Wood gas
Wood gas is a syngas fuel which can be used as a fuel for furnaces, stoves and vehicles in place of gasoline, diesel or other fuels. During the production process biomass or other carbon-containing materials are gasified within the oxygen-limited environment of a wood gas generator to produce hydrogen and carbon monoxide. These gases can then be burnt as a fuel within an oxygen rich environment to produce carbon dioxide, water and heat. In some gasifiers this process is preceded by pyrolysis, where the biomass or coal is first converted to char, releasing methane and tar rich in polycyclic aromatic hydrocarbons.
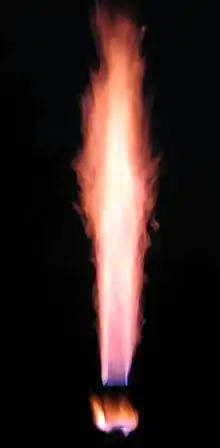
History
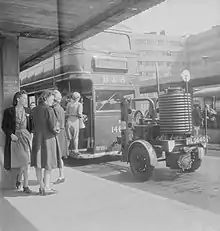
The first wood gasifier was apparently built by Gustav Bischof in 1839. The first vehicle powered by wood gas was built by Thomas Hugh Parker in 1901.[1] Around 1900, many cities delivered syngas (centrally produced, typically from coal) to residences. Natural gas began to be used only in 1930.
Wood gas vehicles were used during World War II as a consequence of the rationing of fossil fuels. In Germany alone, around 500,000 "producer gas" vehicles were in use at the end of the war. Trucks, buses, tractors, motorcycles, ships and trains were equipped with a wood gasification unit. In 1942, when wood gas had not yet reached the height of its popularity, there were about 73,000 wood gas vehicles in Sweden,[2] 65,000 in France, 10,000 in Denmark, and almost 8,000 in Switzerland. In 1944, Finland had 43,000 "woodmobiles", of which 30,000 were buses and trucks, 7,000 private vehicles, 4,000 tractors and 600 boats.[3]
Wood gasifiers are still manufactured in China and Russia for automobiles and as power generators for industrial applications. Trucks retrofitted with wood gasifiers are used in North Korea[4] in rural areas, particularly on the roads of the east coast.
Usage
Internal combustion engine
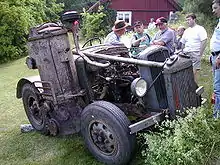
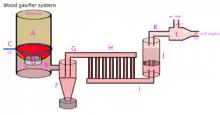
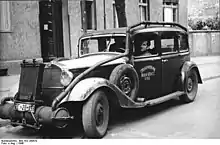
Wood gasifiers can power either spark ignition engines, where all of the normal fuel can be replaced with little change to the carburation, or in a Diesel engine, feeding the gas into the air inlet that is modified to have a throttle valve, if it didn't have it already. On Diesel engines the Diesel fuel is still needed to ignite the gas mixture, so a mechanically regulated Diesel engine's "stop" linkage and probably "throttle" linkage must be modified to always give the engine a little bit of injected fuel, often under the standard idle per-injection volume. Wood can be used to power cars with ordinary internal combustion engines if a wood gasifier is attached. This was quite popular during World War II in several European, African and Asian countries, because the war prevented easy and cost-effective access to oil. In more recent times, wood gas has been suggested as a clean and efficient method to heat and cook in developing countries, or even to produce electricity when combined with an internal combustion engine. Compared to World War II technology, gasifiers have become less dependent on constant attention due to the use of sophisticated electronic control systems, but it remains difficult to get clean gas from them. Purification of the gas and feeding it into natural gas pipelines is one variant to link it to the existing refuelling infrastructure. Liquefaction by the Fischer–Tropsch process is another possibility.
Efficiency of the gasifier system is relatively high. The gasification stage converts about 75% of fuel energy content into a combustible gas that can be used as a fuel for internal combustion engines. Based on long-term practical experiments and over 100,000 kilometres (62,000 mi) driven with a wood gas-powered car, the energy consumption has been 1.54 times higher compared to the energy demand of the same car on petrol, excluding the energy needed to extract, transport and refine the oil from which petrol is derived, and excluding the energy to harvest, process, and transport the wood to feed the gasifier. This means that 1,000 kilograms (2,200 lb) of wood combustible matter has been found to be equivalent to 365 litres (96 US gal) of petrol during real transportation in similar driving conditions and with the same, otherwise unmodified, vehicle.[5] This can be considered to be a good result, because no other refining of the fuel is required. This study also considers all possible losses of the wood gas system, like preheating of the system and carrying of the extra weight of the gas-generating system. In power generation, reported demand of fuel is 1.1 kilograms (2.4 lb) wood combustible matter per kilowatt-hour of electricity.[6]
Gasifiers have been built for remote Asian communities using rice hulls, which in many cases have no other use. One installation in Burma uses an 80 kW modified Diesel-powered electric generator for about 500 people who are otherwise without power.[7] The ash can be used as biochar fertilizer, so this can be considered a renewable fuel.
Exhaust gas emission from an internal combustion engine is significantly lower on wood gas than on petrol.[8] Especially the hydrocarbon emissions are low on wood gas.[9] A normal catalytic converter works well with wood gas, but even without it, emission levels less than 20 ppm HC and 0.2% CO can be easily achieved by most automobile engines. Combustion of wood gas generates no particulates, and the gas renders thus very little carbon black amongst motor oil.[10]
Stoves, cooking and furnaces
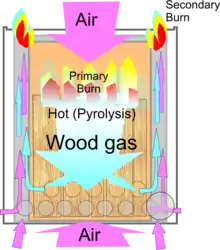
Certain stove designs are, in effect, gasifiers working on the updraft principle: The air passes up through the fuel, which can be a column of rice hulls, and is combusted, then reduced to carbon monoxide by the residual char on the surface. The resulting gas is then burnt by heated secondary air coming up a concentric tube. Such a device behaves very much like a gas stove. This arrangement is also known as a Chinese burner.
An alternative stove based on the down-draft principle and typically built with nested cylinders also provides high efficiency. Combustion from the top creates a gasification zone, with the gas escaping downwards through ports located at the base of the burner chamber. The gas mixes with additional incoming air to provide a secondary burn. Most of the CO produced by gasification is oxidized to CO
2 in the secondary combustion cycle; therefore, gasification stoves carry lower health risks than conventional cooking fires.
Another application is the use of producer gas to displace light density fuel oil (LDO) in industrial furnaces.[11]
Green hydrogen gas is also extracted from the wood gas which is in turn produced from widely available and carbon neutral biomass.[12] All the products of wood gasifier (charcoal, hydro carbon liquids, methane and carbon monoxide) can be converted in to hydrogen by Steam reforming process without external heat input. 5 to 6 kg of dry biomass yields 1 kg of hydrogen with minimum 60% efficiency.
Production
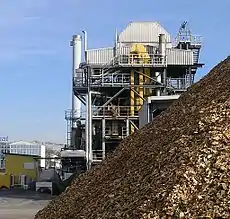
A wood gasifier takes wood chips, sawdust, charcoal, coal, rubber or similar materials as fuel and burns these incompletely in a fire box, producing wood gas, solid ash and soot, the latter of which have to be removed periodically from the gasifier. The wood gas can then be filtered for tars and soot/ash particles, cooled and directed to an engine or fuel cell.[13] Most of these engines have strict purity requirements of the wood gas, so the gas often has to pass through extensive gas cleaning in order to remove or convert, i.e., "crack", tars and particles. The removal of tar is often accomplished by using a water scrubber. Running wood gas in an unmodified gasoline-burning internal combustion engine may lead to problematic accumulation of unburned compounds.
The quality of the gas from different gasifiers varies a great deal. Staged gasifiers, where pyrolysis and gasification occur separately, instead of in the same reaction zone as was the case in, e.g., the World War II gasifiers, can be engineered to produce essentially tar-free gas (less than 1 mg/m3), while single-reactor fluidized bed gasifiers may exceed 50,000 mg/m3 tar. The fluidized bed reactors have the advantage of being much more compact, with more capacity per unit volume and price. Depending on the intended use of the gas, tar can be beneficial, as well by increasing the heating value of the gas.
The heat of combustion of "producer gas" — a term used in the United States meaning wood gas produced for use in a combustion engine — is rather low compared to other fuels. Taylor[14] reports that producer gas has a lower heat of combustion of 5.7 MJ/kg versus 55.9 MJ/kg for natural gas and 44.1 MJ/kg for gasoline. The heat of combustion of wood is typically 15-18 MJ/kg. Presumably, these values can vary somewhat from sample to sample. The same source reports the following chemical composition by volume which most likely is also variable:
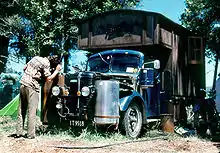
- Nitrogen N2: 50.9%
- Carbon monoxide CO: 27.0%
- Hydrogen H2: 14.0%
- Carbon dioxide CO2: 4.5%
- Methane CH4: 3.0%
- Oxygen O2: 0.6%.
It is pointed out that the gas composition is strongly dependent on the gasification process, the gasification medium (air, oxygen or steam) and the fuel moisture. Steam-gasification processes typically yield high hydrogen contents, downdraft fixed bed gasifiers yield high nitrogen concentrations and low tar loads, while updraft fixed bed gasifiers yield high tar loads.[13][15]
During the production of charcoal for blackpowder, the volatile wood gas is vented. Extremely-high-surface-area carbon results, suitable for use as a fuel in black powder.
See also
References
- "Thomas Hugh Parker".
- Ekerholm, Helena. 'Cultural Meanings of Wood Gas as Automobile Fuel in Sweden, 1930-1945'. In Past and Present energy Societies: How Energy Connects Politics, Technologies and Cultures, edited by Nina Möllers and Karin Zachmann. Bielefeld: Transcript verlag, 2012.
- Wood gas vehicles: firewood in the fuel tank Low-tech Magazine, January 18, 2010
- David Wogan (January 2, 2013). "How North Korea Fuels Its Military Trucks With Trees". Scientific American. Retrieved June 22, 2016.
- Mikkonen, Vesa (2010). Wood Gas for Mobile Applications. Published by the author, available at www.ekomobiili.fi. p. 31.
- Mikkonen, Vesa (2010). Wood Gas for Mobile Applications. Published by the author, available at www.ekomobiili.fi. p. 142.
- Burmese village rice husk gasifier
- Mikkonen, Vesa (2010). Wood Gas for Mobile Applications. Published by the author, available at www.ekomobiili.fi. p. 3.
- Mikkonen, Vesa (2010). Wood Gas for Mobile Applications. Published by the author, available at www.ekomobiili.fi. p. 4.
- Mikkonen, Vesa (2010). Wood Gas for Mobile Applications. Published by the author, available at www.ekomobiili.fi. p. 70.
- Jorapur, Rajeev; Rajvanshi, Anil K. (1997). "Sugarcane leaf-bagasse gasifiers for industrial heating applications". Biomass and Bioenergy. 13 (3): 141–146. doi:10.1016/S0961-9534(97)00014-7.
- "Is This The Best Way To Produce Cheap Hydrogen?". Retrieved 17 July 2020.
- Electricity from wood through the combination of gasification and solid oxide fuel cells, Ph.D. Thesis by Florian Nagel, Swiss Federal Institute of Technology Zurich, 2008
- Taylor, Charles Fayette (1985). Internal-Combustion Engine in Theory and Practice - Vol.1. Cambridge: The MIT Press. pp. 46–47. ISBN 978-0-262-70027-6.
- Handbook of Biomass Downdraft Gasifier Engine Systems (Section 5.2 paragraph 2, pg 30), prepared by the Solar Energy Research Institute, U.S. Department of Energy Solar Technical Information Program, Solar Energy Research Institute, 1988
- Wood gas biochar stoves
External links
![]() |
Wikimedia Commons has media related to Wood gas. |
![]() |
Wikimedia Commons has media related to Gasification. |