History of the Haber process
The history of the Haber process begins with the invention of the Haber process at the dawn of the twentieth century. The process allows the economical fixation of atmospheric dinitrogen in the form of ammonia, which in turn allows for the industrial synthesis of various explosives and nitrogen fertilizers, and is probably the most important industrial process ever developed during the twentieth century.[1][2]
Well before the start of the industrial revolution, farmers would fertilize the land in various ways, mainly by urinating or defecating well aware of the benefits of an intake of essential nutrients for plant growth. Although it was frowned upon, farmers took it upon themselves to fertilise their fields using natural means and remedies that had been passed down from generation to generation.[3] The 1840s works of Justus von Liebig identified nitrogen as one of these important nutrients. Over time children used to play in the fields and farmers reckoned that that was the reason that their children were so strong.[4] The same chemical compound could already be converted to nitric acid, the precursor of gunpowder and powerful explosives like TNT and nitroglycerine.[5] Scientists also already knew that nitrogen formed the dominant portion of the atmosphere, but inorganic chemistry had yet to establish a means to fix it.
Then, in 1909, German chemist Fritz Haber successfully fixed atmospheric nitrogen in a laboratory.[6][7] This success had extremely attractive military, industrial and agricultural applications. In 1913, barely five years later, a research team from BASF, led by Carl Bosch, developed the first industrial-scale application of the Haber process, sometimes called the Haber-Bosch process.[8][9]
The industrial production of nitrogen prolonged World War I by providing Germany with the gunpowder and explosives necessary for the war effort even though it no longer had access to guano.[10] During the interwar period, the lower cost of ammonia extraction from the virtually inexhaustible atmospheric reservoir contributed to the development of intensive agriculture and provided support for worldwide population growth.[11][12][13] During World War II, the efforts to industrialize the Haber process benefited greatly from the Bergius process, allowing Nazi Germany access to the synthesized fuel produced by IG Farben, thereby decreasing oil imports.
In the early twenty-first century, the effectiveness of the Haber process (and its analogues) is such that more than 99 percent of global demand for synthetic ammonia, a demand which exceeds 100 million tons annually, is satisfied thereby. Nitrogen fertilizers and synthetic products, such as urea and ammonium nitrate, are mainstays of industrial agriculture, and are essential to the nourishment of at least two billion people.[11][14] Industrial facilities using the Haber process (and its analogs) have a significant ecology impact. Half of the nitrogen in the great quantities of synthetic fertilizers employed today is not assimilated by plants but finds its way into rivers and atmosphere as volatile chemical compounds.[15][16]
El Dorado made of nitrogen
For several centuries, farmers knew that certain nutrients were essential for plant growth. In different parts of the world, farmers developed different methods of fertilizing the farmland. In China, human waste was scattered in rice fields. In nineteenth-century Europe, gangs of English graverobbers roamed the Continent, searching for skeletons to grind into fertilizer. Justus von Liebig, German chemist and founder of industrial agriculture, claimed that England had "stolen" 3.5 million skeletons from Europe. In Paris, as many as one million tons of horse dung was collected annually to fertilize city gardens. Throughout the nineteenth century, bison bones from the American West were brought back to East Coast factories.[3]
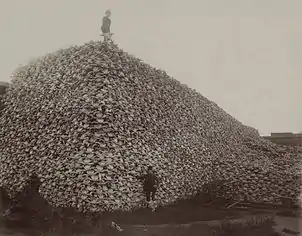
From the 1820s to the 1860s, the Chincha Islands of Peru were exploited for their high quality guano deposits, which they exported to the United States, France and the United Kingdom. The guano-boom increased economic activity in Peru considerably for a few decades until all 12.5 million tons of guano deposits were exhausted.[17][18]
Research was initiated to find alternative sources of fertilizer. The Atacama Desert, at that time part of Peru, was home to significant amounts of Saltpeter (from sodium nitrate). At the time of the discovery of these deposits, the saltpeter had limited agricultural use. Then chemists successfully developed a process to turn the Saltpeter into quality saltpeter to produce gunpowder. The saltpeter, could, in turn, be converted into nitric acid, the precursor of powerful explosives, such as nitroglycerine and dynamite. As exports from this region increased, tensions between Peru and its neighbors increased as well.[19]
In 1879, Bolivia, Chile, and Peru went to war over possession of Atacama Desert, the so-called "Saltpeter War". Bolivian forces were quickly defeated by the Chileans. In 1881, Chile defeated Peru and seized control of nitrate exploitation in the Atacama Desert. Consumption of Chilean saltpeter for agriculture quickly grew and Chileans standard of living rose significantly.[19]
Technological developments in Europe brought an end to these days. In the twentieth century, the minerals from this region "contribute minimally to global nitrogen supply."[20]
A pressing need
In the late nineteenth century, chemists, including William Crookes, President of the British Association for the Advancement of Science in 1898,[21][22] predicted that the demand for nitrogen compounds, either in the form of fertilizer or explosives, would exceed supply in the near future.[23]
Following the work by Claude Louis Berthollet published in 1784, chemists knew ammonia to be a nitrogen compound.[24] Early attempts to synthesize ammonia were performed in 1795 by Georg Friedrich Hildebrandt. Several others were made during the nineteenth century.[25]
In the 1870s, ammonia was an unwanted byproduct of making manufactured gas. Its importance emerged later, and in the 1900s the industry modified their facilities to produce it from coke. Still, production could not meet demand.[26] For example, in 1910, production of fixed nitrogen from coke ovens totaled 230,000 tonnes, while Chile exported around 370,000 metric tonnes.[27]
In 1900, Chile, with its deposits of saltpeter, produced two-thirds of all fertilizer on the planet.[28] However, these deposits rapidly diminished, the industry was dominated by an oligopoly and the cost of saltpeter rose constantly. To ensure food security for Europe's growing population, it was essential that a new economical and reliable method of obtaining ammonia be developed.[29]
Issues of food security were particularly acute in Germany.[30] Its soil was poor and the country lacked an empire. A major consumer of Chilean saltpeter, Germany saltpeter imports totaled 350,000 tonnes in 1900. Twelve years later, it imported 900,000 tonnes. The Unitred States was in much better position due to the Guano Islands Act.[31][32][33]
In the years between 1890 and 1900, chemistry advanced on several fronts, and more scientists attempted to fix atmospheric nitrogen. In 1895, German chemists Adolf Frank and Nikodem Caro succeeded in reacting calcium carbide with dinitrogen to obtain calcium cyanamide, a chemical compound used as a fertilizer. Industrialization of the Frank-Caro process began in 1905. By 1918, there were 35 synthesis sites fixing 325,000 tonnes of nitrogen annually. However, the Cyanamide process consumed large amounts of electrical power and was more labor-intensive than the Haber process.[34] Today, cyanamide is used primarily as a herbicide.[35]
Wilhelm Ostwald, considered one of the best German chemists of the early twentieth century, attempted to synthesize ammonia in 1900 using an invention. He interested BASF, who asked Carl Bosch, a recently hired chemist, to validate the device. After several tests, Bosch concluded the ammonia came from the device itself, not the atmosphere. Ostwald challenged this conclusion, but conceded when Bosch offered proof.[36][37]
In 1901, Henry Le Chatelier, using his own principle, managed to synthesize ammonia from air. After obtaining a patent, he claimed it was possible to obtain better performance by increasing the pressure. When one of his assistants was killed following the accidental explosion of a device, Le Chatelier decided to end his research.[38]
Americans Bradley and Lovejoy, specialists in electrochemistry, developed a method of producing nitric acid using electric arcs. The industrial manufacture of nitric acid using this method began in 1902.[39] Their company soon closed in 1904, as the consumption of electricity made production costs too great.[40]
In 1905, Norwegian physicist Kristian Birkeland, funded by engineer and industrialist Samuel Eyde, developed the Birkeland–Eyde process which fixes atmospheric nitrogen as nitrous oxides.[41] The Birkeland–Eyde process requires a considerable amount of electricity, constraining possible site location; fortunately, Norway possessed several sites capable of meeting these needs. Norsk Hydro was founded 2 December 1905 to commercialize the new process.[42] In 1911, the Norsk Hydro facility was consuming 50,000 kW, the next year, consumption doubled to 100,000 kW.[43] By 1913, Norsk Hydro's facilities were producing 12,000 tonnes of nitrogen, about 5 percent of the volume extracted from coke at the time.[44]
Similar processes were developed at the time. Schönherr, an employee of BASF, worked on a nitrogen fixation process beginning in 1905. In 1919, Schönherr's Badische process was employed at Norsk Hydro facilities.[45] That same year, the Pauling process was used in Germany and the United States.[45]
All these methods were quickly supplanted by the less-expensive Haber process.
A new approach
In 1905, German chemist Fritz Haber published Thermodynamik technischer Gasreaktionen (The Thermodynamics of Technical Gas Reactions), a book more concerned about the industrial application of chemistry than to its theoretical study. In it, Haber inserted the results of his study of the equilibrium equation of ammonia:
- N
2 (g) + 3 H
2 (g) ⇌ 2 NH
3 (g) - ΔH
At 1000 °C in the presence of an iron catalyst, "small" amounts of ammonia were produced from dinitrogen and dihydrogen gas.[46] These results discouraged his further pursuit in this direction.[37] However, in 1907, spurred by a scientific rivalry between Haber and Walther Nernst, nitrogen fixation became Haber's first priority.[37][47] A few years later, Haber used results published by Nernst on the chemical equilibrium of ammonia and his own familiarity with high pressure chemistry and the liquefaction of air, to develop a new nitrogen fixation process.[46][48] He had no precise information on the parameters to impose on the system,[49] but at the conclusion of his research, he was able to establish that an effective ammonia production system must:[50][51][52]
- operate at high pressure (on the order of 20 MPa[53]);
- implement one or more catalysts[54] to accelerate the synthesis of ammonia;
- operate at a high temperature (between 500 °C and 600 °C ) to obtain the best efficiency in the presence of the catalyst;
- since about 5% of the N2(g) and H2(g) molecules react with each passage in the chemical reactor:
- separate the ammonia from the other molecules by liquefaction,
- withdraw ammonia continuously,
- inject again into the chemical reactor the N2(g) and H2(g) molecules that did not react;
- recycle the heat produced.
To overcome the problems associated with high pressure, Haber called upon the talents of Robert Le Rossignol, who designed the equipment necessary for the success of the process.[55] Early in 1909, Haber discovered that osmium could serve as a catalyst. Later, he established that uranium could also act as a catalyst.[56] Haber also obtained good results with iron, nickel, manganese and calcium.[57] In the chemical equation shown above, the direct reaction is exothermic. This heat can be used to heat the reagents before they enter the chemical reactor.[58] Haber's team developed a system that recycles the heat produced.[59]
In March 1909, Haber demonstrated to his laboratory colleagues that he had finally found a process capable of fixing atmospheric dinitrogen sufficient to consider its industrialization.[60]
While BASF took out a patent on the Haber process,[61] August Bernthsen, director of research at BASF, doubted the utility of it. He did not believe that BASF wanted to engage in such a project.[62] According to Bernthsen, no industrial device was capable of withstanding such high pressure and temperature for a long enough period to pay off the investment. In addition, it appeared to him that the catalytic potential of osmium could disappear with use, which required its regular replacement despite the metal being scarce on Earth.[63]
However, Carl Engler, a chemist and university professor, wrote to BASF President Heinrich von Brunck to convince him to talk to Haber. Von Brunck, along with Bernthsen and Carl Bosch, went to Haber's laboratory to determine whether BASF should engage in industrialization of the process. When Bernthsen learned that he needed devices capable of supporting at least 100 atm (about 10 MPa), he exclaimed, "One hundred atmospheres! Just yesterday an autoclave at seven atmospheres exploded on us!"[64] Before deciding, Von Brunck asked for Bosch's advice.[63]
The latter had already worked in metallurgy, and his father had installed a mechanical workshop at home where the young Carl had learned to handle different tools. He had been working for several years on nitrogen fixation, without having obtained any significant results.[65] He knew that processes that used electric arc furnaces, such as the Birkeland-Eyde process, required huge amounts of electricity, making them economically nonviable outside Norway. To continue to grow, BASF had to find a more economical method of fixing.[66] Bosch said, "I think it can work. I know exactly what the steel industry can do. We should risk it."[67]
In July 1909, BASF employees came to check on Haber's success again: the laboratory equipment fixed the nitrogen from the air, in the form of liquid ammonia, at a rate of about 250 milliliters every two hours.[37][68][69] BASF decided to industrialize the process, although it was associated with Norsk Hydro to operate the Schönherr process.[70] Carl Bosch, future head of industrialization of the process, reported that the key factor that prompted BASF to embark on this path was the improvement of the efficiency caused by the catalyst.[71]
References
- Notes
- Schrock, Richard (May 2006). "Nitrogen Fix". Technology Review. Massachusetts Institute of Technology.
- Smil 2001, p. xiii
- Jeffreys 2008, p. 51
- Bensaude-Vincent 2001, pp. 223–226
- Hager 2008, pp. 38, 137–140 and 142–143
- Smil 2001, pp. 61-82
- Hager 2008, pp. 63-108
- Smil 2001, pp. 83–107
- Bosch 1931
- Hager 2008, p. 168
- Smil 2001, p. xv
- Hager 2008, pp. xiii-xiv
- Weast, Robert C., Melvine J. Astle, and William H. Beyer (1983). CRC Handbook of Chemistry and Physics. Boca Raton, FL: CRC Press, Inc. p. B-23. ISBN 0-8493-0464-4.CS1 maint: multiple names: authors list (link)
- Hager 2008, p. xi
- Hager 2008, pp. 272–277
- Smil 2001, pp. 177–198
- Hager 2008, pp. 31–34
- Smil 2001, p. 42
- Hager 2008, pp. 38–43
- Kramer, Deborah A. (January 2003). "Nitrogen (Fixed)—Ammonia" (PDF). U.S. Geological Survey. p. 119.
- Hager 2008, pp. 3-4
- "Sir William Crookes Quotes - Dictionary of Science Quotations and Scientist Quotes". Today in Science History. 2007. Retrieved 22 April 2009.
- Laylin, James (30 October 1993). 1918 Nobel Laureate. Fritz Haber 1868-1934. Nobel Laureates in Chemistry, 1901–1902. American Chemical Society. p. 118. ISBN 0-8412-2690-3.
- Auger, Pierre; Grmek, Mirko D. (1969). Encyclopédie internationale des sciences et des techniques (in French). Verona, Italy: Presses de la cité. p. 434.
- Smil 2001, p. 62
- Haber 1920, pp. 328-329
- Smil 2001, p. 240, Appendix F (quantities from Chilean guano and saltpeter are combined).
- Wisniak 2002, p. 161
- Bachand, Luc, Guy Petit and Philippe Vanier (1996). Chimie 534 (in French). Montreal: LIDEC. p. 315. ISBN 2-7608-3587-1.CS1 maint: multiple names: authors list (link)
- Smil 2001, p. 48
- Hager 2008, p. 52
- "Population of Europe". Historical Atlas. Retrieved 6 April 2009.
- Binoche, Jacques (2003). Histoire des États-Unis (in French). Ellipses Marketing. p. 256. ISBN 978-2-7298-1451-9.
- Hager 2008, pp. 137–143
- "Rich harvest, healthy environment. Calcium cyanamide". Retrieved 18 July 2008.
- Hager 2008, pp. 76-78, 94-96
- Travis 1993
- Wisniak 2002, p. 163
- David V. "Bradley & Lovejoy" (in French). Delcourt. Retrieved 4 March 2009.
- Smil 2001, p. 53
- Witkowski, Nicolas. "Kristian Birkeland, prophète électromagnétique". La Recherche (in French). Retrieved 4 March 2009.
- "Yara - Historique" (in French). Archived from the original on 11 February 2009. Retrieved 4 March 2009.
- Parsons, Chas. L. (Feb 1912). "Mineral Wastes: The Chemists' Opportunity". The Journal of Industrial and Engineering Chemistry. 4 (1): 127. doi:10.1021/ie50038a013.
- Smil 2001, pp. 54–55
- Smith, Alexander (1919). Intermediate Text Book of Chemistry. p. 320.
- Faber, Eduard (1961). Great Chemists. New York: Interscience Publishers. p. 1305.
- Smil 2001, pp. 68–74
- Haber 1920, pp. 336-337
- Hager 2008, p. 81, 91
- Haber 1920, p. 337-338
- Smil 2001, p. 79
- In modern chemical manuals, the authors explain Haber's choices by relying on Le Chatelier's principle. However, at the start of the 20th century, Haber ignored this principle. (See for example Haber 1920, p. 339).
- This was the maximum pressure Haber could obtain with his equipment. Travis 1993
- In Fritz Haber's speech upon receiving his Nobel prize in chemistry, the texts mentions "catalysts" (plural), though it is more probable that the synthesis used only one catalyst at a time. (see Haber 1920, p.337 for more details)
- Smil 2001, p.78-79
- Jayant M. Modak, "Haber Process for Ammonia Synthesis", Resonance, 2002. read online archive [PDF]
- Haber 1920, p.333-335
- In the literature on high-temperature chemical processes, the term "furnace" can replace "chemical reactor."
- Hager 2008, p. 91
- Hager 2008, p.92
- BASF had requested a patent in Germany in 1908: see patent 235 421 Verfahren zur synthetischen Darstellung von Ammoniak aus den Elementen, requested October 13, 1908, approved June 8, 1911
- Nobel Foundation, Carl Bosch - Biography archive, 1931 (accessed March 3, 2009)
- Hager 2008, pp. 92–93.
- Hager 2008, p. 93.
- Bosch had experience with metallic cyanide and nitride. In 1907, he started an experimental site producing cyanide from barium.
- Hager 2008, p. 93-97
- Hager 2008, p. 97
- Hager 2008, p. 99
- Certain authors specify the mass of ammonia. One must simply perform the necessary conversion. For example, in Smil 2001, p. 81, the author mentions 80 g of NH3 per hour, which gives 160 g for two hours. At 0 °C and 191.3 kPa, liquid ammonia has a density of 0.6386 g/cm3.
- Hager 2008, p. 88
- Bosch 1931, p. 197
Bibliography
- Auger, Pierre; Grmek, Mirko D. (1969). Encyclopédie internationale des sciences et des techniques. Verona, Italy: Presses de la Cité. p. 840.
- Bensaude-Vincent, Bernadette (2008). "Fritz Haber : un criminel de guerre récompensé". La Recherche (423): 66–70. ISSN 0029-5671.
- Bensaude-Vincent, Bernadette; Stengers, Isabelle (2001). Histoire de la chimie. Sciences humaines et sociales. Paris: La Découverte/Poche. p. 364. ISBN 2-7071-3541-0.
- Bosch, Carl (1931). The Development of the Chemical High Pressure Method During the Establishment of the New Ammonia Industry (PDF). Oslo, Sweden: Nobel Foundation. p. 45.
- Considine, Glenn D.; Kulik, Peter H. (2002). Ammonia. Van Nostrand's Scientific Encyclopedia, Ninth Edition. Canada: John Wiley & Sons, inc. pp. 140–143. ISBN 0-471-33230-5.
- Haber, Fritz (1920). The Synthesis of Ammonia From its Elements (PDF). Oslo, Sweden: Nobel Foundation. p. 15.
- Hager, Thomas (2008). The Alchemy of Air: A Jewish Genius, a Doomed Tycoon, and the Scientific Discovery That Fed the World but Fueled the Rise of Hitler. New York: Harmony Books. p. 336. ISBN 978-0-307-35178-4.
- Hayes, Peter (2001). Industry and Ideology : IG Farben in the nazi era. New York: Cambridge University Press (published 1971). ISBN 978-0-521-78638-6.
- Jeffreys, Diarmuid (2008). Hell's Cartel: IG Farben and the Making of Hitler's War Machine. Metropolitan Books. p. 496. ISBN 978-0805078138.
- Jones, K.; Bailar, J. C.; Emeléus, H. J.; Nyholm, Sir Ronald Sydney; Trotman-Dickenson, A. F. (1973). Nitrogen. Comprehensive Inorganic Chemistry. New York: Pergamon Press. p. 547. ISBN 0-08-017275-X.
- Lawrence, Stephen A. (2006). "An Introduction to the Amines". Amines. Synthesis, Properties and Applications. Cambridge University Press. p. 384. ISBN 978-0521029728.
- Maxwell, Gary R. (2004). Synthetic Nitrogen Products: A Practical Guide to the Products and Processes. Springer. p. 388. ISBN 978-0306482250.
- Smil, Vaclav (2001). Enriching the Earth: Fritz Haber, Carl Bosch, and the Transformation of World Food Production. MIT Press. p. 358. ISBN 978-0-262-69313-4.
- Travis, Anthony S.; Schröter, Harm G.; Homburg, Ernst; Morris, Peter J. T. (1998). Determinants in the Evolution of the European Chemical Industry, 1900-1939: New Technologies, Political Frameworks, Markets and Companies (Chemists and Chemistry). Springer. p. 300. ISBN 978-0792348900.
- Travis, Tony (1993). "The Haber-Bosch process: exemplar of 20th century chemical industry". Entrepreneur. Society of Chemical Industry.
- Wiley-VCH (2007). Ullmann's Agrochemicals. United States: Wiley-VCH. p. 932. ISBN 978-3527316045.
- Wisniak, Jaime (2002). "Fritz Haber - a Conflicting Chemist" (PDF). Indian Journal of History of Science. 37 (2): 153–173. ISSN 0019-5235.