Zerovalent iron
Zerovalent iron and other zerovalent metals (ZVI and ZVM, respectively) have a variety of applications ranging from filters to electrodes to trenches. One of the emerging uses for ZVI is iron wall remediation. This technology uses ZVIs to form a permeable reactive barrier (PRB) which filters out contaminants in groundwater, leaving only decontaminated groundwater and dissolved iron on the other side of the PRB.

History
The development of granular metallic iron PRB technology was reliant on two advances: that metallic iron (Fe(0)) breaks down chlorinated organic compounds, and that reactions can proceed in situ under normal groundwater conditions.[1] Metals under their elemental form have been used as consumable redox getters or continuously regenerated catalysts since the 20th century, with more literature available concerning the corrosion of metal shipping and storage containers.[1] Because this literature concerned pure solvents rather than aqueous solutions and the processes often occurred at high temperatures and pressures, it was not looked at by the environmental community.[1] In 1972, zerovalent metals were found to be effective in breaking down pesticides and other chlorinated organic compounds in aqueous solution.[2] However, this finding was also overlooked, perhaps because it was only recorded in patents and it preceded awareness of chlorinated solvents in groundwater as an environmental problem.[1]
Background (theory)
Basic chemistry of iron corrosion
The corrosion reaction involving only the protons of water (anaerobic corrosion) is slow, whereas the corrosion of Fe0 with dissolved oxygen (aerobic corrosion) is fast, presuming there is still enough dissolved O2 present in the ground water at depth.
The two respective reactions are the following:
- Anaerobic corrosion: Fe0 + 2 H2O → Fe2+ + H2 + 2 OH−
- Aerobic corrosion: 2 Fe0 + O2 + 2 H2O → 2 Fe2+ + 4 OH−
The presence of a reducible contaminant (oxidant) can produce another reaction which can then contribute to the overall corrosion rate.[3]
Pathways for contaminant reduction
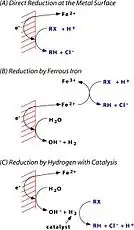
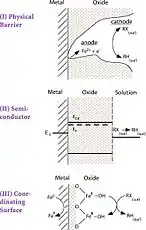
The zerovalent metal (usually granular iron) is the bulk reducing agent in these systems. However, corrosion of iron metal yields Fe2+ and hydrogen, both of which are possible reducing agents for contaminants such as chlorinated solvents. A heuristic model consisting of three possible mechanisms has proven very useful.
Pathway A represents direct electron transfer (ET) for Fe0 to the adsorbed halocarbon (RX) at the metal/water point of contact, resulting in dechlorination and production of Fe2+. Pathway B shows that Fe2+ (resulting from corrosion of Fe0) may also dechlorinate RX, producing Fe3+. Pathway C shows that H2 from the anaerobic corrosion of Fe2+ might react with RX if a catalyst is present.
Hydrogenation also plays a minor role in most systems and iron surfaces will be covered with precipitates of oxides (or carbonates and sulfides) under most environmental conditions. Concern stemming from how the oxide layer mediates transfer of electrons from Fe0 to adsorbed RX led to the formulation of another heuristic model, again consisting of three mechanisms.
In the second model, pathway I shows essentially direct ET from Fe0 to RX in a corrosion pit, or similar defect in the oxide film. Pathway II shows the oxide film mediating ET from Fe0 to RX by acting as a semiconductor. Pathway III shows the oxide film as a coordinating surface containing sites of Fe0 that complex and reduce RX.[4]
Sequestration
Sequestration of a contaminant refers to a removal process which does not involve contaminant degradation. Sequestration by Fe0 typically occurs via adsorption, reduction, and coprecipitation. Often, adsorption is only a prelude to other processes which do transform the contaminant in order to assure that the process cannot be reversed. However, there are cases where adsorption is the sequestration process of primary importance, especially with metals that occur as soluble cations which cannot be reduced to insoluble forms by Fe0. It also can be true in heavy metals, such as Cd, Cu, Hg, etc., which exist predominantly as soluble cations but could be reduced to insoluble species by Fe0.[3]
Type of Metal
Iron
Cast iron, consisting of scrap iron of construction grade, has been used as a reactive material for permeable reactive barriers for groundwater remediation. Reactions are generally believed to occur on the Fe (oxide) surface; however, graphite inclusions have been shown can also serve as a reaction site for 2,4-Dinitrotoluene (DNT)[5]
High purity iron is another category that indicates commercial, granular iron for powder metallurgy, etc.
Zinc and other metals
Zinc has showed much higher reactivity toward pentachlorophenol than iron. This indicates that zinc may be used as a replacement for ZVI in dechlorinating chlorinated phenols. Chlorinated phenols are sequentially dechlorinated and thus less chlorinated phenols have been identified as a reduction product.[6]
Bimetallic combinations
Polychlorinated biphenyls (PCBs) are decontaminated using a treatment system including catalytic ZVM particles and an organic hydrogen donating solvent. The solvent includes water and an alcohol. The treatment system can contain a 2nd solvent, such as d-limonene, toluene, or hexane. The treatment system can contain a thickener, such as calcium stearate or starch. The treatment system can contain a stabilizer, such as glycerin, mineral oil, or vegetable oil. The catalyst consists of zerovalent metal particles, esp. magnesium or iron, coated with a catalytic metal, such as palladium, nickel, or silver. The treatment system provides a paste-like system that is preferably applied to natural media and ex-situ structures.[7]
Nanoscale particles

In addition to using "typical" scale iron in PRBs, nanoparticles (1-100 nm diameter) containing zerovalent iron (nZVI) may be used. There are uncertainties regarding the features of this technology which have made it difficult to engineer applications for optimal performance or to assess the risk to human or ecological health. However, several key facts have been identified related to nZVIs which, if ignored, may lead to misconceptions of the technology. These are as follows: 1) nZVIs used in groundwater remediation are larger than particles that exhibit "true" nano-size effects 2) the high reactivity of nZVI is mainly due to its high specific surface area and 3) the mobility of the nZVI particles will, in almost all relevant scenarios, be less than a few meters (one implication of this limited mobility is that human exposure due to remediation applications of nZVI is likely to be minimal). However, there are still many characteristics of this technology about which very little is known: e.g., how quickly nZVI will be transformed and to what products, whether this residue will be detectable in the environment, and how surface modifications of nZVI will alter its long-term environmental fate and effectiveness for remediation.[4]
The top-down approach for manufacturing nano-ZVMs starts with a large metal particle (granular or microscale) and breaks it down. To do this, either mechanical or chemical means may be used which include but are not limited to milling, etching, and machining. On the other hand, the bottom up approach involves "growing" nanoparticles via chemical synthesis, self-assembling, positional assembling, etc.[8]
Type of contaminants treated
Metals
Chromate is a significant component of many radioactive contaminant plumes. One removal technique involves the addition of scrap metal iron. The reactive surface of ZVI in alkaline waters is a ferrous coating such as green rust.[9]
For arsenic, when selecting the reactive material of the PRB, one must consider the properties of the contaminant. In the case of treating arsenic-contaminated water, materials with a high potential for anion adsorption and coprecipitation are desirable. It is also beneficial to have a high potential to reduce the contaminant to an insoluble solid. For the removal of arsenic, the following is the chemical process involved:[10]
FeCl3 + 3H2O + [As] → [As]Fe(OH)3 + 3H+ + Cl−
Technetium, a radioactive material, is of great concern due to its long half-life and abundance in commercial nuclear waste. Technetium in lower valency states has a lower solubility and sorbs more strongly to soils than does Te7+. ZVI has the potential to remove technetium in groundwater.[11]
To remediate groundwater contaminated by uranium a treatment has been developed to minimize the mobility of uranyl by transferring it to a stable phase. Because the exact mechanism of the decontamination process is unknown, numerous forms of ZVI-materials have been synthesized, including carbon steel, low alloy steel, cast iron, and all other iron-containing alloys.[12]
Non-metal inorganics
Chloramines pose a threat to aquatic ecosystems that are exposed to discharges of treated wastewater. Dechlorination with sulfite reduces the most refractory organic chloramines too slowly to produce wastewater effluents that meet current ecosystem protection criteria in the United States. The aqueous-phase reducing agents that offer speed advantages over sulfite alone include dithionite, thiosulfate, and iodide-mediated sulfite. Ascorbic acid was even more reactive but was found to be slow relative to sulfite. The potential biological oxygen demand might constrain the choice of aqueous reductants. Metallic iron is shown to reduce inorganic and organic chloramines effectively.[13]
Rapid nitrate reduction by iron powder is observed only at pH≤4. pH control with sulfuric acid prolongs nitrate reduction and increases the amount removed.[14] Ammonia is the end product of nitrate reduction and accounts for all nitrate transformed under certain experimental conditions.[14] However, by using nanoscale iron N2 gas is the product instead.[15] Ferrous species, Fe2+ and Fe(OH)2 are probably not involved in the reaction.[14]
Organics
Iron has been shown to be successful at dechlorinating pesticides such as DDT, DDD, and DDE. The rates of dechlorination was independent of the amount of iron; however, the rates with a surfactant (Triton X-114) present were much higher. The rate of dechlorination is limited by the rate of dissolution into the aqueous phase.[16]
Viruses are especially problematic in the environment because they are more mobile and more resistant to chlorination and filtration than are bacteria. Removal of viruses from groundwater involve several different forms of iron, including Fe0, Fe2+, and magnetite. Additionally, viruses can interact with iron in different ways, and thus can be deactivated to different extents.[17]
Modes of application
Permeable reactive barriers
Soil mixing
Permeable reactive barriers can be less effective at greater depths due to construction matters, as most construction techniques involves excavation of the soil and replacing with reactive media. Soil mixing wall (SMW) technology, which is establishing cut-off walls and mixing cement slurries directly with soils under the ground, has become a new technology in soil remediation.[18]
Notes
- Gillham, Robert, John Vogan, Lai Gui, Michael Duchene, and Jennifer Son. "Iron Barrier Walls for Chlorinated Solvent Remediation." In Situ Remediation of Chlorinated Solvent Plumes. Ed. Hans F. Stroo and C. Herb Ward. New York, NY: Springer Science+Business Media, 2010.
- Reynolds GW, Hoff JT, Gillham R W. 1990. Sampling bias caused by materials used to monitor halocarbons in groundwater. Environ Sci Technol 24:135–142
- Tratnyek, P. G.; M. M. Scherer; T. J. Johnson; Matheson, L.J. (2003). Permeable reactive barriers of iron and other zerovalent metals. In: Tarr M. A. (ed.), Chemical Degradation Methods for Wastes and Pollutants; Environmental and Industrial Applications. Environmental Science and Pollution Control, Marcel Dekker, New York, pp 371-421. doi:10.1201/9780203912553.ch9
- Tratnyek, Paul, and Rick Johnson. "Remediation with Iron Metal." Center for Groundwater Research. Oregon Health and Science University, 04 Feb. 2005.
- Jafarpour, B.; Imhoff, P. T.; Chiu. P.C. 2005. Quantification and modeling of 2,4-dinitrotoluene reduction with high-purity and cast iron. Journal of Contaminant Hydrology. 76(1-2): 87-107. doi:10.1016/j.jconhyd.2004.08.001
- Kim, Y. H.; Carraway, E. R. 2003. Dechlorination of chlorinated phenols by zerovalent zinc. Environmental Technology. 24(12): 1455-1463. doi:10.1080/09593330309385690
- Quinn, J. W., K. B. Brooks, C. L. Geiger, and C. A. Clausen. 2007. Bimetallic treatment system and its application for removal and remediation of polychlorinated biphenyls. WO. Patent No. 2007021640. United States of America as Represented by the Adm, 20060807.
- Li, X.; Elliot, D. W.; Zhang, W. 2006. Zerovalent iron nanoparticles for abatement of environmental pollutants: materials and engineering aspects. Critical Reviews in Solid State and Materials Sciences. 31(4): 111-122. doi:10.1080/10408430601057611
- Wander, M. C. F.; Rosso, K.M.; Schoonen, M.A. 2006. Reduction of chromate by ferrous iron and green rust: A comparison of homogeneous vs. heterogeneous electron transfer rates. 232nd ACS National Meeting, San Francisco, CA. Abstracts of Papers, 232nd ACS National Meeting, COLL-509.
- This still needs to be cited, comes from the laminate-cover booklet called "Advances in PRBs for Groundwater Treatment"
- Ding, M.; Schroeder, N.C.; Reimus P.W. 2001. Zerovalent iron as a reducing "getter" for immobilization of technetium. 222nd ACS National Meeting, Chicago, IL. Abstracts of Papers, 222nd ACS National Meeting, Chicago, IL, United States, ENVR-149.
- Baghvand, A. 2003. Immobilization of uranium in groundwater. Journal of Environmental Studies. 29(31): 1-12.
- Bedner, M.; W. A. MacCrehan; G. R. Helz. 2004. Making chlorine greener: investigation of alternatives to sulfite for dechlorination. Water Research. 38(10): 2505-2514. doi:10.1016/j.watres.2004.03.010
- Huang, C.; Wang, H.; Chiu, P. 1998. Nitrate reduction by metallic iron. Water Research. 32(8): 2257-2264. doi:10.1016/S0043-1354(97)00464-8
- Choe, S.; Chang, Y.; Hwang, K.; Khim, J. 1999. Kinetics of reductive denitrification by nanoscale zerovalent iron. Chemosphere. 41(8): 1307-1311. doi:10.1016/S0045-6535(99)00506-8
- Sayles, G. D.; You, G.; Wang, M.; Kupferle, M. J. 1997. DDT, DDD, and DDE dechlorination by zerovalent iron. Environmental Science & Technology. 31(12): 3448-3454. doi:10.1021/es9701669
- Zhang, L.; Chiu, P. C.; Jin, Y. 2006. Remediation and inactivation of viruses with elemental iron. 231st ACS National Meeting, American Chemical Society, Division of Environment. Atlanta, GA. Abstracts of Papers, 231st ACS National Meeting, ENVR-234.
- Ito, H., S. Hino, K. Okunishi, Y. Kinryu, and N. Hamamoto. 2004. Trial for constructing PRBS as application of soil mixing wall. International Conference on Remediation of Chlorinated and Recalcitrant Compounds, 4th, Monterey, CA. Proceedings of the International Conference on Remediation of Chlorinated and Recalcitrant Compounds, 4th, Monterey, CA, United States, May 24–27, 2004, 3A 04/1-3A 04/8.