Lyocell
Lyocell is a form of rayon. It consists of cellulose fibre, made from dissolving pulp and then reconstituting it by dry jet-wet spinning. The fibre is used to make textiles for clothing and other purposes.[1] Unlike rayon made by the viscose process, lyocell production does not use harmful carbon sulfide,[2][3] which is toxic to workers and the environment.[4][5][2] As of 2018, the lyocell process is more expensive than the more common viscose process for making rayon.[2]
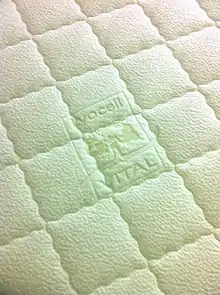
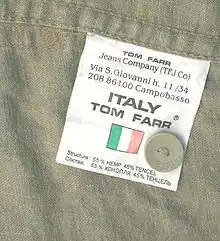
"Lyocell" has become a genericized trademark, used to refer to the lyocell process for making cellulose fibers.[3][6] The U.S. Federal Trade Commission defines lyocell as a fibre "composed of cellulose precipitated from an organic solution in which no substitution of the hydroxyl groups takes place and no chemical intermediates are formed". It classifies the fibre as a sub-category of rayon.[7]
History
The lyocell process was developed in 1972 by a team at the now defunct American Enka fibers facility at Enka, North Carolina. In 2003, this development was recognised by the American Association of Textile Chemists and Colorists (AATCC) by the awarding of their Henry E. Millson Award for Invention. The operating name for the fibre inside the Enka organization was "Newcell", and the development was carried through pilot plant scale before the work was stopped. The fibre was developed further as Tencel in the 1980s by Courtaulds Fibres in Coventry, UK, and at the Grimsby, UK, pilot plant.[8] The process was first commercialised at Courtaulds' rayon factories at Mobile, Alabama (1990), and at the Grimsby plant (1998). In 1998, Courtaulds was acquired by Akzo Nobel, who combined the Tencel division with other fibre divisions under the Accordis banner, prior to selling them off to private equity (CVC Partners). In 2000, CVC sold the Tencel division to Lenzing AG, who combined it with their "Lenzing Lyocell" business, but maintained the brand name Tencel.[6]
The company Birla also sells it under the brand name "Excel".[9]
Uses
.jpg.webp)
As of 2010, lyocell is more expensive to produce than cotton or viscose rayon. It is used in many everyday fabrics. Staple fibres are used in clothes such as denim, chino, underwear, casual wear, and towels. Filament fibres, which are generally longer and smoother than staple fibres,[10] are used in items that have a silkier appearance such as women's clothing and men's dress shirts. Lyocell may be blended with a variety of other fibres such as silk, cotton, rayon, polyester, linen, nylon, and wool. Lyocell also is used in conveyor belts, specialty papers, and medical dressings.[11]
Properties
Lyocell shares many properties with other fibres such as cotton, linen, silk, ramie, hemp and viscose rayon, (to which it is very closely related chemically). Lyocell fiber can absorb around 20% of its own weight in moisture. The vapour and sweat absorption rate, also known as wicking ability, is better than cotton or hemp, (8%), but not as good as wool (30%). Wicking is an important property for blankets and outdoor active wear.
Compared to cotton, consumers often say Lyocell fibres feel softer, and "airier", due to its better ability to wick moisture. Industry claims of higher resistance to wrinkling are as yet unsupported. Lyocell fabric may be machine washed or drycleaned. It drapes well, and may be dyed many colors, needing slightly less dye than cotton to achieve the same depth of colour. [12][9]
Manufacturing process
The lyocell process uses a direct solvent rather than indirect dissolution such as the xanthation-regeneration route in the viscose process. Lyocell fiber is produced from dissolving pulp, which contains cellulose in high purity with little hemicellulose and no lignin. Hardwood logs (such as oak and birch[13]) are chipped into squares about the size of postage stamps. The chips are digested chemically, either with the prehydrolysis-kraft process or with sulfite process, to remove the lignin and hemicellulose. The pulp is bleached to remove the remaining traces of lignin, dried into a continuous sheet and rolled onto spools. The pulp has the consistency of thick posterboard paper and is delivered in rolls weighing some 500 lb (230 kg).
- N-Methylmorpholine N-oxide is a key solvent in the lyocell Process
At the lyocell mill, rolls of pulp are broken into one-inch squares and dissolved in N-methylmorpholine N-oxide (NMMO[2]), giving a solution called "dope". The filtered cellulose solution is then pumped through spinnerets, devices used with a variety of synthetic fibres. The spinneret is pierced with small holes rather like a showerhead; when the solution is forced through it, continuous strands of filament come out. The fibres are drawn in air to align the cellulose molecules, giving the lyocell fibres its characteristic high strength. The fibres are then immersed into a water bath, where desolvation of the cellulose sets the fibre strands. The bath contains some dilute amine oxide in a steady state concentration. Then the fibres are washed with de-mineralised water. Next, the lyocell fibre passes to a drying area, where the water is evaporated from it.
Manufacture then follows the same route as with other kinds of fibers such as viscose. The strands pass to a finishing area, where a lubricant, which may be a soap or silicone or other agent, depending on the future use of the fibre, is applied. This step is basically a detangler, prior to carding and spinning into yarn. At this stage, the dried, finished fibres are in a form called tow, a large untwisted bundle of continuous lengths of filament. The bundles of tow are taken to a crimper, a machine that compresses the fibre, giving it texture and bulk. The crimped fibre is carded by mechanical carders, which perform an action like combing, to separate and order the strands. The carded strands are cut and baled for shipment to a fabric mill. The entire manufacturing process, from unrolling the raw cellulose to baling the fibre, takes about two hours. After this, the lyocell may be processed in many ways. It may be spun with another fibre, such as cotton or wool. The resulting yarn can be woven or knitted like any other fabric, and may be given a variety of finishes, from soft and suede-like to silky.[11]
The amine oxide used to dissolve the cellulose and set the fibre after spinning (NMMO) is recycled. Typically, 99 percent of the amine oxide is recovered.[9] NMMO biodegrades without producing harmful products.[2] Since there is little waste product, this process is relatively eco-friendly, though it is energy-intensive.[9]
See also
References
- Krässig, Hans; Schurz, Josef; Steadman, Robert G.; Schliefer, Karl; Albrecht, Wilhelm; Mohring, Marc; Schlosser, Harald (2002). "Cellulose". Ullmann's Encyclopedia of Industrial Chemistry. Weinheim: Wiley-VCH. doi:10.1002/14356007.a05_375.pub2.
- "Regenerated cellulose by the Lyocell process, a brief review of the process and properties :: BioResources". BioRes. 2018.
- Tierney, John William (2005). Kinetics of Cellulose Dissolution in N-MethylMorpholine-N-Oxide and Evaporative Processes of Similar Solutions (Thesis).
- Swan, Norman; Blanc, Paul (20 February 2017). "The health burden of viscose rayon". ABC Radio National.
- Michelle Nijhuis. "Bamboo Boom: Is This Material for You?". Scientific American.
- "Lenzing Acquires TENCEL®, 2004". Archived from the original on 2010-03-23. Retrieved 2010-01-13.
- 16 CFR 303.7(d)
- Introducing Tencel lyocell
- "Material Guide: How Ethical is Tencel?". Good On You. 2018-07-27. Retrieved 2020-07-21.
- Yates, Marypaul (2002). Fabrics: a guide for interior designers and architects (1st ed.). New York: Norton. ISBN 978-0-393-73062-3.
- Kadolph, Sara; Langford, Anna (2002). Textiles (Ninth ed.). Prentice Hall.
- FiberSource
- Lyocell - raw materials
External links
- Blanc, Paul David (2016). Fake silk : the lethal history of viscose rayon. New Haven: Yale University Press. p. 328. ISBN 9780300204667.
- Dissolving of Cellulosics
- Federal Trade Commission webpage on textiles
- Information about the fibre from fibersource.com
- Lenzing's page on lyocell
- OSU fact sheet
- Tencel at Courtaulds: From Genesis to Exodus and Beyond… – By Calvin Woodings
- Uniform Reuse have a long pdf report on fabric properties and suppliers including lyocell
- Lyocell Comparison