Fast fashion
Fast fashion is a term used to describe a highly profitable business model based on replicating catwalk trends and high-fashion designs, and mass-producing them at low cost. The term 'fast fashion' is also used to generically describe the products of the fast fashion business model.[1]
Origins
Before the 1800s, fashion was an extensive and almost primitive process where one had to source materials like wool or leather, prepare and weave them into garments. However, the Industrial Revolution amplified the world of fashion by introducing new technology – like the sewing machine, textile machines,[2] ready-made clothing factories and mass production of clothes. All of this resulted in clothes becoming cheaper, easier and quicker to make. Meanwhile, localized dressmaking businesses started to emerge to cater to the middle classes, and they employed workroom employees along with garment workers,[3] who worked from home for meager wages. These types of operations would, later on, lead to the growth of the ‘sweatshops’ that would provide the basis of modern clothing production.[4] During World War II, the trend of more functional styles and fabric restrictions led to the standardized production of clothes. Once the middle-class consumers got accustomed to it, they became more receptive to the idea of mass-produced clothing.
The fashion industry produced and ran clothes for four seasons a year up until the mid-twentieth century, and the designers would work many months in advance to predict what the customers would want. It was in the 1960s and 1970s that this method changed drastically when the young generation started to create new trends and used cheaply-made clothing as a form of personal expression. Although most fashion brands tried to find ways of keeping up with the increasing demand for affordable clothes, there was still a clear distinction between the high-end and High Street fashion. In the late 1990s and early 2000s, fast fashion became a booming industry in America with people enthusiastically partaking in consumerism.[5] Fast fashion retailers such as Zara, H&M, Topshop and Primark took over high street fashion. Initially starting as small stores located in Europe, they were able to infiltrate and gain prominence in the American market by examining and replicating the looks and design elements from runway shows and top fashion houses and quickly reproducing and selling them at a fraction of a cost.[6]
When it comes to question of who was the pioneer of the "fast fashion" phenomenon, it is difficult to pinpoint one particular brand or company. Nevertheless, there is some evidence that suggest the popular fashion brands that helped start the phenomenon. Amancio Ortega, founder of Zara, founded his clothing company in 1963 in Galicia and it featured products that were affordable replications of popular higher-end clothing fashions in addition to producing its own unique designs. Later on in 1975 Ortega opened the first retail outlet in Europe in order to sell his collections in the short run and also to integrate production and distribution in the long run. He eventually was able to move to New York in the early 1990s where the New York Times first coined the term “fast fashion” to describe the mission of his store which said that “it would only take 15 days for a garment to go from a designer's brain to being sold on the racks”.[6] In the article “Fast Fashion Lessons”[7] Donald Sull and Stefano Turconi studies how Zara pioneered an approach to navigate the volatile world of the fast fashion industry. According to Sull and Turconi one of the reasons for Zara’s success was that it built a supply chain and production network where they maintained complicated and capital-intensive operations (like computer-guided fabric cutting) in-house, while it outsourced labor intensive operations (like garment sewing) to a network of local subcontractors and seamstress operatives based in Galicia. Thus with shorter lead times the company was able to respond very quickly when the sale of their products exceeded their expectations and also cut off production for items that didn’t have very high demands. Unlike many fashion companies, Zara hardly invests in television or press promotional campaigns and instead relies on store windows to convey the brand image, spread of word-of-mouth and locating their shops strategically in areas with high consumer traffic.
Similar to Zara, the origin story of H&M also has common traits and technically it has also been the longest running retailer. In 1946 Erling Persson, a Swedish entrepreneur, goes on a trip to the USA where he was greatly intrigued and impressed by the concept of efficient and high-volume production stores that he witnessed in New York. The following year in 1947 Persson establishes a women’s wear store called Hennes (which is Swedish for “Hers”) & Mauritz (also commonly known as H&M) in Västerås, Sweden and then between the years of 1960 and 1979 the company rapidly expands not only in terms of location, with 42 stores across Europe, but also in terms of its clothing to include the whole family. The initial foundation for its global expansion is laid when in the 1980s H&M decides to acquire Rowells, a Swedish mail order company, and use it to shift the sale of their fashion products directly into the customer’s homes. After that in the 1990s H&M decides to invest and capitalize on the transition to large city billboard advertising for their products by using famous celebrities and supermodels wearing their clothes. Finally H&M opens its first flagship store on Fifth Avenue in New York in 2000, which marked the commencement of its international expansion outside of Europe.[8] Zaw Thiha Tun examines the secret of H&M’s success as a company and mentions that the distinct business model of H&M is unlike Zara since they don’t manufacture any of their products in-house. Rather it outsources its production to more than 900 independent suppliers that are mainly located in Europe and Asia and overseen by 30 strategically located oversight offices. At the same time it primarily depends on its state-of-the-art IT infrastructure and network to connect between the central national office and the production offices. This fact proves to be very crucial to their operations since they don’t own factories or secure the fabrics in advance, and thus they have been able to reduce their lead times through continuous developments in the buying process.[9]
Concept
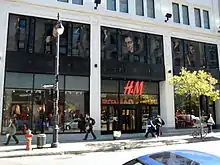
Fast fashion brands produce pieces to get the newest style on the market as soon as possible.[10] They emphasize optimizing certain aspects of the supply chain for the trends to be designed and manufactured quickly and inexpensively and allow the mainstream consumer to buy current clothing styles at a lower price. This philosophy of quick manufacturing at an affordable price is used in large retailers such as H&M, Zara, C&A, Peacocks, Primark, and Topshop. It particularly came to the fore during the vogue for "boho chic" in the mid-2000s.[11] According to the UK Environmental Audit Committee's report "Fixing Fashion," fast fashion "involves increased numbers of new fashion collections every year, quick turnarounds and often lower prices. Reacting rapidly to offer new products to meet consumer demand is crucial to this business model.”[12]
Fast fashion has developed from a product-driven concept based on a manufacturing model referred to as "quick response" developed in the U.S. in the 1980s[13] and moved to a market-based model of "fast fashion" in the late 1990s and first part of the 21st century. The Zara brand name has become almost synonymous with the term, but other retailers worked with the concept before the label was applied, such as Benetton.[14][15] Fast fashion has also become associated with disposable fashion because it has delivered designer product to a mass market at relatively low prices.[16]
Slow fashion counter
The slow fashion or conscious fashion movement has risen in opposition to fast fashion, naming responsibility for pollution (both in the production of clothes and in the decay of synthetic fabrics), poor workmanship, and emphasizing very brief trends over classic style.[17] Elizabeth L. Cline's 2012 book Overdressed: The Shockingly High Cost of Cheap Fashion was one of the first investigations into the human and environmental toll of fast fashion. Fast fashion has also come under criticism for contributing to poor working conditions in developing countries.[18] The 2013 Dhaka garment factory collapse[19] in Bangladesh, the deadliest garment-related accident in world history, brought more attention to the safety impact of the fast fashion industry.[20]
In the rise of slow fashion, emphasis has been given to quality, considerate clothing. In recent Spring/Summer Fashion Show 2020, high end designers are leading the movement of slow fashion by creating pieces that develop environmental friendly practices in the industry.[21] Stella McCartney is one luxury designer who focuses on sustainable and ethical practices, and has done so since the nineties.[22] British Vogue explains that the process of designing and creating clothing in slow fashion involves consciousness of materials, consumers demand, and the climate impact.[21]
Strategy
Management
The primary objective of fast fashion is to quickly produce a product in a cost-efficient manner to respond to fast-changing consumer tastes in as near real time as possible. This efficiency is achieved through the retailers’ understanding of the target market's wants, which is a high fashion-looking garment at a price at the lower end of the clothing sector.[1] Primarily, the concept of category management has been used to align the retail buyer and the manufacturer in a more collaborative relationship.[23] This collaboration occurs as many companies’ resources are pooled to further develop more sophisticated and efficient supply chain models to increase the market's total profit. The fast fashion market utilizes this by uniting with foreign manufacturers to keep prices at a minimum.
Quick response method
Quick Response (QR) was developed to improve manufacturing processes in the textile industry with the aim of removing time from the production system.[24] The U.S. Apparel Manufacturing Association initiated the project in the early 1980s to address a competitive threat to its own textile manufactures from imported textiles in low labour cost countries.[25] During the project lead times in the manufacturing process were halved; the U.S. industry became more competitive for a time, and imports were lowered as a result.[26] The QR initiative was viewed by many as a protection mechanism for the American textile industry with the aim of improving manufacturing efficiencies.[27]
The concept of quick response (QR) is now used to support "fast fashion," creating new, fresh products while also drawing consumers back to the retail experience for consecutive visits.[28] Quick response also makes it possible for new technologies to increase production and efficiency, typified by the introduction of the complementary concept of Fast Fit.[28] The Spanish mega chain Zara, owned by Inditex, has become the global model for how to decrease the time between design and production. This production short cut enables Zara to manufacture over 30,000 units of product every year to nearly 1,600 stores in 58 countries.[29] New items are delivered twice a week to the stores, reducing the time between initial sale and replenishment. As a result, the shortened time period improves consumer's garment choices and product availability while significantly increasing the number of per customer visits per annum. In the case of Renner, a Brazilian chain, a new mini-collection is released every two months.[29]
Marketing
Marketing is the key driver of fast fashion. Marketing creates the desire for consumption of new designs as close as possible to the point of creation. Marketing closes the gap between creation and consumption by promoting this as something fast, low priced, and disposable.[30] The continuous release of new products essentially makes the garments a highly cost effective marketing tool that drives consumer visits, increases brand awareness, and results in higher rates of consumer purchases. Fast fashion companies have also enjoyed higher profit margins in that their markdown percentage is only 15% compared to competitors’ 30% plus. The fast fashion business model is based on reducing the time cycles from production to consumption such that consumers engage in more cycles in any time period. For example, the traditional fashion seasons followed the annual cycle of summer, autumn, winter and spring, but in fast fashion cycles have compressed into shorter periods of 4–6 weeks and in some cases less than this. Marketers have thus created more buying seasons in the same time-space.[31]
Two approaches are currently being used by companies as market strategies; the difference is the amount of financial capital spent on advertisements. While some companies invest in advertising, fast fashion mega firm Primark operates with no advertising. Primark instead invests in store layout, shop-fit and visual merchandising to create an instant hook.[32] The instant hook creates an enjoyable shopping experience, resulting in the continuous return of customers. Research shows that 75 percent of consumers' decisions are made in front of the fixture within three seconds.[23] The alternative spending of Primark also "allows the retailer to pass the benefits of a cost saving back to the consumer and maintain the company's price structure of producing garments at a lower cost".[23]
Production
"Supermarket" market
The consumer in the fast fashion market thrives on constant change and the frequent availability of new products.[28] Fast fashion is considered to be a "supermarket" segment within the larger sense of the fashion market.[23] This term refers to fast fashion's nature to "race to make apparel an even smarter and quicker cash generator".[28] Three crucial differentiating model factors exist within fast fashion consumption: market timing, cost, and the buying cycle.[23] Timing's objective is to create the shortest production time possible. The quick turnover has increased the demand for the number of seasons presented in the stores. This demand also increases shipping and restocking time periods. Cost is still the consumer's primary buying decision. Costs are largely reduced by taking advantage of lower prices in markets in developing countries. In 2004 developing countries accounted for nearly seventy five percent of all clothing exports and the removal of several import quotas has allowed companies to take advantage of the even lower cost of resources.[28] The buying cycle is the final factor that affects the consumer. Traditionally, fashion buying cycles are based around long term forecasts that occur one year to six months before the season.[28] Yet, in the fast fashion market the quick response philosophy can result in higher forecast accuracy because the time period is significantly shortened. A higher sell-through for the goods produced is also a result of the shortened production period.
Supply chain
Supply chains are central to the creation of fast fashion. Supply chain systems are designed to add value and reduce cost in the process of moving goods from design concept to retail stores and finally through to consumption.[33] Efficient supply chains are critical to delivering the retail customer promise of fast fashion. The selection of a merchandising vendor is a key part in the process. Inefficiency primarily occurs when suppliers can't respond quickly enough, and clothing ends up bottlenecked and in back stock.[29] Two kinds of supply chains exist, agile and lean. In an agile supply chain the principal characteristics include the sharing of information and technology.[28] The collaboration results in the reduction in the amount of stock in the megastores. A lean supply chain is characterized as the correct appropriation of the commodity for the product.[28] The combination of the two supply chains is called "leagile".
Vendor relationships
The companies in the fast fashion market also utilize a range of relationships with the suppliers. The product is first classified as "core" or "fashion".[28] Suppliers close to the market are used for products that are produced in the middle of a season, meaning trendy, "fashion" items. In comparison, long-distance suppliers are utilized for cheap, "core" items, sometimes referred to as "capsule" clothing, that are used in collections every season and have a stable forecast.
Internal relationships
Productive internal relationships within the fast fashion companies are as important as the company's relationships with external suppliers, especially when it comes to the company's buyers. Traditionally with a "supermarket" market the buying is divided into multi-functional departments. The buying team uses the bottom-up approach when trend information is involved, meaning the information is only shared with the company's fifteen top suppliers.[28] On the other hand, information about future aims, and strategies of production are shared downward within the buyer hierarchy so the team can consider lower cost production options.[28] The buyers also interact closely with merchandising and design departments of the company because of the buyer's focus on style and color. The buyer must also consult with the overall design team to understand the cohesion between trend forecasting and consumer's wants. The close relationships result in flexibility within the company and an accelerated response speed to the demands of the market.
Sustainable labour costing and efficiency dilemma in fast fashion
Published by University of Manchester, the Working Papers of "Capturing the Gains, global summit" brings together an international network of experts from North and South. The Working Paper 14 focuses on a specific feature of buying behaviour in the UK fashion retail industry: the negotiation of a manufacturing price (cut-make-trim, CMT, cost) with suppliers that does not separately itemize labour cost. This practice, tacitly supported by both buyers and suppliers, is examined against the backdrop of ongoing wage defaulting and import price deflation in the global apparel industry. For obvious reasons, the make-up of standard time using Predetermined Time standards (PTS), Predetermined motion time system (PMTS); is highly technical and ‘synthetic’. According to the International Labour Organization (ILO), as of 1992 there were some 200 different PTS systems, offered by consultancies for adoption by manufacturing companies.[34] In apparel manufacture, three PTS (aka PMTS) consultancy firms specializing in methods-time measurement (MTM) appear to be operating in the sector– the US-based Modular Arrangement of Predetermined Time Standards (MODAPTS), the Sri Lankan-based Seweasy and the UK-headquartered GSD (Corporate) Ltd. All three forms of work measurement for arriving at a standard time should normally make provision for relaxation, contingency and special allowances.
List of fast fashion brands
- Anthropologie
- ASOS.com[35]
- Bershka
- Bestseller
- Boohoo
- C&A
- Charlotte Russe
- Cotton On
- Esprit
- Fashion Nova
- FIVE FOXes
- Free People
- Forever 21
- Gap Inc.
- Giordano
- H&M
- Inditex
- Mango (clothing)
- Metersbonwe
- Missguided
- Miss Selfridge
- Nasty Gal
- New Look
- NewYorker
- Next
- Oysho
- Peacocks
- PrettyLittleThing
- Primark
- Pull & Bear
- Rainbow Shops
- Renner
- Riachuelo
- River Island
- s. Oliver
- Shasa
- Stradivarius (clothing brand)
- Topshop
- United Colors of Benetton
- Uniqlo[36][37]
- Uterqüe
- Urban Outfitters
- Zara[36]
Environmental impact
According to the United Nations Economic Commission for Europe,[38] the fast fashion system provides opportunities for economic growth but the entire fashion industry hinders sustainability efforts by contributing to 20 % of wastewater. In addition, fast fashion is responsible for nearly 10 percent of global gas emissions. Providing insight, the Ellen Macarthur Foundation released study results on fashion and suggests a new circular system. A singular t-shirt requires over 2,000 liters of water to make.[39] Clothing is not utilized to its full potential, the Ellen MacArthur Foundation explains that linear systems are contributing to unsustainable behavior and the future of fashion may need to transition towards a circular system of production and consumer behavior.
Journalist Elizabeth L. Cline, author of Overdressed: The Shockingly High Cost of Cheap Fashion and one of the earliest critics of fast fashion, notes in her article Where Does Discarded Clothing Go?[40] that Americans are purchasing five times the amount of clothing than they did in 1980. Due to this rise in consumption, developed countries are producing more and more garments each season. The United States imports more than 1 billion garments annually from China alone.[41] United Kingdom textile consumption surged by 37% from 2001 to 2005.[42] The Global Fashion Business Journal reported that in 2018, the global fiber production has reached the highest all-time, 107 million metric tons.[43]
The average American household produces 70 pounds (32 kg) of textile waste every year.[44] The residents of New York City discard around 193,000 tons of clothing and textiles, which equates to 6% of all the city's garbage.[40] In comparison, the European Union generates a total of 5.8 million tons of textiles each year.[45] As a whole, the textile industry occupies roughly 5% of all landfill space.[44] The clothing that is discarded into landfills is often made from non-biodegradable synthetic materials.[46]
Greenhouse gases and various pesticides and dyes are released into the environment by fashion-related operations.[47] The United Nations estimated that the business of what we wear, including its long supply chains, is responsible for 10 percent of the greenhouse gas emissions heating our planet.[48] The growing demand for quick fashion continuously adds effluent release from the textile factories, containing both dyes and caustic solutions.[49] In comparison, greenhouse gas emissions from textile production companies is more than international flights and maritime shipping combined annually. The materials used not only affect the environment in textile product, but also the workers and the people who wear the clothes. The hazardous substances affect all aspects of life and release into the environments around them.[50] Optoro estimates that 5 billion pounds of waste is generated through returns each year, contributing 15 million metric tons of carbon dioxide to the atmosphere.[51]
Sustainability
Recycling
Due to the amount of pollution and waste caused by the fashion industry,[52] for-profit groups, like Viletex, and retailers, such as H&M, are working to decrease the industry's environmental footprint and adopt sustainable technologies.[40] Both companies have created programs that encourage recycling from the general public. These programs provide consumers with bins that allow them to dispose of their unwanted garments that will ultimately be transformed into insulation and carpet padding, as well as being used to produce other garments.[40] While these brands are taking initiatives towards sustainability, the authenticity of these initiatives are questionable. By offering this discount, H&M is further promoting or encouraging people to shop more, hence making the intent behind such initiatives taken by fast-fashion brands questionable.
Advances in technologies have offered new methods of using dyes, producing fibers, and reducing the use of natural resources. To decrease the consumption of traditional textiles, Anke Domaske has produced "QMilch," an eco-milk fiber; Virus has produced high-tech sportswear from recycled coffee beans; and Suzanne Lee has created vegetable leather from fermented tea.[53] Many companies have also created various ways to reduce the amount of dyes emitted into the world's waterways as well as the level of water consumption. For example, AirDye saves between 7 and 75 gallons of water per pound of textiles produced while digital printing reduces water usage by 95 percent.[53]
Technology
Fast fashion brands like ASOS.com, Levi’s, Macy's, North Face have turned to sizing technology that use algorithms to solve sizing issues, and give accurate size recommendations on their website to reduce environmental impact on returns. H&M's design team is implementing 3D design, 3D sampling and 3D prototyping to help cut waste, while artificial intelligence can be used to produce small garment runs for specific stores.[54]
Companies are helping support the circular system in fashion production and consumer behavior by renting out clothes to customers with recycled or reuse items. New York & Company Closet and American Eagle Style Drop are examples of rental services that can be offered to customers when subscribed to the program.[55] Tulerie, a smartphone application offers borrowing, renting, or sharing of clothes in local communities across the globe; users have the opportunity to profit by renting clothes as well.[55]
As our global society has become even more interconnected as a result of increased technological innovation, consumers have become more and more aware of the environmental and ethical detriments that the industry causes, and have been initiating waves of smaller social movements via various social media platforms in hopes to slow the impacts of fast fashion. Social media has directly helped increase consumer awareness of the issue behind the fast fashion industry. Rather than placing sole responsibility for radical change in the hands of the companies or designers themselves, social media has allowed for anyone to vocalize their perspectives on this issue, or even take it a step further and take action into their hands. Considering that the Fast Fashion movement calls its user base to expose the harsh environmental and humanitarian injustices imposed by select corporations, it can be perceived that social media platforms facilitate the widening of the Overton Window, or allow for a broader range of unrestricted ideas and discourses. For this particular social movement, Twitter, Instagram, Facebook, LinkedIn and independent blog forums were the primary platforms that inspired individuals, or activist groups would use to educate others on the horrors of the Fast Fashion Movement. While there are certain demographic changes across the realm of these social media platforms, activists used various hashtags to centralize all the relevant content as well as establishing a more consistent and powerful virtual presence. As advocacy groups and concerned individuals started popularizing select hashtags and keywords, the centrality of coverage would allow for the movement to establish stronger network internalities across a plethora of groups and organizations. Twitter posts using these keywords and hashtags are more frequently referenced by journalists or other media publications as opposed to Facebook groups or Instagram posts. The fact that there are a plethora of popular hashtags that renounce the environmental impacts of Fast Fashion, such as #WhoMadeMyClothes, #SecondHandSeptember, #SustainableFashion, #Sustainability and #SlowFashion allows for this movement to maximize the user base that sees the content in hopes that it would lead to a greater level of user engagement.
Design strategies & techniques
According to FutureLearn,[56] which is an online platform offering a plethora of courses to its users, the following design strategies and techniques can be applied to make fast fashion more sustainable:
- Zero Waste Pattern Cutting: This technique eliminates potential textile waste right at the design stage, where the pattern pieces are strategically laid like a jigsaw puzzle onto a precisely measured piece of fabric.
- Minimal Seam Construction: This technique allows faster manufacturing time by lessening the number of seams that are necessary to stitch a garment.
- Design for Disassembly (DfD): The main intention of this strategy involves designing a product in such a way that it can be easily taken apart at the end of its lifespan and this allows the use of fewer materials.
- Craft preservation: This technique combines and incorporates ancestral craft techniques into modern designs and in a way it ensures preservation of traditional craftsmanship through innovation.
- Transformational/Multifunctional: This strategy can be used to design products or garments that could be worn in numerous ways and can even have elements that are reversible. The best real-life example is the Carry on Closet fashion line created and developed by Antithesis.[57]
- Pull Factor Framework: Brands such as L.L Bean and Harvey Nichols implemented a “Pull Factor Framework” which is a new methodology that strives to make sustainable innovation more enticing for consumers and producers alike.[58] One-way brands successfully utilize the Pull Factor Framework is by facilitating radical transparency in various aspects of their business such as their shedding light on their supply chain production or informing their customers about their ethical sourcing methods. In 2013, designer Stella McCartney created a video campaign that exposed the horrendous environmental problems caused by many brands. Since then, she has shifted her business model where the emphasis is placed on creating a totally sustainable brand, ranging from their production methods to their supply chain. Her efforts to promote ethical fashion was a catalyst for many other high fashion and fast fashion brands to change their business models so that they are more environmentally conscious.
Overconsumption
In contrast to modern overconsumption, fast fashion traces its roots to World War II austerity, where high design was merged with utilitarian materials.[59] The business model of fast fashion is based on consumers’ desire for new clothing to wear.[60] In order to fulfill consumer's demand, fast fashion brands provide affordable prices and a wide range of clothing that reflects the latest trends. This ends up persuading consumers to buy more items which leads to the issue of overconsumption. Dana Thomas, author of Fashionopolis, stated that Americans spent 340 billion dollars on clothing in 2012, the same year of the Rana Plaza collapse.[61] Planned obsolescence plays a key role in overconsumption. Based on the study of planned obsolescence in The Economist, fashion is deeply committed to planned obsolescence. Last year's skirts; for example, are designed to be replaced by this year's new models.[62] In this case, fashion goods are purchased even when the old ones are still wearable. The quick response model and new supply chain practices of fast fashion even accelerate the speed of it. In recent years, the fashion cycle has steadily decreased as fast fashion retailers sell clothing that is expected to be disposed of after being worn only a few times.[63]
A recent article about fast fashion in Huffington Post pointed out that in order to make the fast moving trend affordable, fast-fashion merchandise is typically priced much lower than the competition, operating on a business model of low quality and high volume.[60] Low quality goods make overconsumption more severe since those products have a shorter life span and would need to be replaced much more often. Furthermore, as both industry and consumers continue to embrace fast fashion, the volume of goods to be disposed of or recycled has increased substantially. However, most fast-fashion goods do not have the inherent quality to be considered as collectables for vintage or historic collections.[64]
Sweatshops
A sweatshop is a factory where manual workers are employed for their hard labor under very poor working conditions with severe health and safety risks, at extremely low wages, including child labor.[65] The fashion industry is known as the most labor dependent[66] industry, as one in every six person works in acquiring raw materials and manufacturing clothing. With an annual revenue of 19.8 billion dollars last year,[67] H&M - a fast-fashion conglomerate, is the largest producer of clothing in under-developed South Asian and Southeast Asian countries such as India, Bangladesh and Cambodia.[68] Bangladesh – a country known for its cheap labor, is home to four million garment production workers in over 5000 factories, out of which 85% are women.[69] These women are forced to work in unsafe and poor working conditions while receiving a minimum wage of less than US$3, being unable to provide themselves with a livelihood. The only justification for this is the need to achieve unfathomably low costs in order to sell at low prices, which in turn leads to mass impoverishment.
The Rana Plaza was a garment factory in Bangladesh that collapsed in 2013, killing over a thousand workers and being recorded as the deadliest garment-factory incident in history. The five-story building collapsed due to a structural failure. Although the workers noticed cracks appearing on the walls and it was declared as an unsafe environment to work in, employees were still forced to come to work the next day. Garment factory owners do not abide by health and safety regulations due to the fear of disrupting production and losing profits.
Film and media
- The True Cost is a 2015 documentary film focusing on fast fashion that is directed by Andrew Morgan.[70]
- 'How fast fashion adds to the world's clothing waste problem' is a short 2018 documentary created by Marketplace that is a part of the CBC News network.[71]
Design lawsuits and legislation
Lawsuits and proposed legislation in the U.S.
As of 2007, Forever 21, one of the larger fast fashion retailers, was involved in several lawsuits over alleged violations of intellectual property rights.[72] The lawsuits contended that certain pieces of merchandise at the retailer can effectively be considered infringements of designs from Diane von Furstenberg, Anna Sui and Gwen Stefani's Harajuku Lovers line as well as many other well-known designers.[72] Forever 21 has not commented on the state of the litigation but initially said it was "taking steps to organize itself to prevent intellectual property violations".[72]

H.R. 5055
H.R. 5055, or Design Piracy Prohibition Act, was a bill proposed to protect the copyright of fashion designers in the United States.[73] The bill was introduced into the United States House of Representatives on March 30, 2006. Under the bill designers would submit fashion sketches and/or photos to the U.S. Copyright Office within three months of the products’ "publication". This publication includes everything from magazine advertisements to the garment's first public runway appearances.[74] The bill as a result, would protect the designs for three years after the initial publication. If infringement of copyright was to occur the infringer would be fined $250,000, or $5 per copy, whichever is a larger lump sum.[73] The bill was suspended after the House of Representatives session concluded in 2006, this resulted in H.R. 5055 being cleared from the agenda.
H.R. 2033
The Design Piracy Prohibition Act was reintroduced as H.R. 2033 during the first session of the 110th Congress on April 25, 2007.[75] It had goals similar to H.R. 5055, as the bill proposed to protect certain types of apparel design through copyright protection of fashion design. The bill would grant fashion designs a three-year term of protection, based on registration with the U.S. Copyright Office. The fines of copyright infringement would continue to be $250,000 total or $5 per copied merchandise.[75]
See also
References
- "This Is What Fast Fashion Means (Definition, Problems, And Examples)". Retrieved 2020-10-29.
- "Textile Machines Selection Guide | Engineering360". www.globalspec.com. Retrieved 2020-09-24.
- "Garment Workers | WIEGO". www.wiego.org. Retrieved 2020-09-24.
- "What Is Fast Fashion?". Good On You. 2018-08-07. Retrieved 2020-04-02.
- Linden, Annie Radner. "An Analysis of the Fast Fashion Industry". Senior Projects Fall 2016. 30.
- Idacavage, Sara. "Fashion History Lesson: The Origins of Fast Fashion". Fashionista. Retrieved 2020-04-02.
- Sull, Donald; Turconi, Stefano (2008). "Fast fashion lessons". Business Strategy Review. 19 (2): 4–11. doi:10.1111/j.1467-8616.2008.00527.x. ISSN 1467-8616. S2CID 154671050.
- "H&M group | History". hmgroup.com. Retrieved 2020-04-02.
- Tun, Zaw Thiha. "H&M: The Secret to Its Success". Investopedia. Retrieved 2020-04-02.
- Schlossberg, Tatiana (2019-09-03). "How Fast Fashion Is Destroying the Planet". The New York Times. ISSN 0362-4331. Retrieved 2019-10-05.
- See, for example, Sunday Times Style, 17 September 2006
- "Fixing fashion: clothing consumption and sustainability - Environmental Audit Committee". publications.parliament.uk. Retrieved 2019-03-12.
- Lowson, B., R. King, and A. Hunter. 1999. Quick Response - Managing the Supply Chain to Meet Consumer Demand. Chichester: Wiley.
- Hines, T. 2001. "From analogue to digital supply chains: Implications for fashion marketing " In Fashion marketing: Contemporary issues. Eds. T. Hines and M. Bruce. Oxford: Butterworth Heinemann, 26-47
- Hines, T. 2004. Supply chain strategies: Customer driven and customer focused. Oxford: Elsevier.
- Hines, T. (2007) Globalization: Global markets and global supplies, in Hines, T. and M.Bruce. Eds. Fashion Marketing Contemporary Issues 2nd Edn. Oxford, Elsevier
- Cline, Elizabeth L. (2012) Overdressed: The Shockingly High Cost of Cheap Fashion. Penguin Group. New York.
- Taplin, Ian M. (2014). "Who is to blame?: A re-examination of fast fashion after the 2013 factory disaster in Bangladesh". Critical Perspectives on International Business. 10 (1/2): 72–83. doi:10.1108/cpoib-09-2013-0035.
- "2013 Dhaka garment factory collapse", Wikipedia, 2020-04-16, retrieved 2020-05-15
- Hobson, J. (7 July 2013). "To die for? The health and safety of fast fashion". Occupational Medicine. 63 (5): 317–319. doi:10.1093/occmed/kqt079. PMID 23837074.
- Quick, Harriet (6 March 2020). "SS20's Biggest Trend? Slow Fashion That's Rooted In Reality". British Vogue. Retrieved 14 May 2020.
- "5 Sustainable Luxury Designers For Eco-Friendly Fashion". The Good Trade. Retrieved 2020-05-15.
- Sheridan, Mandy; Moore, Christopher; Nobbs, Karinna (2006). "Fast fashion requires fast marketing: The role of category management in fast fashion positioning". Journal of Fashion Marketing and Management. 10: 301–15. doi:10.1108/13612020610679286.
- Hines, T. (2007) Supply Chain Strategies, Structures and Relationships, in Hines, T. and M.Bruce. Eds. Fashion Marketing Contemporary Issues 2nd Edn. Oxford, Elsevier
- Hines, T. 2001. "From analogue to digital supply chains: Implications for fashion marketing " In Fashion marketing: Contemporary issues. Eds. T. Hines and M. Bruce. Oxford: Butterworth Heinemann, 26-47.
- Hunter, N.A. . 1990. Quick Response in Apparel Manufacturing. Manchester The Textile Institute.
- Hines, T. (2004), Supply Chain Strategies: Customer Driven and Customer Focused, Oxford: Elsevier
- Bruce, Margaret; Daly, Lucy (2006). "Buyer behaviour for fast fashion". Journal of Fashion Marketing and Management. 10 (3): 329–44. doi:10.1108/13612020610679303.
- Pfeifer, Margarida O. "Fast and Furious." Latin Trade (English) 15.9 (Sep. 2007): 14-14. Business Source Complete.
- Payne, Alice (2011). "The life-cycle of the fashion garment and the role of Australian mass market designers". The International Journal of Environmental, Cultural, Economic and Social Sustainability. 7 (3): 237–246. doi:10.18848/1832-2077/cgp/v07i03/54938. Retrieved 15 January 2016.
- Hines, Tony. 2001. "Globalization: An introduction to fashion markets and fashion marketing." In Fashion marketing: Contemporary issues. Eds. T. Hines and M. Bruce. Oxford: Butterworth Heinemann, 1-24.
- Baker, Rosie. "Following fast fashion." In-Store (June 2008): 37-39. Business Source Complete. EBSCO.
- Hines, T (2010). "Trends in textile global supply chains". Textiles. 37 (2): 18–20.
- George Kanawaty (1992). Introduction to Work Study. International Labour Office. ISBN 978-9221071082.
- https://www.adweek.com/brand-marketing/as-waste-plagues-the-fast-fashion-industry-asos-is-taking-a-step-toward-sustainability/
- "Uniqlo is Going to Start Producing Clothing at Zara Speeds".
- "Sneaky ways stores like H&M, Zara, and Uniqlo get you to spend more money on clothes".
- Nations, United Nations Economic Commission for EuropeInformation UnitPalais des; Geneva 10, CH-1211; Switzerl. "UN Alliance aims to put fashion on path to sustainability". www.unece.org. Retrieved 2020-03-24.
- https://www.ellenmacarthurfoundation.org/assets/downloads/publications/A-New-Textiles-Economy_Full-Report_Updated_1-12-17.pdf
- Cline, Elizabeth (July 18, 2014). "Where Does Discarded Clothing Go?". The Atlantic. The Atlantic Monthly Group. Retrieved October 24, 2015.
- Muran, Lisa (2007). Profile of H&M: A Pioneer of Fast Fashion. Textile Outlook International. pp. 11–13.
- Black, Sandy (2013). The Sustainable Fashion Handbook. New York: Thames and Hudson. ISBN 978-0500290569.
- "Global fiber production reaches all-time high, preferred cotton share rises". www.themds.com. Retrieved 2019-11-30.
- "Council for Textile Recycling". www.weardonaterecycle.org. Retrieved 2015-11-08.
- DuFault, Amy. "Can 'upcycling' give Haiti's fashion industry a boost?". the Guardian. Retrieved 2015-11-08.
- "Environmental impact of the textile and clothing industry" (PDF). European Parliament.
- "Fast Fashion Is the Second Dirtiest Industry in the World, Next to Big Oil » Page 2 of 3". EcoWatch. Retrieved 2015-11-08.
- https://grist.org/article/a-scrappy-solution-to-the-fashion-industrys-waste-problem/
- Hunter, A.; King, R.; Lowson, B. (1999). Quick Response - Managing the Supply Chain to Meet Consumer Demand. Wiley. ISBN 978-0-471-98833-5.
- MacArthur, Ellen. "A NEW TEXTILES ECONOMY: REDESIGNING FASHION'S FUTURE" (PDF). ellenmacarthurfoundation.
- https://www.bbcearth.com/blog/%3Farticle%3Dyour-brand-new-returns-end-up-in-landfill/
- Claudio, Luz (2007). "Waste Couture: Environmental Impact of the Clothing Industry". Environ. Health Perspect. 115 (9): A449–A454. doi:10.1289/ehp.115-a449. PMC 1964887. PMID 17805407.
- Breyer, Melissa (September 4, 2014). "10 awesome innovations changing the future of fashion". Treehugger. Narrative Content Group. Retrieved October 24, 2015.
- https://www.voguebusiness.com/technology/hm-fast-fashion-sustainability-recycling-hong-kong
- Douglas, Demi (28 August 2019). "8 clothing rental services that let you change your wardrobe in an instant". TODAY.com. Retrieved 14 May 2020.
- FutureLearn. "Sustainable design techniques". FutureLearn. Retrieved 2020-04-03.
- "ANTITHESIS". www.notjustalabel.com. Retrieved 2020-04-03.
- Courtney, Liz. "Fueling the Sustainable Fashion Movement Unlocking "The Pull Factor" to Tip Fashion Toward a Sustainable Future". bbmg.com.
- Chua, Jasmin Malik (29 August 2017). "Fast Fashion's Surprising Origins". Racked. Vox Media. Retrieved 29 August 2017.
- "Where Does Discarded Clothing Go?". The Atlantic. 2014-07-18. Retrieved 2015-11-08.
- Schlossberg, Tatiana (2019-09-03). "How Fast Fashion Is Destroying the Planet". The New York Times. ISSN 0362-4331. Retrieved 2020-02-19.
- "Planned obsolescence". The Economist. ISSN 0013-0613. Retrieved 2015-11-08.
- Carr, D. J.; Gotlieb, M. R.; Lee, N. & Shah, D. V. (2012). "Examining overconsumption, competitive consumption, and conscious consumption from 1994 to 2004: Disentangling cohort and period effects". The Annals of the American Academy of Political and Social Science. doi:10.1177/0002716212449452. S2CID 154754612.
- Gwilt, A. & Rissanen, T. (2011). Shaping sustainable fashion: Changing the way we make and use clothes. Washington DC, London: Earthcan. p. 143.
- "Do Something".
- "Labor-Intensive Industries: How immigration plays a critical role". New American Economy. Retrieved 2020-09-24.
- "Euromonitor".
- "Fashion Revolution". Archived from the original on 2017-12-20.
- "Bangladesh Factsheet" (PDF).
- "The True Cost | A Documentary Film". The True Cost. Retrieved 2017-01-11.
- How fast fashion adds to the world's clothing waste problem (Marketplace), retrieved 2020-04-02
- Casabona, Liza. "Retailer Forever 21 Facing A Slew of Design Lawsuits." WWD: Women's Wear Daily 194.15 (23 July 2007): 12-12. Textile Technology Index. EBSCO.
- United States. Cong. House. Committee on the Judiciary. 109th Cong., 2nd sess. HR 5055. By Goodlatte, Delahunt, Coble and Wexler. 30 Mar. 2006. 13 Nov. 2008 <"Archived copy" (PDF). Archived from the original (PDF) on 2008-10-08. Retrieved 2008-11-13.CS1 maint: archived copy as title (link)>.
- Woyke, Elizabeth. "FASHION'S BID TO KNOCK OUT KNOCKOFFS." Business Week (10 Apr. 2006): 16-16. Business Source Complete. EBSCO.
- United States. Cong. House. Committee on the Judiciary. 110th Cong., 1st sess. HR 2033. By Delahunt, Goodlatte, Maloney and Bono. 25 Apr. 2007. 13 Nov. 2008 <"Archived copy" (PDF). Archived from the original (PDF) on 2010-12-05. Retrieved 2008-11-13.CS1 maint: archived copy as title (link)>.
Further reading
- Anderson, Kim. "Alternative Strategies to the ZARA Fast Fashion Model." AATCC Review 8.4 (Apr. 2008): 33-33. Textile Technology Index. EBSCO.
- Baker, Rosie. "Following fast fashion." In-Store (June 2008): 37-39. Business Source Complete. EBSCO.
- Bruce, Margaret; Daly, Lucy (2006). "Buyer behaviour for fast fashion". Journal of Fashion Marketing and Management. 10 (3): 329–44. doi:10.1108/13612020610679303.
- Casabona, Liza. "Retailer Forever 21 Facing A Slew of Design Lawsuits." WWD: Women's Wear Daily 194.15 (23 July 2007): 12-12. Textile Technology Index. EBSCO.
- "Charlotte Russe Holding Inc." Apparel Magazine 49.9 (May 2008): 16-18. Textile Technology Index. EBSCO.
- Choi, T.M. Fashion Retail Supply Chain Management: A Systems Optimization Approach, CRC Press, 2014.
- Choi, T.M. (Ed.) Fashion Supply Chain Management: Industry and Business Analysis, IGI Global, 2011. ISBN 978-1609607562
- Choi, T.M. Fast Fashion Systems: Theories and Applications, CRC Press, 2013.
- Cole, Michael D. "The Oxford School of Fast Fashion." Apparel Magazine 49.11 (July 2008): 40-41. Textile Technology Index. EBSCO.
- Corcoran, Cate T. "WHERE THE GARMENT FACTORY IS GOING." WWD: Women's Wear Daily 194.129 (19 Dec. 2007): 10-10. Business Source Complete. EBSCO.
- Field, Thomas G Jr. "Focus on: Intellectual Property Tights." U.S. Department of State's Bureau of International Information Programs. 24 Nov. 2008 <https://web.archive.org/web/20081114200938/https://usinfo.state.gov/products/pubs/intelprp/>.
- Gee, Tim. "Fast fashion." Engineer (00137758) 293.7742 (25 Feb. 2008): 16-16. Business Source Complete. EBSCO.
- Hines, Tony, and Margaret Bruce. 2006. Fashion Marketing: Contemporary Issues. Oxford: Elsevier.
- Muran, Lisa. "Profile of H&M: A Pioneer of Fast Fashion." Textile Outlook International (July 2007): 11-36. Textile Technology Index. EBSCO.
- Pfeifer, Margarida O. "Fast and Furious." Latin Trade (English) 15.9 (Sep. 2007): 14-14. Business Source Complete. EBSCO.
- Sheridan, Mandy; Moore, Christopher; Nobbs, Karinna (2006). "Fast fashion requires fast marketing: The role of category management in fast fashion positioning". Journal of Fashion Marketing and Management. 10: 301–15. doi:10.1108/13612020610679286.
- Sull, Donald; Turconi, Stefano (June 2008). "Fast fashion lessons". Business Strategy Review. 19 (2): 4–11. doi:10.1111/j.1467-8616.2008.00527.x.
- Thomas, Dana (2019). Fashionopolis: The Price of Fast Fashion – and the Future of Clothes. Apollo. ISBN 978-1789546064.
- United States. Cong. House. Committee on the Judiciary. 109th Cong., 2nd sess. HR 5055. By Goodlatte, Delahunt, Coble and Wexler. 30 Mar. 2006. 13 Nov. 2008 <https://web.archive.org/web/20081008233839/http://www.aipla.org/Content/ContentGroups/Legislative_Action/109th_Congress/House1/HR5055.pdf>.
- United States. Cong. House. Committee on the Judiciary. 110th Cong., 1st sess. HR 2033. By Delahunt, Goodlatte, Maloney and Bono. 25 Apr. 2007. 13 Nov. 2008 https://web.archive.org/web/20101205023853/http://www.aipla.org/Content/ContentGroups/Legislative_Action/110th_Congress1/House2/HR2033.pdf
- Woyke, Elizabeth. "FASHION'S BID TO KNOCK OUT KNOCKOFFS." Business Week (10 Apr. 2006): 16-16. Business Source Complete. EBSCO.
- Taplin, Ian M (2014). "Who is to blame?: A re-examination of fast fashion after the 2013 factory disaster in Bangladesh". Critical Perspectives on International Business. 10 (1/2): 72–83. doi:10.1108/cpoib-09-2013-0035.
- Zamani, Bahareh; Sandin, Gustav; Peters, Greg M. (20 September 2017). "Life cycle assessment of clothing libraries: can collaborative consumption reduce the environmental impact of fast fashion?". Journal of Cleaner Production. 162: 1368–1375. doi:10.1016/j.jclepro.2017.06.128.