700 lbf (30 kN) | 6,970 lbf (31.0 kN) | 7,500 lbf (33 kN) | 7,000 lbf (31 kN) | ||||||||
Length | 63.66 in (1,617 mm) | 65.57 in (1,665 mm) | ||||||||||
Height | 55.5 in (1,410 mm) | 54.5 in (1,380 mm) | ||||||||||
Width | 47.8 in (1,210 mm) | 48.6 in (1,230 mm) | ||||||||||
Weight [lower-alpha 1] | 1,336 lb (606 kg) | 1,375 lb (624 kg) (1F: 1,385 lb (628 kg)) | ||||||||||
LP rpm | 7,184 - 7,374 | |||||||||||
HP rpm | 19,280 - 19,760 | |||||||||||
TSFC | 0.406 lb/lbf/h (41.4 kg/kN/h)[10] | |||||||||||
Thrust/weight | 5.01 | 5.22 | 5.45 | 5.09 |
See also
Related development
- Honeywell HTF7000 (AS907), ALF502/LF507 successor
Comparable engines
Geared turbofans
- Garrett TFE731
- Pratt & Whitney PW1000G
- Turbomeca Aspin/Astafan
- IAE SuperFan
- Rolls-Royce/SNECMA M45SD
Related lists
Notes
- includes essential engine accessories but excludes starter, hydraulic pump, integrated drive generator and exhaust nozzle
References
- Leyes, Richard A., II; Fleming, William A. (1999). The history of North American small gas turbine aircraft engines. Reston, VA: National Air and Space Museum and American Institute of Aeronautics and Astronautics (AIAA). ISBN 1-56347-332-1. OCLC 247550535.
- "Type certificate data sheet E6NE" (PDF) (15th ed.). Department of Transportation, Federal Aviation Administration (FAA). June 7, 2002. Lay summary.
- Rauch, Dale (July 1972). Design study of an air pump and integral lift engine ALF-504 using the Lycoming 502 core (Report). National Aeronautics and Space Administration (NASA). hdl:2060/19730004744. Lay summary.
- Warwick, Graham (June 17, 1992). "Lycoming outlines LF500 power increase". Flight International. Vol. 141 no. 4323. p. 8. ISSN 0015-3710 – via Gale Research.
- Kandebo, Stanley (November 7, 1994). "AlliedSignal completes Lycoming acquisition". Aviation Week & Space Technology. Vol. 141 no. 19. p. 35. ISSN 0005-2175.
- "AlliedSignal runs demo test on former Lycoming 'Common Core' engine". Commuter Regional Airline News. Vol. 12 no. 50. December 26, 1994. pp. 6+. ISSN 1040-5402 – via Gale Research.
- "AlliedSignal plans turbine closure". FlightGlobal. July 11, 1995. Retrieved July 16, 2020.
- "Textron Lycoming studies 9,000 lb-thrust LF509 for 'developed' RJ100". Commuter Regional Airline News. Vol. 12 no. 28. July 18, 1994. p. 2. ISSN 1040-5402 – via Gale Research.
- Sweetman, Bill (October 1994). "New power for regionals". Finance, markets & industry. Interavia. Vol. 49 no. 583. Minneapolis, Minnesota, U.S.A. pp. 16–18. ISSN 1423-3215. OCLC 199793280 – via EBSCOhost.
- "ALF 502 turbofan engine". Honeywell Aerospace. November 29, 2010. Archived from the original on March 5, 2012.
- Warwick, Graham (25 August 1993). "Engine for change". Flight International. Vol. 144 no. 4384. pp. 39+. ISSN 0015-3710 – via Gale Research.
External links
![]() |
Wikimedia Commons has media related to Lycoming ALF 502. |