Refrigerant
A refrigerant is a substance or mixture, usually a fluid, used in a heat pump and refrigeration cycle. In most cycles it undergoes phase transitions from a liquid to a gas and back again. Many working fluids have been used for such purposes. Fluorocarbons, especially chlorofluorocarbons, became commonplace in the 20th century, but they are being phased out because of their ozone depletion effects. Other common refrigerants used in various applications are ammonia, sulfur dioxide, and non-halogenated hydrocarbons such as propane.[1]
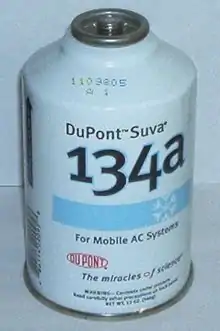
Desirable properties
The ideal working fluid or often called refrigerant would have favorable thermodynamic properties, be noncorrosive to mechanical components, and be safe, including freedom from toxicity and flammability. It would not cause ozone depletion or climate change. Since different fluids have the desired traits in different degree, choice is a matter of trade-offs.
The desired thermodynamic properties are a boiling point somewhat below the target temperature, a high heat of vaporization, a moderate density in liquid form, a relatively high density in gaseous form, and a high critical temperature. Since boiling point and gas density are affected by pressure, refrigerants may be made more suitable for a particular application by appropriate choice of operating pressures.
Environmental challenges
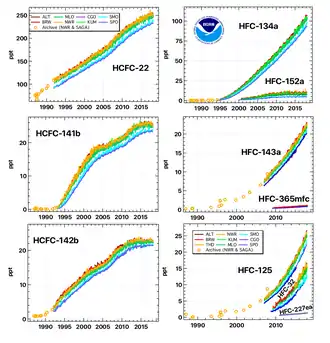
The inert nature of many haloalkanes, chlorofluorocarbons (CFC) and hydrochlorofluorocarbons (HCFC), particularly CFC-11 and CFC-12, made them preferred choices among refrigerants for many years because of their non-flammability and non-toxicity. However, their long lifetimes in the atmosphere along with their corresponding global warming potential and ozone depletion potential raised concerns about their usage. In order from the highest to the lowest potential of ozone depletion are: Bromochlorofluorocarbon, CFC then HCFC.
The discovery of stratospheric ozone holes over polar regions in the early 1980's led to a transition to hydrofluorocarbons (HFCs) which are not-ozone depleting. These include R-134a, R-143a, and R-410a (a 50/50 blend of R-125/R-32), These refrigerants still have global warming potentials thousands of times greater than CO2 and atmospheric lifetimes that can extend for decades.
New refrigerants were developed in the early 21st century that are safer for the environment, but their introduction has been held up due to concerns over toxicity and flammability.[2] HFCs are now being replaced in markets where leaks are likely by using a fourth generation of refrigerants, most prominently HFO-1234yf trademarked by Chemours as Opteon-YF, that have global warming potentials much closer to that of CO2.
As of year 2019, CFCs, HCFCs, and HFCs are responsible for about one-tenth of the direct radiative forcing from all long-lived anthropogenic greenhouse gases.[3] A 2018 study by the nonprofit organization "Drawdown" put proper refrigerant management and disposal at the very top of the list of climate impact solutions, with an impact equivalent to eliminating over 17 years of US carbon dioxide emissions.[4]
Compared to halogenated refrigerants, hydrocarbons like isobutane (R-600a) and propane (R-290) offer several advantages: low cost and widely available, zero ozone depletion potential and very low global warming potential. They also have good energy efficiency, but are flammable and can form an explosive mixture with air if a leak occurs. Despite the flammability, they are increasingly used in domestic refrigerators. EU and US regulations set maximum charges of 57 or 150 grams of refrigerant, keeping the concentration in a standard kitchen below 20% of the lower explosive limit. The LEL can be exceeded inside the appliance, so no potential ignition sources can be present. Switches must be placed outside the refrigerated compartment or replaced by sealed versions, and only spark-free fans can be used. In 2010, about one-third of all household refrigerators and freezers manufactured globally used isobutane or an isobutane/propane blend, and this was expected to increase to 75% by 2020.[5]
History
Early mechanical refrigeration systems employed sulfur dioxide, methyl chloride or ammonia. Being toxic, sulfur dioxide and methyl chloride rapidly disappeared from the market with the introduction of CFCs. Occasionally, one may encounter older machines with methyl formate, methyl chloride, or dichloromethane (called carrene in the trade).
Chlorofluorocarbons were little used for refrigeration until better synthesis methods, developed in the 1950s, reduced their cost. Their domination of the market was called into question in the 1980s by concerns about depletion of the ozone layer.
Following legislative regulations on ozone depleting chlorofluorocarbons (CFCs) and hydrochlorofluorocarbons (HCFCs), substances used as substitute refrigerants such as perfluorocarbons (FCs) and hydrofluorocarbons (HFCs) have also come under criticism. They are currently subject to prohibition discussions on account of their harmful effect on the climate. In 1997, FCs and HFCs were included in the Kyoto Protocol to the Framework Convention on Climate Change. In 2006, the EU adopted a Regulation on fluorinated greenhouse gases, which makes stipulations regarding the use of FCs and HFCs with the intention of reducing their emissions. The provisions do not affect climate-neutral refrigerants. Hydrocarbons are seeing increasing use as refrigerants.
Uses
Refrigerants such as ammonia (R717), carbon dioxide and non-halogenated hydrocarbons do not deplete the ozone layer and have no (ammonia) or only a low (carbon dioxide, hydrocarbons) global warming potential. They are used in air-conditioning systems for buildings, in sport and leisure facilities, in the chemical/pharmaceutical industry, in the automotive industry and above all in the food industry (production, storage, marine shipping, retailing). In these settings their toxicity is less a concern than in home equipment.
Emissions from automobile air conditioning are a growing concern because of their impact on climate change. From 2011 on, the European Union will phase out refrigerants with a global warming potential (GWP) of more than 150 in automotive air conditioning (GWP = 100 year warming potential of one kilogram of a gas relative to one kilogram of CO2). This will ban potent greenhouse gases such as the refrigerant HFC-134a (also known as R-134a in North America) —which has a GWP of 1410—to promote safe and energy-efficient refrigerants.
One of the most promising alternatives is CO2 (R-744). Carbon dioxide is non-flammable, non-ozone depleting, has a global warming potential of 1. R-744 can be used as a working fluid in climate control systems for cars, residential air conditioning, hot water pumps, commercial refrigeration, and vending machines. R12 is compatible with mineral oil, while R134a is compatible with synthetic oil that contains esters. GM announced that it would start using "hydrofluoroolefin", HFO-1234yf, in all of its brands by 2013.[6] Dimethyl ether (DME) is also gaining popularity as a refrigerant,[7] but like propane, it is also dangerously flammable.
Some refrigerants are seeing rising use as recreational drugs, leading to an extremely dangerous phenomenon known as inhalant abuse.[8]
Disposal
Under Section 608 of the United States' Clean Air Act it is illegal to knowingly release refrigerants into the atmosphere.[9] SNAP approved hydrocarbon substitutes (isobutane and propane: R600a, R441a and R290), ammonia and CO2 are exempt from the venting prohibition.[10]
When refrigerants are removed they should be recycled to clean out any contaminants and return them to a usable condition. Refrigerants should never be mixed together outside of facilities licensed to do so for the purpose of producing blends. Some refrigerants must be managed as hazardous waste even if recycled, and special precautions are required for their transport, depending on the legislation of the country's government.
Various refrigerant reclamation methods are in use to recover refrigerants for reuse.[11]
Refrigerants by class and R-number
Refrigerants may be divided into three classes according to their manner of absorption or extraction of heat from the substances to be refrigerated:
- Class 1: This class includes refrigerants that cool by phase change (typically boiling), using the refrigerant's latent heat.
- Class 2: These refrigerants cool by temperature change or 'sensible heat', the quantity of heat being the specific heat capacity x the temperature change. They are air, calcium chloride brine, sodium chloride brine, alcohol, and similar nonfreezing solutions. The purpose of Class 2 refrigerants is to receive a reduction of temperature from Class 1 refrigerants and convey this lower temperature to the area to be cooled.
- Class 3: This group consists of solutions that contain absorbed vapors of liquefiable agents or refrigerating media. These solutions function by nature of their ability to carry liquefiable vapors, which produce a cooling effect by the absorption of their heat of solution. They can also be classified into many categories.
The R-# numbering system was developed by DuPont (which owned the Freon trademark), and systematically identifies the molecular structure of refrigerants made with a single halogenated hydrocarbon. The meaning of the codes is as follows:
- For saturated hydrocarbons, subtracting 90 from the concatenated numbers of carbon, hydrogen and fluorine atoms, respectively gives the assigned R#.[12]
- If bromine is present, the number is followed by a capital B and then the number of bromine atoms.
- Remaining bonds not accounted for are occupied by chlorine atoms.
- A suffix of a lower-case letter a, b, or c indicates increasingly unsymmetrical isomers.
For example, R-134a has 2 carbon atoms, 2 hydrogen atoms, and 4 fluorine atoms, an empirical formula of tetrafluoroethane. The "a" suffix indicates that the isomer is unbalanced by one atom, giving 1,1,1,2-Tetrafluoroethane. R-134 (without the "a" suffix) would have a molecular structure of 1,1,2,2-Tetrafluoroethane.
- The R-400 series is made up of zeotropic blends (those where the boiling point of constituent compounds differs enough to lead to changes in relative concentration because of fractional distillation) and the R-500 series is made up of so-called azeotropic blends. The rightmost digit is assigned arbitrarily by ASHRAE, an industry standards organization.
- The R-700 series is made up of non-organic refrigerants, also designated by ASHRAE.
The same numbers are used with an R- prefix for generic refrigerants, with a "Propellant" prefix (e.g., "Propellant 12") for the same chemical used as a propellant for an aerosol spray, and with trade names for the compounds, such as "Freon 12". Recently, a practice of using abbreviations HFC- for hydrofluorocarbons, CFC- for chlorofluorocarbons, and HCFC- for hydrochlorofluorocarbons has arisen, because of the regulatory differences among these groups.
Notable blends
Below are some notable blended HFC mixtures. There exist many more (see list of refrigerants). All R-400 (R-4xx) and R-500 (R-5xx) hydroflurocarbons are blends, as noted above.
- R-401A is a HCFC zeotropic blend of R-22, R-152a, and R-124. It is designed as a replacement for R-12.[13]
- R-404A is a HFC "nearly azeotropic" blend of 52 wt.% R-143a, 44 wt.% R-125, and 4 wt.% R-134a. It is designed as a replacement of R-22 and R-502 CFC. Its boiling point at normal pressure is −46.5 °C, its liquid density is 0.485 g/cm3.[14]
- R-406A is a zeotropic blend of 55 wt.% R-22, 4 wt.% R-600a, and 41 wt.% R-142b.
- R-407A is a HFC zeotropic blend of 20 wt.% R-32, 40 wt.% R-125, and 40 wt.% R-134a.[15]
- R-407C is a zeotropic hydrofluorocarbon blend of R-32, R-125, and R-134a. The R-32 serves to provide the heat capacity, R-125 decreases flammability, R-134a reduces pressure.[16]
- R-408A is a zeotropic HCFC blend of R-22, R-125, and R-143a. It is a substitute for R-502. Its boiling point is −44.4 °C.[17]
- R-409A is a zeotropic HCFC blend of R-22, R-124, and R-142b. Its boiling point is −35.3 °C. Its critical temperature is 109.4 °C.[18]
- R-410A is a near-azeotropic blend of R-32 and R-125. The US Environmental Protection Agency recognizes it as an acceptable substitute for R-22 in household and light commercial air conditioning systems.[19] It appears to have gained widespread market acceptance under several trade names.
- R-438A another HFC blended replacement for R-22, with five components: R-32, R-125/R-134a, R-600, and R-601a, blended in respective ratios 8.5+.5,−1.5%; 45±1.5%; 44.2±1.5%; 1.7+.1,−.2%; 0.6+.1,−.2%. The mean molecular weight of this mix is 99, resulting in the tradename ISCEON MO99 from manufacturer DuPont (a line of blended HFC products developed initially by Rhodia, and sold to DuPont).[20][21]
- R-500 is an azeotropic blend of 73.8 wt.% R-12 and 26.2 wt.% of R-152a.
- R-502 is an azeotropic blend of R-22 and R-115.
- R-507 is a HFC zeotropic blend of R-143a and R-125.
Air as a refrigerant
Air has been used for residential,[22] automobile, and piston- and turbine-powered aircraft[23][24] air-conditioning and/or cooling. Air is not more widely used as a general-purpose refrigerant because there is no change of phase, and is therefore too inefficient to be practical in most applications.[22] It has been suggested that with suitable compression and expansion technology, air can be a practical (albeit not the most efficient) refrigerant, free of the possibility of environmental contamination or damage,[22] and almost completely[25] harmless to plants and animals.
However, an explosion could result from vapors or atomized refrigerant-type compressor lubricating oils being compressed together with air, in a process similar to a diesel engine.
See also
- Brine (Refrigerant)
- Eurammon - initiative for natural refrigerants
- Industrial gas
- List of refrigerants
- Refrigerant reclamation
- Working fluids
References
- Siegfried Haaf, Helmut Henrici "Refrigeration Technology" in Ullmann's Encyclopedia of Industrial Chemistry, 2002, Wiley-VCH, doi:10.1002/14356007.b03_19
- Rosenthal, Elisabeth; Lehren, Andrew (June 20, 2011). "Relief in Every Window, but Global Worry Too". The New York Times. Retrieved June 21, 2012.
- Butler J. and Montzka S. (2020). "The NOAA Annual Greenhouse Gas Index (AGGI)". NOAA Global Monitoring Laboratory/Earth System Research Laboratories.
- Berwald, Juli (2019-04-29). "One overlooked way to fight climate change? Dispose of old CFCs". National Geographic - Environment. Retrieved 2019-04-30.
- "Protection of Stratospheric Ozone: Hydrocarbon Refrigerants" (PDF). Environment Protection Agency. Retrieved 5 August 2018.
- GM First to Market Greenhouse Gas-Friendly Air Conditioning Refrigerant in U.S.
- 101110
- Harris, Catharine. "Anti-inhalant Abuse Campaign Targets Building Codes: 'Huffing’ of Air Conditioning Refrigerant a Dangerous Risk." The Nation's Health. American Public Health Association, 2010. Web. 05 Dec. 2010. http://thenationshealth.aphapublications.org/content/39/4/20.extract.
- "Frequently Asked Questions on Section 608". Environment Protection Agency. Retrieved 20 December 2013.
- "US EPA lifts venting prohibition for SNAP approved hydrocarbons". Retrieved 5 August 2018.
- Guide to Effective Refrigerant Recovery Ritchie Engineering Company
- "Numbering Scheme for Ozone-Depleting Substances and their Substitutes". Retrieved 25 December 2015.
- HCFC - R401A
- "Refrigerant gas R-404A". Cameo Chemicals. NOAA.
- "Refrigerant gas R-407A". Cameo Chemicals. NOAA.
- "Comparison of R407C and R417A heat transfer coefficients and pressure drops during flow boiling in a horizontal smooth tube". ResearchGate. Retrieved 2015-09-09.
- "Mixed refrigerants, R-408A page". Archived from the original on 2006-11-26.
- Mixed refrigerants, R-409A page
- "Significant New Alternatives Policy (SNAP) Program". Archived from the original on 1 June 2002. Retrieved 25 December 2015.
- "This page has moved". Retrieved 25 December 2015.
- Air as a refrigerant in air conditioning systems in buildings.
- Air cycle machine.
- Turboexpander.
- Current air cooling methods release a trivial amount of oil or other lubricant into the atmosphere.