Mine railway
A mine railway (or mine railroad, U.S.), sometimes pit railway, is a railway constructed to carry materials and workers in and out of a mine.[1] Materials transported typically include ore, coal and overburden (also called variously spoils, waste, slack, culm,[2] and tilings; all meaning waste rock). It is little remembered, but the mix of heavy and bulky materials which had to be hauled into and out of mines gave rise to the first several generations of railways, at first made of wooden rails, but eventually adding protective iron, steam locomotion by fixed engines and the earliest commercial steam locomotives, all in and around the works around mines.[3]
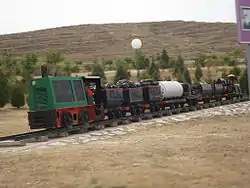
History
Mine rails
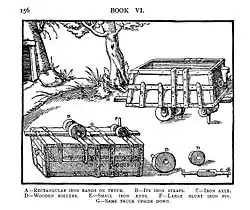
Wagonways (or tramways) were developed in Germany in the 1550s to facilitate the transport of ore tubs to and from mines, using primitive wooden rails. Such an operation was illustrated in 1556 by Georgius Agricola of Germany (Image right).[4] This used "Hund" carts with unflanged wheels running on wooden planks and a vertical pin on the truck fitting into the gap between the planks, to keep it going the right way.[5] Such a transport system was used by German miners at Caldbeck, Cumbria, England, perhaps from the 1560s.[6] An alternative explanation derives it from the Magyar hintó – a carriage. There are possible references to their use in central Europe in the 15th century.[7]
A funicular railway was made at Broseley in Shropshire, England at some time before 1605. This carried coal for James Clifford from his mines down to the river Severn to be loaded onto barges and carried to riverside towns.[8] Though the first documentary record of this is later, its construction probably preceded the Wollaton Wagonway, completed in 1604, hitherto regarded as the earliest British installation. This ran from Strelley to Wollaton near Nottingham. Another early wagonway is noted onwards. Huntingdon Beaumont, who was concerned with mining at Strelley, also laid down broad wooden rails near Newcastle upon Tyne, on which a single horse could haul fifty to sixty bushels (130–150 kg) of coal.[9]
By the 18th century, such wagonways and tramways existed in a number of areas. Ralph Allen, for example, constructed a tramway to transport stone from a local quarry to supply the needs of the builders of the Georgian terraces of Bath. The Battle of Prestonpans, in the Jacobite rising of 1745, was fought astride the 1722 Tranent – Cockenzie Waggonway.[10] This type of transport spread rapidly through the whole Tyneside coalfield, and the greatest number of lines were to be found in the coalfield near Newcastle upon Tyne. They were mostly used to transport coal in chaldron wagons from the coalpits to a staithe (a wooden pier) on the river bank, whence coal could be shipped to London by collier brigs. The wagonways were engineered so that trains of coal wagons could descend to the staithe by gravity, being braked by a brakesman who would "sprag" the wheels by jamming them. Wagonways on less steep gradients could be retarded by allowing the wheels to bind on curves. As the work became more wearing on the horses, a vehicle known as a dandy wagon was introduced, in which the horse could rest on downhill stretches.
Coal, iron, rail symbiosis
A tendency to concentrate employees started when Benjamin Huntsman, looking for higher quality clock springs, found in 1740[11] that he could produce high quality steel in unprecedented quantities (crucible steel to replace blister steel) in using ceramic crucibles in the same fuel shortage/glass industry inspired reverbatory furnaces that were spurring the coal mining, coking, cast-iron cannon foundries, and the much in demand gateway or stimulus products[11] of the glass making industries. These technologies, for several decades, had already begun gradually quickening industrial growth and causing early concentrations of workers so that there were occasional early small factories that came into being.[11]
This trend concentrating effort into bigger central located but larger enterprises[11] turned into a trend spurred by Henry Cort's iron processing patent of 1784[11] leading in short order to foundries collocating near coal mines[3] and accelerating the practice of supplanting the nations cottage industries.[11] With that concentration of employees and separation from dwellings,[3] horsedrawn trams became commonly available as a commuter resource for the daily commute to work.[3] Mine railways were used from 1804 around Coalbrookdale in such industrial concentrations of mines and iron works, all demanding traction-drawing of bulky or heavy loads. These gave rise to extensive early wooden rail ways and initial animal-powered trains of vehicles,[11] then successively in just two decades[3]to protective iron strips nailed to protect the rails, to steam drawn trains (1804), and to cast-iron rails. Later, George Stephenson, inventor of the world-famous Rocket and a board member of a mine, convinced his board to use steam for traction.[12] Next, he petitioned Parliament to license a public passenger railway,[3] founding the Liverpool and Manchester Railway. Soon after the intense public publicity, in part generated by the contest to find the best locomotive won by Stephenson's Rocket, railways underwent explosive growth worldwide, and the industrial revolution gradually went global.[3]
Company towns and child labour
Today, most mine railways are electrically powered; in former times pit ponies, such as Shetland ponies, donkeys, and/or mules were used to haul the early mine trains. In the very cramped conditions of hand-hewn mining tunnels, children were also often used, and the animals were led and tended by boys (called 'mule boys'[13] in the USA, aged 10–12). Until the movement against child labour pushed passage of laws requiring universal mandatory education of children to the sixth grade in the United States, in the Appalachian anthracite coal fields in Eastern Pennsylvania, these urchins were used and known as mule-boys into the 1920s, a position one step up the ladder towards the better pay as an apprentice miner (age 12+) from breaker boys, while the earnings of each stage allowed each group to return considerably more to their hard-scrabble families.
Since many US mines were founded in remote areas and the joint stock companies imported workers from Europe who had to work off their passage in a company town purpose-built to staff the mine – a typical miner's family was constantly in debt to the company for board, rent, groceries, and tools most of their lives, so there was considerable social pressure from family and community for children to earn wages as soon as someone would pay them. Practices in Europe were little different, the mining interests owned the town lands, the buildings, the commercial enterprises established to support the workers from beer gardens, company stores to barbers, dentists, theatres and even doctors' offices. The mining companies even ran the real estate offices, and happily sold lands to all comers so individuals gradually invested in such busy communities, including rights of way to railway companies.
Rails

There is usually no direct connection from a mine railway to the mine's industrial siding or the public railway network, because of the narrow-gauge track that is normally employed. In the United States, the standard gauge for mine haulage is 3 ft 6 in (1,067 mm), although gauges from 18 in (457 mm) to 5 ft 6 in (1,676 mm) are used.[14][15]
Original mine railways used wax-impregnated wooden rails attached to wooden sleepers, on which drams were dragged by men, children or animals. This was later replaced by L-shaped iron rails, which were attached to the mine floor, meaning that no sleepers were required and hence leaving easy access for the feet of children or animals to propel more drams.
Wood to cast iron
These early mine railways used wooden rails, which in the early industrial revolution about Coalbrookdale, were soon capped with iron strapping, those were replaced by wrought iron, then with the first steam traction engines, cast-iron rails,[12] and eventually steel rails as each was in succession found to last much longer than the previous cheaper rail type.[3] By the time of the first steam locomotive-drawn trains, most rails laid were of wrought iron[3] which was outlasting cast-iron rails by 8:1. About three decades later, after Andrew Carnegie had made steel competitively cheap, steel rails were supplanting iron for the same longevity reasons.[3]
Motive power
The tram (or dram) cars used for mine haulage are generally called tubs.[16] The term mine car is commonly used in the United States[17]
Pit ponies
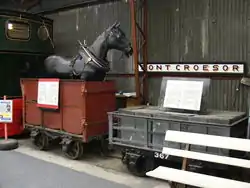
The Romans were the first to realise the benefits of using animals in their industrial workings, using specially bred pit ponies to power supplementary work such as mine pumps.
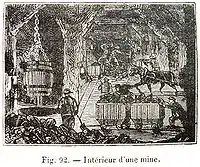
Ponies began to be used underground, often replacing child or female labour, as distances from pit head to coal face became greater. The first known recorded use in Britain was in the County Durham coalfield in 1750; in the United States, mules were the dominant source of animal power in the mine industry, with horses and ponies used to a lesser extent.[18] At the peak in 1913, there were 70,000 ponies underground in Britain. In later years, mechanical haulage was quickly introduced on the main underground roads replacing the pony hauls and ponies tended to be confined to the shorter runs from coal face to main road (known in North East England as "putting", in the United States as "tramming" or "gathering"[19]) which were more difficult to mechanise. As of 1984, 55 ponies were still at use with the National Coal Board in Britain, chiefly at the modern pit in Ellington, Northumberland.
Dandy wagons were often attached to trains of full drams, to contain a horse or pony. Mining and later railway engineers designed their tramways so that full (heavy) trains would use gravity down the slope, while horses would be used to pull the empty drams back to the workings. The Dandy wagon allowed for easy transportation of the required horse each time.
Probably the last colliery horse to work underground in a British coal mine, Robbie, was retired from Pant y Gasseg, near Pontypool, in May 1999.[20]
Cable haulage
In the 19th century after the mid-1840s, when the German invention of wire rope became available from manufactories in both Europe and North America, large stationary steam engines on the surface with cables reaching underground were commonly used for mine haulage. Unsurprisingly, the innovation-minded managers of the Lehigh Coal & Navigation Company pioneered the technology in America using it to allow the dead-lift of loaded coal consists 1,100 feet (340 m) up the Ashley Planes, and the augmentation of their works in and above the Panther Creek Valley[21] with new gravity switchback sections and return cable inclines, but most notably by installing two cable lift sections and expanding the already famous Mauch Chunk Switchback Railway with a 'back track' dropping car return time from 3–4 hours to about 20 minutes, which the new inclines then fed from new mine shafts and coal breakers farther down into the valley.[22] Sometimes, stationary engines were even located underground, with the boiler on the surface, though that was a minority situation. All of the cable haulage methods were primarily used on the main haulage ways of the mine. Typically, manual labor, mules or pit ponies were used in gathering filled cars from the working areas (galleries were driven across seams as much as possible) to main haulage ways.[23] In the first decade of the 20th century, electric locomotives were displacing animal power for this secondary haulage role in mines[24] where sparking triggered explosive methane buildup was a lesser danger. Several cable haulage systems were used:
In slope mines, where there was a continuous downgrade from the entrance to the working face, the rope from the hoisting engine could be used to lower empty cars into the mine and then raise full cars. In shaft mines, secondary hoisting engines could be used to pull cars on grades within the mine. For grades of a few percent, trains of 25 cars each carrying roughly half a ton were typical in the 1880s.[25]
In mines where grades were not uniform or where the grades were not steep enough for gravity to pull a train into the mine, the main hoisting rope could be augmented with a tail rope connected to the opposite end of the train of mine cars. The tail-rope system had its origins on cable-hauled surface inclines prior to the 1830s.[26] This was the dominant system in the 1880s[27] Frequently, one engine was used to work both ropes, with the tail rope reaching into the mine, around a pulley at the far end, and then out again.
Finally, the most advanced systems involved continuous loops of rope operated like a cable car system. Some mines used endless chains before wire-rope became widely available.[28] The endless chain system originated in the mines near Burnley (England) around 1845. An endless rope system was developed in Nottinghamshire around 1864, and another independently developed near Wigan somewhat later (also in England).[29] In these systems, individual cars or trains within the mine could be connected to the cable by a grip comparable to the grips used on surface cable car systems.[30] In some mines, the haulage chain or cable went over the top of the cars, and cars were released automatically when the chain or cable was lifted away by an overhead pulley. Where the cable ran under the cars, a handheld grip could be used, where the grip operator would ride on the front car of the train working the grip chained to the front of the car. In some cases, a separate grip car was coupled to the head of the train.[31] At the dawn of the 20th century, endless rope haulage was the dominant haulage technology for the main haulage ways of underground mines.[24]
Steam locomotives


For as long as it was economical to operate steam locomotives on the general railway system, steam locomotives were also used on the surface trackage of mines. In the 19th and early 20th centuries, some large mines routinely used steam locomotives underground. Locomotives for this purpose were typically very squat tank engines with an 0-4-0 wheel arrangement. Use of steam power underground was only practical in areas with very high exhaust airflow, with engine speed limits of 1/2 the air velocity to assure adequate clean air for the crew on outbound trips. Such engines could not be used in mines with firedamp problems.[32]
Porter, Bell & Co. appears to have built the first underground mining locomotives used in the United States around 1870. By 1874, the Consolidation Coal Company and Georges Creek Coal and Iron Company were using several Porter locomotives in their underground mines in the Georges Creek Valley of Maryland. Other users included several coal mines near Pittsburgh, Pennsylvania, the Lehigh Coal and Navigation Company and an iron mine in the Lake Superior Iron Ranges. Porter's mine locomotives required a minimum 5-foot clearance and 4-foot width when operating on 3-foot gauge track, where they could handle a 20-foot radius curve.[33][34] The Baldwin Locomotive Works built similar locomotives, starting in 1870.[35][36] By the early 20th century, very small British-made oil-fired steam locomotives were in use in some South African mines.[37] Porter and Vulcan (Wilkes-Barre) advertised steam mine locomotives in 1909 and 1911.[38][39] By the early 1920s, only a few small mines in the Pocahontas Coalfield in West Virginia were using steam locomotives underground.[40] Nonetheless, both Baldwin and Vulcan continued to advertise steam locomotives for underground use outside the coal industry as late as 1921.[41]
Compressed air locomotives
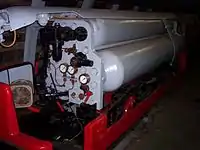
Compressed-air locomotives were powered by compressed air carried on the locomotive in compressed-air containers. This method of propulsion had the advantage of being safe but the disadvantage of high operating costs due to very limited range before it was necessary to recharge the air tanks. Generally, compressors on the surface were connected by plumbing to recharge stations located throughout the mine. Recharging was generally very fast. Narrow gauge compressed air locomotives were manufactured for mines in Germany as early as 1875, with tanks pressurized to 4 or 5 bar.[42] The Baldwin Locomotive Works delivered their first compressed air locomotive in 1877, and by 1904, they offered a variety of models, most with an 0-4-0 wheel arrangement.[43] Compressed air locomotives were introduced in the Newbottle Collieries in Scotland in 1878, operating at 200 psi (14 bar).[44]
Ordinary mine compressed-air systems operating at 100 psi (7 bar) only allowed a few hundred feet of travel. By the late 1880s, Porter was building locomotives designed for 500 to 600 psi (34-41 bar).[45] By the early 1900s, locomotive air tank pressures had increased to from 600 to 800 psi (41-55 bar), although pressures up to 2000 psi (140 bar) were already envisioned.[43] In 1911, Vulcan (Wilkes-Barre) was selling single-tank compressed-air locomotives operating at 800 psi (55 bar), double-tank models up to 1000 psi (69 bar) and one 6-tank model that may have operated at a much higher pressure.[46] The Homestake in South Dakota, USA used such high pressures, with special compressors and distribution piping. Except for very small prospects and remote small mines, battery or diesel locomotives have replaced compressed air.
Overhead-electric locomotives
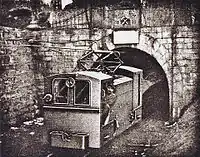
The electric motor technology used pre-1900 to DC with a few hundred volts and a direct supply of power to the motor from the overhead wire enabled the use of efficient, small and sturdy tractors of simple construction. Initially, there was no voltage standard, but by 1914, 250 volts was the standard voltage for underground work in the United States. This relatively low voltage was adopted for safety's sake.[47]
The first electric mine railway in the world was developed by Siemens & Halske for bituminous coal mining in Saxon Zauckerode near Dresden (now Freital) and was being worked as early as 1882 on the 5th main cross-passage of the Oppel Shaft run by the Royal Saxon Coal Works.[48]
In 1894, the mine railway of the Aachen smelting company, Rothe Erde, was electrically driven, as were subsequently numerous other mine railways in the Rhineland, Saarland Lorraine, Luxembourg and Belgian Wallonia. There were large scale deliveries of electric locomotives for these railways from AEG, Siemens & Halske, Siemens-Schuckert Works (SSW) and the Union Electricitäts-Gesellschaft (UEG) in these countries.
The first electric mine locomotive in the United States went into service in mid 1887 in the Lykens Valley Coal Company mine in Lykens, Pennsylvania. The 35 hp motor for this locomotive was built by the Union Electric Company of Philadelphia.[49] The 15000 pound (6800 kg) locomotive was named the Pioneer, and by mid 1888, a second electric locomotive was in service at that mine.[50][51][52] Use in the Appalachian coal fields spread rapidly. By 1903, there were over 600 electric mine locomotives in use in America with new ones being produced at a rate of 100 per year.[53]
Initially, electric locomotives were used only where it was economical to string overhead line for power. This limited their usage for gathering loads at the mine face, where trackage was temporary and frequently relocated. This motivated the development of battery locomotives, but in the first decade of the 20th century the first successful electric gathering locomotives used cable reels. To run on tracks away from overhead lines, the power cable was clipped to the overhead line and then automatically unreeled as the locomotive advanced and reeled up as the locomotive returned.[54][55][56]
Crab locomotives were equipped with a winch for pulling cars out of the un-powered tracks. This approach allowed use of temporary track that was too light to carry the weight of the a cable-reel or battery locomotive. The disadvantage of a crab locomotive was that someone had to pull the haulage cable from the winch to the working face, threading it over pulleys at any sharp turns.[57][58]
Explosion-proof mining locomotives from Schalker Eisenhütte are used in all the mines owned by Ruhrkohle (today Deutsche Steinkohle).
Internal-combustion locomotives
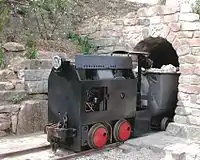
The Gasmotorenfabrik Deutz (Deutz Gas Engine Company), now Deutz AG, introduced a single-cylinder benzine locomotive for use in mines in 1897. Their first mining locomotives were rated at 6 to 8 hp (4.5 to 6.0 kW) and weighed 5,280 pounds (2,390 kg).[59] The original 6 hp (4.5 kW) engine was 8 feet 6.5 inches (2.60 m) long, 3 feet 11 inches (1.19 m) wide and 4 feet 3.5 inches (1.31 m) high and weighed 2.2 long tons (2.46 short tons; 2.24 t).[60] Typical Deutz mine engines in 1906 were rated at 8 to 12 hp (6.0 to 8.9 kW).[61] By this time, double-cylinder 18 hp (13 kW). engines built by Wolseley Motors were being used in South African mines.[62] By 1914, Whitcomb Locomotive Works, Vulcan Iron Works, and Milwaukee Locomotive Manufacturing Co. (later merged with Whitcomb) were making gasoline mining locomotives in the United States with 4 and 6 cylinder engines.[63]
Late 19th and early 20th century mine railway locomotives were operated with petrol benzene and alcohol / benzene mixtures.[64] Although such engines were initially used in metal mines, they were in routine use in coal mines by 1910. Firedamp safety was achieved by wire gauze shields over intake and exhaust ports as well as cooling water injection in the exhaust system. Bubbling the exhaust through a water bath also greatly reduced noxious fumes.[63][65]
For safety (noxious fumes as well as flammability of the fuel) modern mine railway internal combustion locomotives are only operated using diesel fuel. Catalytic scrubbers reduce carbon monoxide. Other locomotives are electric, either battery or trolley.
Battery-electric locomotives
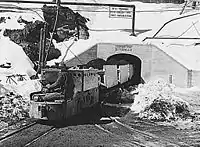
Battery powered locomotives and systems solved many of the potential problems that combustion engines present, especially regarding fumes, ventilation and heat generation. Compared to simple electric locomotives, battery locomotives do not need trolley wire strung over each track. However, batteries are heavy items which used to require long periods of charge to produce relatively short periods of full-power operation, resulting in either restricted operations or the need for the doubling-up of equipment purchasing.
In the 19th century, there was considerable speculation about the potential use of battery locomotives in mines.[66][67][68] By 1899, Baldwin-Westinghouse had delivered an experimental battery locomotive to a Virginia mine; battery recharging occurred whenever the locomotive was running under trolley wire, while it could run from battery when working on temporary trackage near the face. This locomotive was eventually successful, but only after the voltage on the trolley system was stabilized.[69] A Siemens and Haske pure storage battery locomotive was in use in a coal mine in Gelsenkirchen (Germany) by 1904.[70]
One problem with battery locomotives was battery replacement. This was simplified by use of removable battery boxes. Eventually, battery boxes were developed that included wheels so that they could be rolled off of the locomotive.[71] While the initial motivation had to do with battery maintenance, the primary use for this idea was at charging stations where a discharged battery box could be rolled off and replaced with a freshly charged box.[72]
While popular, battery systems were often practically restricted to mines where systems were short, and moving relatively low-density ore which could explode easily. Today, heavy-duty batteries provide full-shift (8 hours) operations with one or more spare batteries charging.
In operation
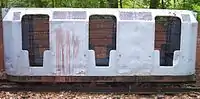
Until 1995 the largest single, narrow gauge, above-ground, mine and coal railway network in Europe was in the Leipzig-Altenburg lignite field in Germany. It had 726 kilometres (451 mi) of 900 mm (2 ft 11 7⁄16 in) – the largest 900 mm (2 ft 11 7⁄16 in) network in existence. Of this, about 215 kilometres was removable track inside the actual pits and 511 kilometres was fixed track for the transportation of coal to the main rail network.
The last 900 mm (2 ft 11 7⁄16 in) gauge mine railway in the German state of Saxony, a major mining area in central Europe, was closed in 1999 at the Zwenkau Mine in Leipzig. Once a very extensive railway network, towards the end it only had 70 kilometres (43 mi) of movable 900 mm (2 ft 11 7⁄16 in) track and 90 kilometres (56 mi) of 900 mm (2 ft 11 7⁄16 in) fixed railway track within the Zwenkau open cast mine site itself, as well as a 20 kilometres (12 mi), standard gauge, link railway for the coal trains to the power stations (1995–1999). The closure of this mine marked the end of the history of 900 mm (2 ft 11 7⁄16 in) mine railways in the lignite mines of Saxony. In December 1999, the last 900 mm (2 ft 11 7⁄16 in)railway in the Central German coal mining field in Lusatia was closed.
In the United States, Consol Energy's Shoemaker Mine, covering a large area east of Benwood, West Virginia was the last underground coal mine to use rail haulage. Starting in 2006, 12 miles of underground conveyor belt and 2.5 miles of above ground conveyor belt were installed. The last load of coal was hauled by rail in January 2010.[73]
Museum and heritage railways
A remnant of the coal railways in the Leipzig-Altenburg Lignite Field may be visited and operated as a museum railway. Regular museum trains also run on the line from Meuselwitz via Haselbach to Regis-Breitingen.
Mine railways in visitor mines
Austria
- Pradeisstollen, Radmer in the Styria
- Schwaz Silver Mine
Germany
- Hesse
- Grube Fortuna, Solms, visitor mine with working shaft, field and pit railway museum with circular track, 600 mm (1 ft 11 5⁄8 in), 2.3 km (1.4 mi) long
- Lower Saxony
- Barsinghausen, Klosterstollen, 600 mm (1 ft 11 5⁄8 in), 13 km (8.1 mi) long
- Clausthal-Zellerfeld–Clausthal, Ottiliae Shaft, open pit railway to the old station in Clausthal, 600 mm (1 ft 11 5⁄8 in), 2.2 km (1.4 mi)
- Goslar, Rammelsberg
- Langelsheim–Lautenthal, Lautenthals Glück Pit
- North Rhine-Westphalia
- Bestwig–Ramsbeck, Ramsbeck Ore Mine
- Kleinenbremen, Kleinenbremen Visitor Mine
- Rhineland-Palatinate
- Steinebach/Sieg, Bindweide Pit
- Saxony
- Annaberg-Buchholz, Markus Röhling Stolln, 600 mm (1 ft 11 5⁄8 in)
- Ehrenfriedersdorf, Sauberg (underground section only), 600 mm (1 ft 11 5⁄8 in)
- Saxony-Anhalt
- Elbingerode (Harz), Drei Kronen & Ehrt visitor mine, 600 mm (1 ft 11 5⁄8 in)
- Sangerhausen–Wettelrode, Röhrigschacht show mine
- Thuringia
- Ilfeld–Netzkater, Rabensteiner Stollen, 600 mm (1 ft 11 5⁄8 in)
- Luxembourg
- Minièresbunn, Fond-de-Gras, 700 mm (2 ft 3 9⁄16 in), 4 km (2.5 mi) long
- National Museum of Luxembourg Iron Ore Mines, circular track
See also
- Industrial railway
- Granite Railway
- Mantrip (shuttle for transporting miners)
- Mine car
- Minecart
- Plateway
- Quarry tub
- Rail profile
- Rail tracks
- Wagonway
References
- Ellis, Iain (2006). Ellis' British Railway Engineering Encyclopaedia. Lulu.com. ISBN 978-1-8472-8643-7.
- culture noted and terms listed: culm.
- Clark, Ronald W. (1985). Works of Man: History of Invention and Engineering, From the Pyramids to the Space Shuttle (1st American Edition. 8"x10" Hard cover ed.). Viking Penguin, Inc., New York, U.S.A., (1985). pp. 352 (indexed). ISBN 9780670804832.
- Georgius Agricola (trans Hoover), De re metallica (1913), p. 156
- The miners called the wagons Hund — "dog" — from the noise they made on the tracks.Lee, Charles E (1943). The Evolution of Railways. Railway Gazette (2 ed.). London. p. 16. OCLC 1591369.
- Warren Allison, Samuel Murphy, and Richard Smith, 'An Early Railway in the German Mines of Caldbeck' in G. Boyes (ed.), Early Railways 4: Papers from the 4th International Early Railways Conference 2008 (Six Martlets, Sudbury, 2010), 52–69.
- Lewis, Early wooden railways, 8-10.
- Peter King, 'The First Shropshire Railways' in G. Boyes (ed.), Early Railways 4: Papers from the 4th International Early Railways Conference 2008 (Six Martlets, Sudbury, 2010), 70–84.
- M. J. T. Lewis, Early Wooden railways.
- Ransom, Philip (1981). The archaeology of railways. Tadworth, England: World's Work. p. 268. ISBN 978-0-437-14401-0.
- James Burke (science historian), Connections (1985), pages: 136-137, pbk: 304 pages, Little Brown & Co., New York, ISBN
- George Stephenson#Early locomotives
- "Jim the Mule Boy (Film Short, title @IMDB)". Edison Film Company. 28 March 1911.
This film is run on a video loop with other historical programming in the Anthracite Coal Mining Museum, Coaldale, Pennsylvania
- Lowrie, Raymond L., ed. (2002). "Excavation, Loading, and Material Transport". SME Mining Reference Handbook. Society for Mining, Metallurgy and Exploration. p. 232. Retrieved 9 October 2012.
- Stoek, H. H.; Fleming, J. R.; Hoskin, A. J. (July 1922). A Study of Coal Mine Haulage in Illinois. Engineering Experiment Station Bulletin. 132. University of Illinois. pp. 102–103. Retrieved 22 June 2011.
- "II, Haulage". Mining. Wallgate, Wigan, England: Stowager and Sons. 2 December 1893.
- Fay, Albert H. (1920). "Car". A Glossary of the Mining and Mineral Industry. U.S. Department of the Interior. p. 131.
- H.H. Stoek, J.R. Fleming, A.J. Hoskin, A Study of Coal Mine Haulage in Illinois, Bulletin 132, University of Illinois Engineering Experiment Station, July 1922; pages 15-16.
- H.H. Stoek, J.R. Fleming, A.J. Hoskin, A Study of Coal Mine Haulage in Illinois, Bulletin 132, University of Illinois Engineering Experiment Station, July 1922; page 70 and page 12.
- Thompson, Ceri (2008). Harnessed: colliery horses in Wales. Cardiff: National Museum Wales. p. 66. ISBN 978-0-7200-0591-2.
- Fred Brenckman, Official Commonwealth Historian (1884). HISTORY OF CARBON COUNTY PENNSYLVANIA (Archive.org project pdf e-reprint 2nd edition, 627 pages, (1913) ed.). Also Containing a Separate Account of the Several Boroughs and Townships in the County, J. Nungesser, Harrisburg, Pennsylvania.
- Bartholomew, Ann M.; Metz, Lance E.; Kneis, Michael (1989). DELAWARE and LEHIGH CANALS, 158 pages (First ed.). Easton, Pennsylvania: Center for Canal History and Technology, Hugh Moore Historical Park and Museum, Inc. pp. 4–5. ISBN 0930973097. LCCN 89-25150.
- Francis M. Fultz, An Iowa Coal Mine, Chapter V of Out of Door Studies in Geography, I, The Making of the Surface and Soils of the Upper Mississippi Region, 1908; pages 97-105, see page 101.
- Sydney F. Walker, Electrical Mining Notes, Electrical Review, Vol. 48, No. 1, January, 1906.
- Wilhelm Hildenbrand, Section II, The Simple Engine Plane, The Underground Haulage of Coal by Wire Ropes, John A. Roebling's Sons Co., 1884; page 16.
- Nicholas Wood, Chapter IV – Motive power, Section III – Steam-engine fixed upon ascending planes, A Practical Treatise on Railr-Roads, Longman, Rees, Orme, Brown and Green, London, 1832; page 114.
- Wilhelm Hildenbrand, Section III, The Tail Rope System, The Underground Haulage of Coal by Wire Ropes, John A. Roebling's Sons Co., 1884; page 22.
- Thomas J. Waters, Rope Haulage at the Westport Coal Company's Coalbrookdale Colliery, Westport, Papers read at the Mining Conference held at Dunedin, March 1890, George Didsbury, Government Printer, Wellington, NZ, 1890; page 12
- Report of the Tail-Rope Committee, Transactions of the North of England Institute of Mining Engineers, vol. XVII, Appendix I (1867-8), Newcastle upon Tyne, 1868.
- Carl Volk, Haulage and Winding Appliances used in Mines, Scott, Greenwood & Co. London, 1903; page 113.
- Wilhelm Hildenbrand, Section IV, The Endless Rope System, The Underground Haulage of Coal by Wire Ropes, John A. Roebling's Sons Co., 1884; page 37.
- Mine Haulage, The Elements of Mining Engineering, Vol. III, The Colliery Engineer Co., Scranton, 1900; paragraphs 2436-2437.
- Light Locomotives, Saward's Coal Trade Journal, July 29, 1874; pages 39-40.
- Porter Bell & Co. 1873 advertisement.
- Baldwin Locomotive Works, Illustrated Catalog of Locomotives, second ed., Burnham, Parry, Williams & Co., Philadelphia, 1881; page 47.
- Mine Locomotives for Gold Mines, Railroad Gazette, October 12, 1877; page 453. Has good scale drawings.
- A Novel Mining Locomotive, The Locomotive Magazine, Vol. IX, No. 125 (Oct. 10, 1903); pages 214-215. Includes photo.
- H.K. Porter Co., Advertisement, Engineering Magazine, Vol. XXVII, No. 6 (September 1909); advertising page 111.
- Vulcan Locomotives, Vulcan Iron Works, Wilkes-Barre, 1911; pages 70, 72, 86 and 105.
- H.H. Stoek, J.R. Fleming, A.J. Hoskin, A Study of Coal Mine Haulage in Illinois, Bulletin 132, University of Illinois Engineering Experiment Station, July 1922; page 17.
- The Mining Catalog (Metal and Quarry Ed.), Keystone, Pittsburgh, 1921; pages 273 (Baldwin) and 275 (Vulcan).
- Compressed Air Locomotives, Brotherhood of Locomotive Engineers Monthly Journal; vol. X, no. 1 (January, 1876); page 16.
- Compressed Air Locomotives, Record of Recent Construction No. 46, Baldwin Locomotive Works, 1904; page 14, mentions the first delivery; page 9 shows storage and working pressures; pages 13-14 discuss operation at 2000 psi.
- Professional Notes, Compressed Air Mine Locomotives, The School of Mines Quarterly, vol. II, no. 4 (May 1881), Columbia College, New York; pages 215-216.
- Compressed Air Mine Locomotive, The Colliery Engineer, vol. XII, no. 8 (March, 1892); page 183.
- Vulcan Locomotives, Vulcan Iron Works, Wilkes-Barre, 1911; pages 74-78 and 97.
- David R. Shearer, Chapger VI: Direct-Current Power Plant Design, Electricity in Coal Mining, McGraw-Hill, New York, 1914.
- F.M.F. Cazin, How can Mining and Metallurgical Industry be Benefited by Electric Contrivances? Part II, [ Electric Power], Vol III, No. 35, (Nov. 1891); pages 405-409 (see pages 408-409 for a discussion of early German and U.S. electric mine haulage).
- Schlesinger Electric Locomotive Motor, The Electrical World, Vol. XI, No. 8 (Feb. 25, 1888); page 88. Includes pictures of the traction motor.
- The Electric Railway in the Lykens Valley Coal Mine, The Electrical World, Vol. XI, No. 24 (June 16, 1888); page 303. Includes a picture of the locomotive.
- The Union Electric Company, Philadelphia (Advertisement), The Electrical World, Vol. XI, No. 26 (June 30, 1888); page xv. Includes locomotive weights.
- T. C, Martin and Joseph Wetzler, Chapter XIII: Latest American Motors and Motor Systems, [The Electric Motor and its Applications, third ed.]; W. J. Johnston, New York, 1891; pages 218-224. Includes good illustrations of the Pioneer.
- George Gibbs, The Electric Locomotive for Mine Haulage, Cassier's Magazine, vol. 22, no. 3 (July 1902); pages 323-343. Well illustrated.
- Seward Mighell, Locomotive, U.S. Patent 732,768, granted July 7, 1903.
- Kenneth Rushton, Reel Attachment for Mine Locomotives, U.S. Patent 737,491, granted Aug. 25. 1903.
- Cable-Reel Locomotives, The Coal Miners' Pocketbook, 11th Ed., McGraw-Hill, New York, 1916; page 826-827.
- W. E. Hamilton, Locomotive Car Puller, U.S. Patent 765,833, granted July 26, 1904.
- Crab Locomotives, The Coal Miners' Pocketbook, 11th Ed., McGraw-Hill, New York, 1916; page 827.
- A Benzine Locomotive for use in Mines, The Petroleum Industrial and Technical Review, vol. 2, no. 68 (June 23, 1900); page 388.
- Benzine Locomotive, English Mechanic and World of Science, No. 1713 (Jan 21, 1898); pages 532-533.
- Benzine Locomotives for Mining Purposes, The Petroleum Review, vol. XIV (New Series), no. 375 (June 23, 1906); page 411. Includes photos.
- A Petroleum-Driven Mining Locomotive, The Locomotive Magazine, Vol. IX, No. 119 (Aug. 29, 1903); page 128. Includes scale drawings.
- Joseph A. Anglada, Gasoline Locomotives for Mines, The Gas Engine, Vol. XVI, No. 2 (Feb. 1914); pages 100-103. Includes photos.
- Heise-Herbst, Bergbaukunde, Springer-Verlag 1910, p. 345 ff.
- A Unique English Internal Combustion Mining Locomotive, Mining Science, Vol. LXI, No. 1573 (Mar. 24, 1910); page 272. Includes photo.
- Electric Underground Haulage, The Coal Trade Journal, Oct. 3, 1894; page 726.
- J. S. Doe, The Iser vs. the Waser, Proceedings of the Seventeenth Annual Meeting of the Ohio Institute of Mining Engineers, Jan 19-21, 1898, Columbus, published as The Ohio Mining Journal, No. 27, (1899); pages 60-66, see particularly page 62.
- Francis A. Pocock, Accumulators and Mining, presented at the New York Meeting, Sept. 1890, Trans. Amer. Inst. of Mining Engineers, Vol. XIX (1891); pages 278-282.
- Harry K. Myers, A Combined Trolley and Storage Battery Locomotive for Mines, American Electrician, Vol. XI, No. 11 (Nov. 1899); page 512-513.
- J. F. Gairns, Industrial Locomotives for Mining, Factory and Allied Uses, part III, Cassier's Magazine, Vol. XXVI, No. 5 (Sept. 1904); pages 474-496; see photo on page page 474, text on page 489.
- Eugene W. Schellentrager and Bradley E. Clarkson, Storage-Battery Locomotive, U.S. Patent 1,413,686, granted April 25, 1922.
- William T. Petterson, Locomotive Battery Changing Mechanism, U.S. Patent 2,970,550, granted Feb. 7, 1961.
- Shoemaker Mine banks on future, The Times Leader, Martin's Ferry Ohio, Jan 28, 2010.
External links
![]() |
Wikimedia Commons has media related to Mining railways. |